Pintar motores de vehículos agrícolas
Los equipos de Graco desempeñan un papel clave en una nueva línea de recubrimiento de motores automáticos en la planta de MANTA Group en Italia.
MANTA Group, con sede en Foggia, Italia, ha centrado su actividad en el montaje y recubrimiento de componentes aeroespaciales y automotrices durante más de 30 años. En 2021, se confió a la empresa la tarea de pintar motores de maquinaria agrícola. Para llevar a cabo esta tarea, MANTA seleccionó un grupo de proveedores para crear una línea de pintura totalmente digital, conforme a la Industria 4.0, automatizada, flexible y rápida.
Los objetivos de la nueva línea de recubrimiento eran desafiantes. Tendría que permitir pintar más de 700 variantes de motor en cuatro colores diferentes, con una capacidad de 85 000 motores al año. También tenía que estar totalmente integrada a nivel digital con el sistema de gestión de la empresa para permitir una supervisión minuciosa de cada etapa de recubrimiento y el cumplimiento de los requisitos de calidad.
Gaiotto, Savim y CM Automazione participaron en los aspectos relacionados con la ingeniería de la planta y Graco fue responsable de la aplicación de pintura. El sistema de pintura de base acuosa de una sola capa que se va a aplicar a los motores fue validado por un laboratorio externo (CRF) antes del inicio de la producción.
Colaboradores perfectos
La planta de pintura fue construida por Savim (Arbizzano, Verona, Italia), está equipada con robots Gaiotto e integra un transportador paso a paso XD45/59 diseñado y proporcionado por CM Automazione (Giussano, Monza e Brianza, Italia). La línea admite hasta 116 unidades de manipulación con una capacidad de carga máxima de 850 kg cada una. A pleno rendimiento, la línea es capaz de pintar 370 motores al día.
Para el suministro de alimentación de pintura, el equipo de aplicación de pintura y el sistema de cambio de color, MANTA confió en Graco y su integrador Comaind (San Giovanni Lupatoto, Verona, Italia), cuya colaboración fue fundamental en una de las fases más críticas de este proyecto.
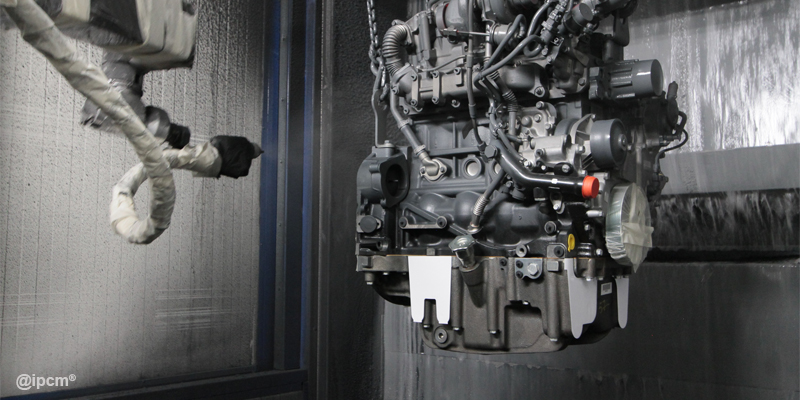
Un proceso optimizado
Cada motor pasa por varias etapas de preparación: enmascaramiento, pretratamiento químico con desengrase fosfatado, limpieza con agua desmineralizada y secado en tres pasos (túnel de secado previo, soplado robotizado y horno a 90 °C) antes de que los motores pasen por una zona de enfriamiento.
A continuación, la pintura líquida se aplica en dos cabinas de agua presurizadas con cortina y con control de temperatura y humedad, suministradas por Savim, cada una con un robot Gaiotto articulado que gira 180° y pinta un lado del motor. El espesor mínimo aplicado es de 50 micras. Se utiliza una tercera cabina manual para retoques. La línea termina con un túnel de secado y un horno que seca 50 motores a 100 °C durante 90 minutos. Después, los motores se trasladan a una estación de calidad en línea para la aprobación final.
El sistema de aplicación de pintura
«Diseñamos el sistema de alimentación y aplicación de pintura junto con Gaiotto para gestionar los cuatro colores utilizados por MANTA», explica Davide Galvani de Comaind. «El más utilizado es el gris, que representa casi el 90 % de la producción. Los otros tres colores son el amarillo, el gris Perkins y el transparente, que suponen el 10 % restante de los volúmenes».
La planificación del recubrimiento no se realiza por lotes, sino por cada motor individual. Esto significó diseñar un sistema de cambio de color muy rápido de solo 30 segundos. La unidad de gestión de pintura está equipada con un recipiente de 1000 kg para el color gris y bidones de 200 litros para los otros tintes. La pintura se mantiene agitada mediante un agitador eléctrico con certificación ATEX, con paletas extensibles y un sistema de llenado conectado a un tanque de 100 litros donde una bomba Endura-Flo de Graco hace circular la pintura a una presión de 2,5-3 bar. Este tanque alimenta previamente el dosificador multicomponente PD1K de Graco equipado con cuatro bombas separadas, una para cada color, para garantizar la máxima velocidad de cambio de color en el robot.
Además, se realiza una filtración con una malla de 60 en el producto recirculado. El dispositivo PD1K también tiene su propia unidad de filtración en la salida de la pistola. Los dos robots de recubrimiento están equipados con dos pistolas automáticas AirPro con tecnología compatible de Graco cada una. Una pistola maneja la pintura gris, mientras que la otra cuenta con válvulas de cambio de color colocadas a unos 40-50 cm de la pistola, casi en la muñeca del robot. Una válvula es para lavar el circuito y las otras tres son para los tintes. La unidad de gestión de pintura también alimenta previamente la cabina de retoques donde hay disponible una pistola de cada color que se activa con el color correcto dependiendo del motor entrante.
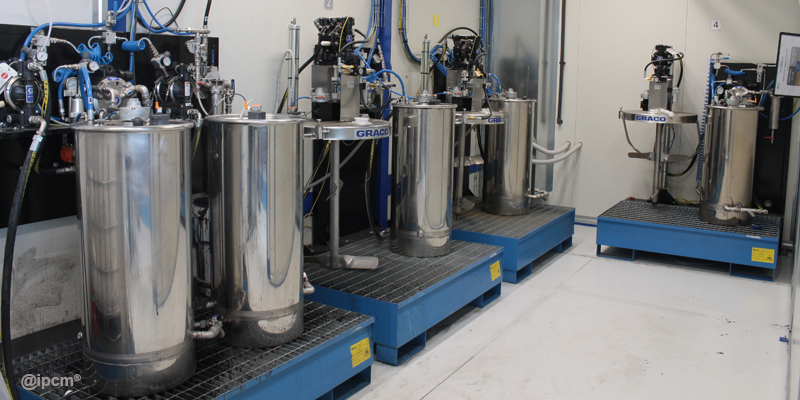
PD1K de Graco en el corazón del sistema
«Hemos seleccionado el dosificador multicomponente PD1K de Graco, ya que permite controlar directamente el flujo de pintura en la pistola y ajustarlo en función del movimiento del robot durante la etapa de pintura», añade Galvani. «Esta unidad también permite analizar los parámetros técnicos/de producción y las interfaces con el sistema 4.0 de la línea».
Gracias a su tecnología única de accionamiento de pistón con codificador y a sus válvulas de control activas, el PD1K proporciona una precisión en la proporción de mezcla dentro del 1 % que asegura una dosificación uniforme y exacta en cada momento. Mantiene esta precisión excepcional independientemente de la altura piezométrica, la elevación, la viscosidad del material, la temperatura o el accionamiento de la pistola.
Además, al acercar el punto de mezcla a la pistola, disminuye la zona de lavado. Esto se traduce en una disminución del desperdicio de material, un lavado más rápido y una mayor eficiencia. El lavado completo se puede programar en el módulo de pantalla avanzada de la unidad, con la posibilidad de preestablecer hasta cinco recetas de lavado diferentes con disolventes individuales, cronogramas y otros factores.
A MANTA también le interesaba la rentabilidad que ofrece el PD1K gracias a su control de caudal impecable, sus cambios de color rápidos y su dispensación eficiente. Su método de limpieza único reduce el consumo de disolvente y el desperdicio de material hasta en un 80 % y el coste del mantenimiento es considerablemente menor al de las bombas de engranajes, lo que lo convierte en una opción asequible para la línea de pintura de MANTA.
El dispositivo es perfecto para aplicaciones manuales o automáticas. Puede operar hasta cuatro bombas, dosificar diferentes productos químicos y controlar la vida útil de hasta tres pistolas de pulverización en un solo sistema. Se pueden gestionar hasta 30 colores en configuraciones 1K o 4K y es posible combinar materiales que suelen separarse, como epoxis y uretanos, o pintura de base agua o disolvente.
Funcionamiento de alta calidad
La línea empezó la producción total a finales de 2022. La fase de puesta en marcha implicó un proceso de aprendizaje, especialmente porque la pintura base agua es mucho más líquida que su equivalente de base disolvente. Al principio, era necesario retocarla manualmente porque los programas de pintura de los robots no estaban totalmente optimizados. Cuando se ajustaron, el trabajo manual necesario se redujo progresivamente.
MANTA y sus clientes están impresionados con la alta calidad de la pintura de los motores, gracias en parte a la calidad y el contenido tecnológico de los sistemas de Graco.
Perspectiva general de esta línea de pintura de motores
La nueva planta de pintura y la línea de pintura de motores totalmente automatizada son el resultado de la unión de expertos. Combinan la experiencia de Gaiotto, Savim, CM Automazione, Comaind y Graco.
La línea está compuesta por diferentes estaciones. Y nuestro sistema de alimentación y aplicación de pintura es una de ellas. Echemos un vistazo más de cerca a la perspectiva general, en la que cada número representa una estación independiente.
- La estación de enmascaramiento. Para proteger las superficies sensibles contra la entrada de agua durante el pretratamiento.
- Pretratamiento químico de 3 etapas con desengrase fosfatado y limpieza con agua desmineralizada.
- Túnel de presecado. El primer paso del proceso de secado.
- Soplado robótico. Para eliminar el agua de la limpieza que pueda haber quedado dentro de los orificios.
- Horno a 90 °C. El tercer y último paso del proceso de secado.
- Zona de enfriamiento.
- Segunda fase de enmascaramiento. Se usan unos 100 dispositivos de enmascaramiento.
El ciclo continúa con la aplicación de pintura líquida en dos cabinas de agua presurizadas con cortina y con control de temperatura y humedad. El espesor mínimo aplicado es de 50 micras.
Se utiliza una tercera cabina manual para retoques.
La línea de pintura del motor termina con un túnel de secado y un horno que seca 50 motores a 100 °C durante 1 hora y 30 minutos.
Para obtener más información sobre el sistema PD1K de Graco, rellene el siguiente formulario.
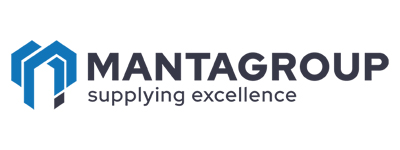
Artículos relacionados
La fábrica de Jonh Deere en Mannheim instala el sistema de suministro de pintura 2KS de Graco
Para cumplir con los estrictos estándares de calidad y aumentar la fiabilidad de su proceso, la fábrica de John Deere en Mannheim ha invertido en un nuevo sistema de suministro de pintura de Graco.
Los procesos manuales son cosa del pasado: automatización para aumentar la productividad
Descubra cómo las pistolas de pulverización AirPro de Graco funcionan bien con su proceso de automatización.
Recubrimiento óptimo de cajas de engranajes para máquinas autopropulsadas
Los dosificadores ProMix Easy y ProMix 2KS y las pistolas de pulverización G40 y AirPro de Graco demuestran lo que valen en una planta de producción de cajas de engranajes de Forli, Italia.