Case Study: Li-ion Battery Manufacturing
Studium przypadku: Produkcja akumulatorów litowo-jonowych
An EV battery manufacturer had to determine the best foam encapsulation process for a new cell module design. Quick collaboration with Graco put it into production by a critical deadline.
Producent akumulatorów litowo-jonowych optymalizujący proces zamykania pianki
Producent akumulatorów litowo-jonowych potrzebował rozwiązania pozwalającego na zalewanie ogniw, które spełniałoby wymagania branżowe z zakresu zapobiegania niekontrolowanym zmianom i propagacji temperatury w przypadku stosowanych przez niego modułów z cylindrycznymi ogniwami akumulatorowymi. Producent borykał się z problemem określenia odpowiednich punktów wtrysku, parametrów dozowania, a także wpływu skomplikowanej dynamiki płynów. Poza wyzwaniami projektowymi, producent musiał także zmierzyć się z kluczową kwestią związaną z datą wprowadzenia produktu na rynek, dlatego też potrzebował gotowego procesu produkcyjnego, umożliwiającego zaplanowanie swojej linii produkcyjnej.
Wyzwania związane z procesem
Konstrukcja każdego ogniwa cylindrycznego ma unikalne cechy, a także wymagania mogące wpływać na natężenia przepływu oraz punkty dozowania wtryskowego, pozwalające na równomierne dozowanie odpowiednich ilości materiału w obrębie modułów. W przypadku tego projektu konieczne było stawienie czoła następującym wyzwaniom:
- Brak możliwości zmiany konstrukcji akumulatora na tak późnym etapie produkcyjnym
- Konieczność dozowania od górnej części modułu akumulatorowego, z ewentualną możliwością wtryskiwania bocznego.
- Ogniwa akumulatora znajdowały się bardzo blisko siebie, co oznaczało bardzo niewielkie odległości pomiędzy nimi, a to z kolei wpływało na dodatkowe ograniczenie przepływu.
- Dostęp pianki do modułu akumulatora od góry był mocno ograniczony.
- Czas trwania procesu miał kluczowe znaczenie dla działań klienta.
Proces współpracy
Nasz zespół inżynierów ds. zastosowań podjął bezpośrednią współpracę z zespołem projektowym producenta akumulatorów oraz dostawcą materiałów w celu opracowania rozwiązania procesowego spełniającego wymagania w zakresie wydajności operacyjnej, jakości produktu i powtarzalności zastosowania materiałów. Dzięki naszemu laboratorium rozwojowemu, zespołowi ekspertów ds. aplikacji oraz współpracy z dostawcą materiałów przeprowadziliśmy odpowiednie próby mające na celu określenie optymalnej metody aplikacji, definiującej natężenie przepływu, techniki aplikacji oraz punkty dozowania dla końcowego procesu produkcyjnego.
Testowanie materiałów – mając na uwadze możliwość określenia optymalnego rodzaju pianki oraz wymogów dotyczących sprzętu, przeprowadzono szczegółowe badania nad proporcjami i powtarzalnością procesu.
Specyfikacja sprzętu – na podstawie wcześniejszych prób przeprowadzonych dla podobnych zastosowań oraz opartych na dokonanej przez nas ocenie materiału określiliśmy idealną kombinację sprzętu w kontekście aplikacji docelowej.
Próby aplikacji – korzystając z prototypowych modeli i modułów dostarczonych przez producenta akumulatorów, dokonaliśmy oceny i walidacji proponowanej specyfikacji procesu.
WYNIKI
- Wypełnianie z wykorzystaniem & wysokiej jakości pianki: Zawór mieszający Voltex przeznaczony do mieszania dynamicznego oraz system dozowania EFR Meter Mix Dispense System zapewniły możliwość dokładnego mieszania panki, jej równomiernego rozprowadzania w obrębie całego modułu oraz powtarzalność wtryskiwania, której wymagał proces produkcyjny klienta.
- Zoptymalizowane dozowanie: na podstawie przeprowadzonych prób laboratoryjnych określiliśmy odpowiednie parametry mieszania, natężenia przepływu, a także punkty dozowania wtryskowego, pozwalające na precyzyjne i równomierne dozowanie odpowiednich ilości materiału w obrębie modułu.
- Krótszy czas trwania procesu: dzięki modelowaniu oraz próbom dozowania zoptymalizowaliśmy wzór ruchu, co pozwoliło nam uzyskać jeszcze krótszy czas trwania procesu.
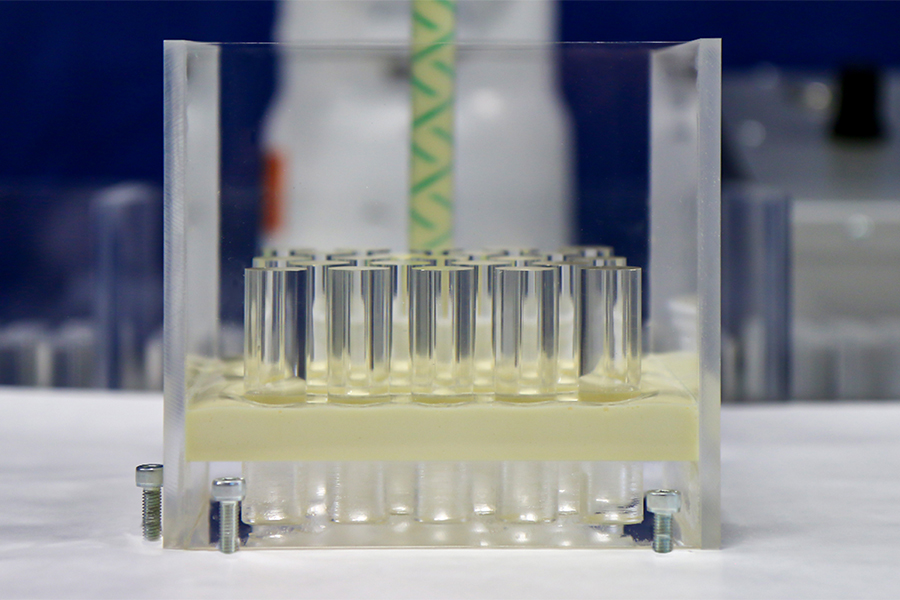
- Quality foam and fill: The Voltex Dynamic Mix Valve and Electric Fixed Ratio (EFR) Metering System provide thoroughly mixed form, even distribution throughout the module, and shot repeatability.
- Optimized dispense: With the proper mixing parameters, flow rates, and dispense injection points, an accurate amount of material is evenly dispensed into each module.
- Rapid process time: The modeling and dispense trials helped optimized the motion pattern to reduce the required processing time.
Collaborate with Us
Innovation truly comes through collaboration with Graco expertise and material supplier partnerships. We strive to deliver custom solutions backed by our global support network.
Contact our team for help with your application.
Related Articles
Enkapsulacja pianką cylindrycznych ogniw akumulatorów
Dowiedz się więcej na temat enkapsulacji pianką i jej roli w produkcji wysokowydajnych modułów akumulatorowych, które pozostają bezpieczne w każdej sytuacji awaryjnej.
Zarządzanie termiczne w produkcji baterii do pojazdów elektrycznych i elektroniki
Niezależnie od tego, czy mówimy o bateriach stosowanych w pojazdach elektrycznych (EV), produktach elektronicznych, czy o miniaturyzacji płytek drukowanych (PCB), zarządzanie ciepłem odgrywa kluczową rolę w kontekście trwałości, wydajności i bezpieczeństwa.
Uszczelnianie akumulatorów – akumulatory do pojazdów elektrycznych
Wysokiej jakości uszczelnienie odgrywa kluczową rolę w kwestii zapewniania wydajności i długowieczności akumulatorów przeznaczonych do pojazdów elektrycznych. Ponadto chroni ono komponenty wewnętrzne przed wnikaniem wody, a także przed innymi, niesprzyjającymi warunkami środowiskowymi.