Verniciatura di motori per veicoli agricoli
Le apparecchiature Graco svolgono un ruolo chiave in una nuova linea automatica di rivestimento motori presso lo stabilimento del Gruppo MANTA in Italia.
Il Gruppo MANTA, con sede a Foggia, in Italia, si concentra da oltre 30 anni sull'assemblaggio e sul rivestimento di componenti aerospaziali e automobilistici. Nel 2021, all'azienda è stata affidata la verniciatura dei motori per macchine agricole. Per portare a termine questo compito, MANTA ha identificato un pool di fornitori per costruire una linea di verniciatura completamente digitale, conforme a Industry 4.0, automatizzata, flessibile e veloce.
Gli obiettivi per la nuova linea di rivestimento erano impegnativi. Avrebbe dovuto consentire la verniciatura di oltre 700 varianti di motore in quattro colori diversi, con una capacità di 85.000 motori all'anno. Inoltre, doveva essere completamente integrata digitalmente con il sistema di gestione dell'azienda per consentire un attento monitoraggio di ogni fase del rivestimento e il rispetto dei requisiti di qualità.
Per gli aspetti impiantistici sono stati coinvolti Gaiotto, Savim e CM Automazione, mentre a Graco è stata affidata la responsabilità dell'applicazione della verniciatura. Il sistema di verniciatura monostrato a base acquosa da applicare sui motori è stato validato da un laboratorio esterno (CRF) prima dell'avvio della produzione.
Collaboratori tranquilli
L'impianto di verniciatura è stato realizzato da Savim (Arbizzano, Verona, Italia), dotato di robot Gaiotto, e integra un trasportatore passo-passo XD45/59 progettato e fornito da CM Automazione (Giussano, Monza e Brianza, Italia). La linea ospita fino a 116 unità di movimentazione con una capacità di carico massima di 850 kg ciascuna. A pieno regime, la linea è in grado di verniciare 370 motori al giorno.
Per la fornitura di alimentazione vernice, le attrezzature per l'applicazione della vernice e il sistema di cambio colore, MANTA si è affidata a Graco e al suo integratore Comaind (San Giovanni Lupatoto, Verona, Italia), la cui collaborazione è stata fondamentale in una delle fasi più critiche di questo progetto.
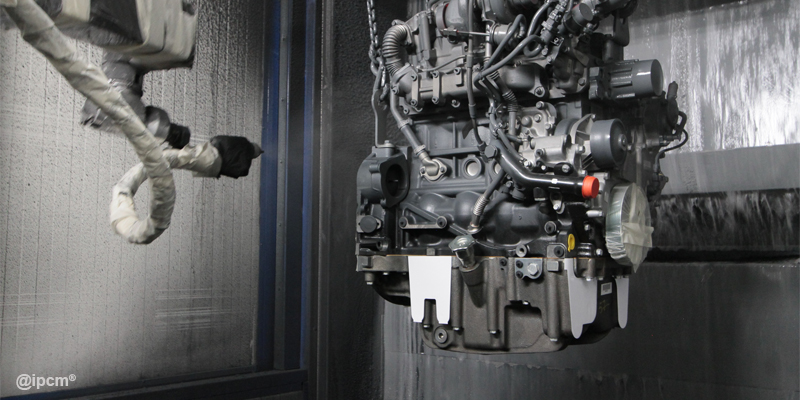
Un processo ottimizzato
Ogni motore passa attraverso una serie di fasi di preparazione: mascheratura, pretrattamento chimico con fosfosgrassaggio, pulizia con acqua demineralizzata ed asciugatura in tre fasi (tunnel di pre-asciugatura, soffiaggio robotizzato, forno a 90°C) prima i motori che i passino attraverso una zona di raffreddamento.
La vernice liquida viene quindi applicata in due cabine a velo d'acqua pressurizzate, a temperatura e umidità controllate, fornite da Savim, ciascuna dotata di un robot articolato Gaiotto con rotazione di 180° che vernicia un lato del motore. Lo spessore minimo applicato è di 50 micron. Una terza cabina manuale viene utilizzata per i ritocchi. La linea termina con un tunnel di appassimento e un forno che ospita 50 motori a 100°C per 90 minuti. I motori procedono quindi verso una porta di controllo qualità in linea per l'approvazione finale.
Il sistema di applicazione della vernice
“Abbiamo progettato insieme a Gaiotto il sistema di alimentazione e applicazione della vernice per gestire i quattro colori applicati da MANTA”, spiega Davide Galvani di Comaind. “Quello più utilizzato è il grigio, che rappresenta quasi il 90% della produzione. Gli altri tre colori sono giallo, grigio Perkins e trasparente, che coprono il restante 10% dei volumi”.
La pianificazione del rivestimento non viene eseguita su base batch ma per singoli motori. Ciò si è tradotto nella progettazione di un sistema di cambio colore rapidissimo che richiede appena 30 secondi. L'unità di gestione vernice è dotata di un contenitore da 1000 kg per il colore grigio e di fusti da 200 litri per le altre tinte. La vernice è mantenuta in agitazione da un agitatore elettrico certificato ATEX con palette espandibili e un sistema di ricarica collegato ad un serbatoio da 100 litri dove una pompa Graco Endura-Flo fa circolare la vernice ad una pressione di 2,5-3 bar. Questo serbatoio prealimenta il dosatore pluricomponente Graco PD1K dotato di quattro pompe separate, una per ogni colore, per garantire la massima velocità di cambio colore a bordo del robot.
Inoltre sul prodotto ricircolato viene effettuata una filtrazione a 60 mesh. Il dispositivo PD1K dispone inoltre di una propria unità di filtraggio all'uscita della pistola. I due robot di rivestimento sono dotati ciascuno di due pistole automatiche conformi alla tecnologia Graco AirPro. Una pistola lavora con vernice grigia, mentre l'altra è alimentata da valvole di cambio colore posizionate a circa 40-50 cm dalla pistola, quasi sul polso del robot; una valvola serve per il lavaggio del circuito e le altre tre servono per le tinte. L'unità di gestione della vernice prealimenta anche la cabina di ritocco dove per ogni colore è disponibile una pistola che si attiva con il colore corretto a seconda del motore in entrata.
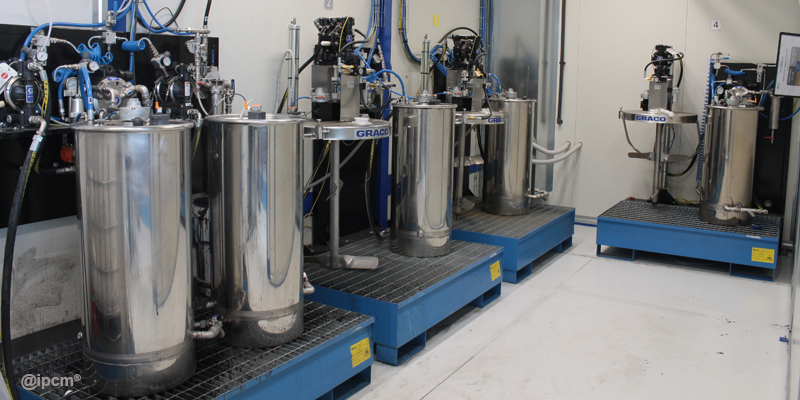
Il PD1K di Graco al cuore del sistema
"Abbiamo scelto il dosatore pluricomponente Graco PD1K perché consente di controllare direttamente il flusso di vernice sulla pistola e di regolarlo in base al movimento del robot durante la fase di verniciatura", aggiunge Galvani. “Questa unità permette anche di eseguire l’analisi dei parametri tecnico/produttivi e si interfaccia con il sistema 4.0 della linea.”
Grazie alla sua esclusiva tecnologia di azionamento del pistone basata su encoder e alle valvole di controllo attive, il PD1K fornisce una precisione del rapporto di miscelazione entro l'1%, garantendo ogni volta un'erogazione regolare e precisa. Il sistema mantiene questa accuratezza straordinaria indipendentemente da pressione ed elevazione della testa, viscosità del materiale, temperatura e frequenza di attivazione della pistola.
Inoltre, avvicinando il punto di miscelazione alla pistola, si diminuisce la zona di lavaggio. Ciò si traduce in meno sprechi di materiale, lavaggi più rapidi e maggiore efficienza. Il lavaggio completo può essere programmato nel modulo ADM dell’unità, con la possibilità di preimpostare fino a cinque diverse ricette di lavaggio con singoli solventi, orari programmati e altri fattori.
Un altro elemento interessante per MANTA è il rapporto costo-efficacia del dosatore PD1K, grazie al controllo impeccabile del flusso, ai rapidi cambi di colore e all'efficiente erogazione. Il suo esclusivo metodo di lavaggio riduce l'uso di solventi e gli sprechi di materiale fino all'80%, inoltre il costo di manutenzione è notevolmente inferiore rispetto a quello delle pompe a ingranaggi.
L’apparecchio è perfettamente adatto per applicazioni manuali o automatiche. Permette di azionare fino a quattro pompe, erogare diverse sostanze chimiche e tracciare la durata utile della carica per un massimo di tre pistole a spruzzo - tutto in un unico sistema. Può gestire fino a 30 colori in configurazioni da 1K a 4K e combinare materiali tipicamente separati come resina epossidica e uretano o vernici a base acquosa o di solvente.
Pienamente funzionante ad alta qualità
La linea è entrata in piena modalità di produzione alla fine del 2022. La fase di avvio ha comportato un processo di apprendimento, soprattutto perché la vernice a base acquosa è molto più liquida della sua equivalente a base solvente. Inizialmente sono stati necessari alcuni ritocchi manuali poiché i programmi di verniciatura dei robot non erano completamente ottimizzati. Quando questi sono stati adeguati, il lavoro manuale necessario si è progressivamente ridotto.
MANTA – e i suoi clienti – sono impressionati dall'alta qualità della verniciatura dei motori, dovuta in parte alla qualità e al contenuto tecnologico dei sistemi Graco.
Il quadro più ampio di questa linea di verniciatura motori
Il nuovo impianto di verniciatura e la linea di verniciatura dei motori completamente automatizzata sono il risultato dell'unione degli sforzi di esperti. Questi combinano le competenze di Gaiotto, Savim, CM Automazione, Comaind e Graco.
La linea è composta da diverse stazioni. Il nostro sistema di alimentazione e applicazione della vernice è uno di questi. Diamo uno sguardo più da vicino al quadro più ampio, dove ogni numero rappresenta una stazione separata.
- La stazione di mascheramento. Per proteggere le superfici sensibili dall'ingresso di acqua durante il pretrattamento
- Pretrattamento chimico a 3 stadi con ingrassaggio ai fosfuri e pulizia con acqua demineralizzata.
- Tunnel di pre-essiccazione. La prima fase del processo di essiccazione.
- Soffiaggio robotico. Per rimuovere l'acqua di pulizia rimasta all'interno dei fori.
- Forno a 90°C. La terza e ultima fase del processo di essiccazione.
- Zona di raffreddamento.
- Fase 2 di mascheramento. Vengono applicati circa 100 dispositivi di mascheramento.
Il ciclo prosegue con l'applicazione della vernice liquida in due cabine a velo d'acqua pressurizzate, a temperatura e umidità controllate. Lo spessore minimo applicato è di 50 micron.
Una terza cabina manuale viene utilizzata per i ritocchi.
La linea di verniciatura motori termina con un tunnel di appassimento e un forno che accoglie 50 motori a 100°C per 1 ora e 30 minuti
Per ulteriori informazioni sul sistema PD1K di Graco, compilare il modulo riportato sotto, compilare il modulo riportato sotto.
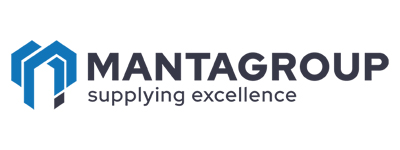
Articoli correlati
Lo stabilimento John Deere di Mannheim installa il sistema di alimentazione di vernice 2KS di Graco
Per soddisfare gli stringenti standard di qualità e aumentare l'affidabilità dei processi, lo stabilimento John Deere di Mannheim ha investito in un nuovo sistema di alimentazione di vernice Graco.
I processi manuali appartengono al passato: automazione per una maggiore produttività
Scoprite come le pistole a spruzzo Graco AirPro funzionano bene con il vostro processo di automazione.
Rivestimento ottimale delle trasmissioni per macchine semoventi
I dosatori ProMix Easy, ProMix 2KS e le pistole a spruzzo G40 e AirPro di Graco danno prova del loro valore nell'impianto di produzione di trasmissioni Bonfiglioli a Forlì, in Italia.