Lackierung von Motoren für landwirtschaftliche Fahrzeuge
Graco-Geräte spielen eine Schlüsselrolle in einer neuen automatischen Motorlackieranlage im Werk der MANTA-Gruppe in Italien.
Die MANTA-Gruppe mit Sitz in Foggia, Italien, konzentriert sich seit über 30 Jahren auf die Montage und Lackierung von Bauteilen für die Luft- und Raumfahrt und die Automobilindustrie. 2021 wurde das Unternehmen mit der Lackierung von Landmaschinenmotoren beauftragt. Zur Bewältigung dieser Aufgabe hat MANTA einen Pool von Zulieferern für den Aufbau einer vollständig digitalen, Industrie-4.0-konformen, automatisierten, flexiblen und schnellen Lackieranlage gefunden.
Die Ziele für die neue Lackieranlage waren anspruchsvoll. Sie müsste die Lackierung von mehr als 700 Motorvarianten in vier verschiedenen Farben ermöglichen – bei einer Kapazität von 85.000 Motoren pro Jahr. Außerdem musste das System vollständig digital in das Managementsystem des Unternehmens integriert werden, um die genaue Überwachung der einzelnen Lackierschritte und die Erfüllung der Qualitätsanforderungen sicherzustellen.
Gaiotto, Savim und CM Automazione waren für den Anlagenbau zuständig und Graco übernahm die Verantwortung für den Farbauftrag. Das Einschicht-Lackiersystem auf Wasserbasis, mit dem die Motoren lackiert werden, wurde vor Produktionsbeginn von einem externen Labor (CRF) validiert.
Reibungslose Zusammenarbeit
Die Lackieranlage wurde von Savim (Arbizzano, Verona, Italien) gebaut, mit Gaiotto-Robotern ausgestattet und mit einem von CM Automazione (Giussano, Monza und Brianza, Italien) entwickelten und gelieferten taktgesteuerten Förderband XD45/59 ergänzt. Die Anlage bietet Platz für bis zu 116 Handhabungsgeräte mit einer maximalen Tragfähigkeit von jeweils 850 kg. Bei vollem Durchsatz kann die Anlage 370 Motoren pro Tag lackieren.
Bei der Farbzufuhr, den Farbauftragsgeräten und dem Farbwechselsystem verließ sich MANTA auf Graco und seinen Integrator Comaind (San Giovanni Lupatoto, Verona, Italien), deren Zusammenarbeit in einer der kritischsten Phasen dieses Projekts von grundlegender Bedeutung war.
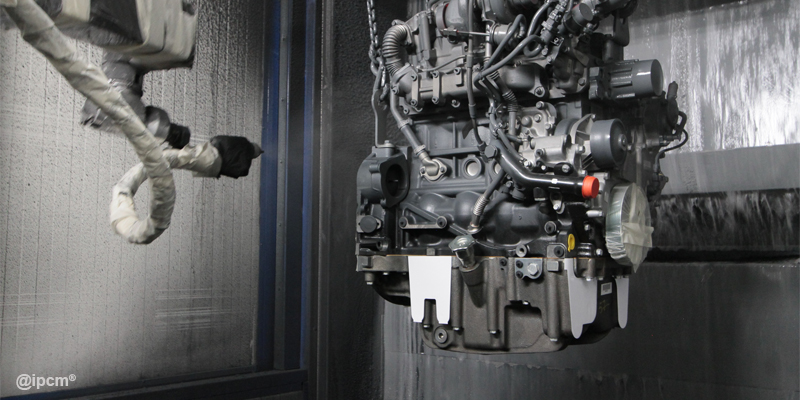
Ein optimierter Prozess
Jeder Motor durchläuft eine Reihe von Vorbereitungsstufen: Abkleben, chemische Vorbehandlung mit Phosphid-Entfettung, Reinigung mit demineralisiertem Wasser und Trocknung in drei Schritten (Vortrocknungstunnel, Abblasen durch Roboter, Ofen bei 90 °C), bevor die Motoren einen Kühlbereich durchlaufen.
Der flüssige Lack wird dann in zwei von Savim gelieferten, unter Druck stehenden, temperatur- und feuchtigkeitsgesteuerten Wasservorhang-Kabinen aufgetragen, die jeweils mit einem um 180° rotierenden Gaiotto-Gelenkroboter ausgestattet sind, der eine Motorseite lackiert. Die aufgetragene Mindestdicke beträgt 50 μm. Eine dritte manuelle Kabine wird für Ausbesserungen verwendet. Die Anlage endet mit einem Abblasetunnel und einem Ofen, der 50 Motoren bei 100 °C 90 Minuten lang aufnimmt. Die Motoren durchlaufen dann ein Inline Quality Gate für die endgültige Freigabe.
Das Farbauftragssystem
„Zur Handhabung der vier von MANTA aufgetragenen Farben haben wir das System für Farbzufuhr und Farbauftrag zusammen mit Gaiotto entwickelt“, erläutert Davide Galvani von Comaind. „Die am häufigsten verwendete Farbe ist Grau; sie macht fast 90 % der Produktion aus. Die anderen drei Farben sind Gelb, Perkins-Grau und Transparent, die die restlichen 10 % des Volumens ausmachen.“
Die Lackierungsplanung erfolgt nicht chargenweise, sondern für einzelne Motoren. Dies bedeutete, dass ein sehr schnelles Farbwechselsystem von nur 30 Sekunden entwickelt werden musste. Das Farbmanagementsystem ist mit einem 1000-kg-Behälter für die graue Farbe und 200-Liter-Fässern für die anderen Farben ausgestattet. Die Farbe wird durch ein ATEX-zertifiziertes elektrisches Rührwerk mit spreizbaren Schaufeln und einem Nachfüllsystem, das mit einem 100-Liter-Behälter verbunden ist, in dem eine Graco Endura-Flo-Pumpe die Farbe mit einem Druck von 2,5–3 bar umwälzt, ständig in Bewegung gehalten. Dieser Behälter speist das Mehrkomponenten-Dosiergerät PD1K von Graco, das mit vier separaten Pumpen – eine für jede Farbe – ausgestattet ist, um eine maximale Farbwechselgeschwindigkeit im Roboter zu gewährleisten.
Darüber hinaus wird das Produkt im Kreislauf einer Filterung mit Maschenweite 60 unterzogen. Das PD1K-Gerät verfügt außerdem über eine eigene Filtereinheit am Pistolenausgang. Die beiden Lackierroboter sind mit je zwei automatischen normenkonformen Graco AirPro-Pistolen ausgestattet. Eine Pistole ist für die graue Farbe zuständig, während die andere über Farbwechselventile gespeist wird, die etwa 40–50 cm von der Pistole entfernt, also fast am Handgelenk des Roboters, angebracht sind. Ein Ventil dient zum Spülen des Kreislaufs, die anderen drei sind für die Farben. Das Farbmanagementsystem speist auch vorab die Ausbesserungskabine, in der für jede Farbe eine Pistole zur Verfügung steht, die je nach dem ankommenden Motor mit der richtigen Farbe aktiviert wird.
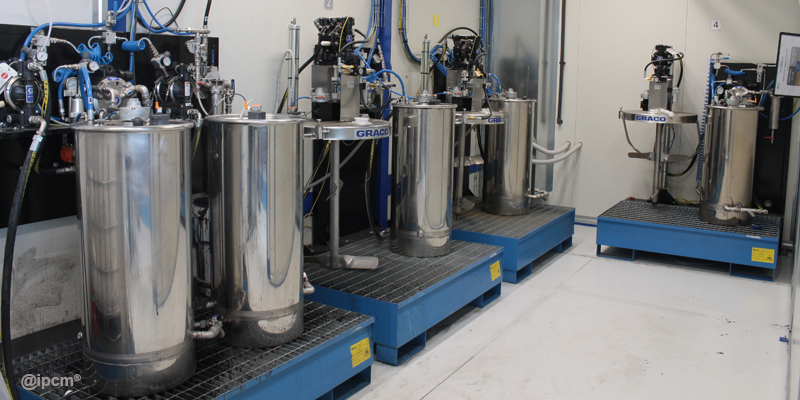
Das PD1K von Graco als Herzstück des Systems
„Wir haben uns für das Mehrkomponenten-Dosiergerät PD1K von Graco entschieden, da es die direkte Steuerung des Farbflusses an der Pistole und die Anpassung an die Bewegungen des Roboters während des Lackiervorgangs ermöglicht“, fügt Galvani hinzu. „Dieses Gerät ermöglicht auch die Analyse der technischen und produktiven Parameter und ist mit dem System 4.0 der Anlage verbunden.“
Dank der einzigartigen, auf einem Impulsgeber basierenden Kolbenantriebstechnologie und den aktiven Steuerventilen bietet das PD1K eine Mischverhältnisgenauigkeit innerhalb von 1 % und gewährleistet so jedes Mal eine reibungslose und genaue Dosierung. Diese außerordentliche Genauigkeit wird unabhängig von statischem Druck, Höhe, Materialviskosität, Temperatur oder Pistolenabzug eingehalten.
Außerdem wird durch die Verlagerung des Mischpunkts näher an die Pistole der Spülbereich verkleinert. Dies führt zu weniger Materialverlust, schnellerem Spülen und höherer Effizienz. Die vollständige Spülung kann im erweiterten Anzeigemodul programmiert werden, mit der Möglichkeit, bis zu fünf verschiedene Spülrezepte mit individuellen Lösungsmitteln, Zeitplänen und anderen Faktoren vorab einzustellen.
Interessant für MANTA ist auch die Kosteneffizienz des PD1K, die sich durch die einwandfreie Durchflussregelung, schnelle Farbwechsel und eine effiziente Dosierung auszeichnet. Seine einzigartige Spülmethode reduziert den Lösungsmittelverbrauch und den Materialabfall um bis zu 80 %, die Wartungskosten sind im Vergleich zu Zahnradpumpen deutlich geringer, und dies macht es zu einer budgetfreundlichen Möglichkeit für die MANTA-Lackieranlage.
Das Gerät eignet sich hervorragend für manuelle oder automatische Anwendungen. Es kann bis zu vier Pumpen betreiben, verschiedene Chemikalien dosieren und die Topfzeit von bis zu drei Spritzpistolen verfolgen – alles mit einem System. Bis zu 30 Farben können in 1K- bis 4K-Setups verwaltet und typischerweise getrennte Materialien wie Epoxid- und Urethanlacke oder Farben auf Wasser- und Lösungsmittelbasis können kombiniert werden.
Mit hoher Qualität in Betrieb
Die Anlage ging Ende 2022 in vollem Umfang in Betrieb. Die Anlaufphase war mit einem Lernprozess verbunden, zumal Farbe auf Wasserbasis sehr viel flüssiger ist als ihre Pendants auf Lösungsmittelbasis. Anfänglich waren einige manuelle Nacharbeiten erforderlich, da die Lackierprogramme der Roboter nicht ganz optimiert waren. Als diese angepasst wurden, konnte der manuelle Arbeitsaufwand schrittweise reduziert werden.
MANTA – und seine Kunden – sind von der hohen Qualität der Motorlackierung beeindruckt und das ist teilweise auf die Qualität und den technologischen Gehalt der Graco-Systeme zurückzuführen.
Das Gesamtbild dieser Motorenlackieranlage
Die neue Lackieranlage und die vollautomatische Motorenlackierstraße sind das Ergebnis der Zusammenarbeit von Experten. Sie vereinen das Know-how von Gaiotto, Savim, CM Automazione, Comaind und Graco.
Die Anlage besteht aus verschiedenen Stationen. Unser Farbzufuhr- und Farbauftragssystem ist eine davon. Schauen wir uns das Gesamtbild genauer an; dabei steht jede Zahl für eine einzelne Station.
- Die Abklebestation. Zum Schutz empfindlicher Oberflächen vor eindringendem Wasser während der Vorbehandlung
- 3-stufige chemische Vorbehandlung mit Phosphidfettung, Reinigung mit demineralisiertem Wasser.
- Vortrocknungstunnel. Der erste Schritt des Trocknungsprozesses.
- Abblasen durch Roboter Zur Entfernung des in den Löchern verbliebenen Reinigungswassers.
- Ofen bei 90 °C. Der dritte und letzte Schritt des Trocknungsprozesses.
- Kühlbereich.
- Abklebephase 2. Es werden etwa 100 Abklebegeräte eingesetzt.
Der Zyklus wird fortgesetzt mit dem Auftragen des Flüssiglacks in zwei unter Druck stehenden, temperatur- und feuchtigkeitsgeregelten Wasservorhang-Kabinen. Die aufgetragene Mindestdicke beträgt 50 μm.
Eine dritte manuelle Kabine wird für Ausbesserungen verwendet.
Die Lackierstraße für Motoren endet mit einem Abblasetunnel und einem Ofen, der 50 Motoren bei 100 °C 1,5 Stunden lang aufnimmt.
Für weitere Informationen über PD1K-Systeme von Graco füllen Sie bitte das Formular unten aus.
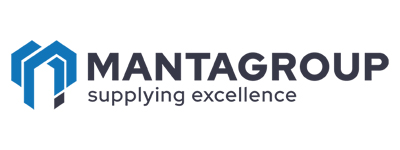
Ähnliche Artikel
John Deere Werk in Mannheim installiert Farb-Zufuhrsystem Graco 2KS
Zur Erfüllung höchster Qualitätsanforderungen und zur Steigerung der Prozess-Sicherheit hat das Mannheimer John Deere Werk in ein neues Farb-Zufuhrsystem von Graco investiert.
Manuelle Prozesse gehören der Vergangenheit an: Automatisierung für mehr Produktivität
Erfahren Sie, wie die Graco AirPro-Spritzpistolen gut mit Ihrem Automatisierungsprozess zusammenarbeiten.
Optimale Beschichtung von Getrieben für Maschinen mit Eigenantrieb
Die Dosiergeräte ProMix Easy, ProMix 2KS sowie die Spritzpistolen G40 und AirPro von Graco demonstrieren ihre Stärken aktuell im Getriebewerk von Bonfiglioni in Forli (Italien).