InvisiPac
Začněte využívat hlavní výhody technologie systémů bez nádrží InvisiPac pro dodávku horké taveniny. Díky principu tavení na vyžádání eliminují systémy dodávky horké taveniny InvisiPac připalování lepidla a zvyšují produktivitu.
Bezpečné. Spolehlivý. Ziskové.
- Eliminujte nákladná bezpečnostní rizika tím, že odstraníte riziko přímého kontaktu obsluhy vaší linky s horkým roztaveným lepidlem
- Snižte spotřebu lepidla minimálně o 20 % a potenciálně až o 70–80 %
- Eliminujte neplánované prostoje způsobené zuhelnatěním lepidla, ucpáváním trysek a problémy s hadicí
- Zvyšte výrobu s bezkonkurenční 10minutovou dobou uvedení do provozu systému InvisiPac, která vám každý den poskytne dalších 25 minut výroby
- Sledujte svoji spotřebu, výkon a další systémová data kdekoli a kdykoli.
Rozdíl díky InvisiPac
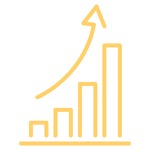
Ziskové.
Díky špičkovému času spouštění pouhých 10 minut dosahuje bezzásobníková technologie InvisiPac snížení spotřeby energie pro spouštění. Kromě toho systém InvisiPac snižuje využití lepidla a eliminuje neplánované prostoje způsobené připálením, ucpáváním trysek a problémy s hadicemi. To vše přispívá k zaručeným úsporám.
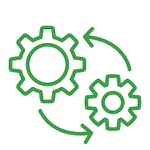
Spolehlivé
Systém pro dodávku horké taveniny InvisiPac udržuje lepidlo na konzistentní teplotě a viskozitě. Tím, že se zabrání kolísání teploty a tvorbě připálenin, zůstává výstup materiálu konstantní během výrobní směny s nulovými prostoji. Integrovaný modul filtru na aplikátoru InvisiPac eliminuje ucpané trysky a zaručuje dodávku konzistentní housenky lepidla na každé krabici. Sledujte využití lepidla, výkon systému a data linky odkudkoliv a kdykoliv a dosáhněte svých cílů v průmyslu 4.0.
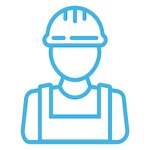
Bezpečné.
Protože obsluha nemá přímý kontakt s taveninou, systém InvisiPac eliminuje bezpečnostní rizika, jako je hoření, toxické výpary a prokluz. Když tavicí zařízení dosáhne určité hladiny, automaticky se do plnicího systému odešle signál, který způsobí, že lepidlo bude nasáváno z nádoby přímo do tavicího zařízení – to vše bez zásahu obsluhy.
Lepší v každém ohledu
Bližší pohled na systém pro horkou taveninu InvisiPac
InvisiPac HM25c
Maximální rychlost tavení 11,3 kg/25 lbs za hodinu
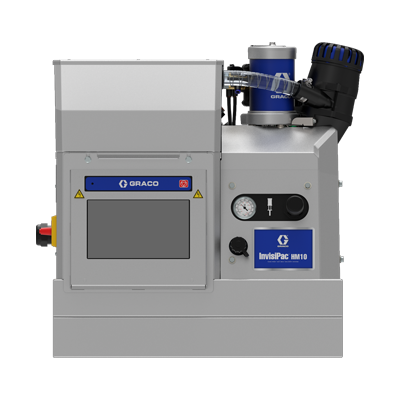
InvisiPac HM10
Maximální rychlost tavení 4,5 kg/10 lb za hodinu