Controllo della qualità dell’imballaggio per aumentare l’affidabilità e la redditività
Ottimizzazione del processo produttivo
Per molte applicazioni di produzione industriale, l’ideazione di un processo di produzione efficiente ed efficace rappresenta spesso l’elemento chiave per una buona redditività. Gli ingegneri di processo investono molto tempo e abbondanti risorse per testare e riuscire a mettere a punto processi ottimizzati.
La standardizzazione in vista della conformità ISO e il mantenimento di un processo di produzione snello è una costante nel settore dell’industria automobilistica, in cui quando si definisce un processo alterarlo o cambiarlo in fase di produzione potrebbe equivalere al suicidio.
Imballaggio di fine linea con processi di produzione ISO e snelli
Il desiderio di ottenere la certificazione ISO 9000 o 9001 in ultima analisi ha spinto molti settori a dotarsi di processi di produzione e attenervisi. Queste certificazioni non si concentrano su ciò che il processo dovrebbe essere esattamente; sono semplici strumenti che documentano il processo e poi usano quella documentazione allo scopo di monitorare che i produttori mantengano costante la qualità del prodotto.
Quando gli impianti mettono in atto metodi di produzione snella il punto di attenzione è l’eliminazione degli sprechi per aumentare l’efficienza e ridurre il prezzo, fornendo così un valore aggiunto alla clientela.
A causa delle troppe variabili che sfuggono al loro controllo, i responsabili della qualità hanno dedicato poca attenzione allo sviluppo di processi d’imballaggio di fine linea snelli o ottimizzati.
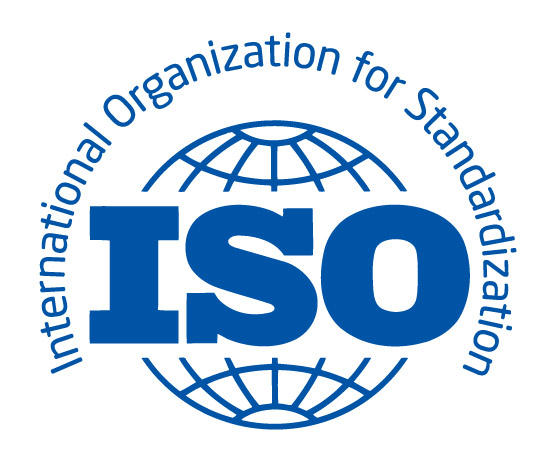
Tecnologie antiquate e produzione snella
Le iniziative di produzione snella tendono a non comprendere le applicazioni di imballaggio di fine linea soprattutto perché non c’è modo di ottimizzare il processo a causa delle limitate capacità del sistema. L’antiquata tecnologia della fusione con serbatoio e delle pompe a ingranaggi rende pressoché impossibile la standardizzazione del processo.
Dato che i vecchi sistemi a caldo fondono l’adesivo in un serbatoio riscaldato, è molto difficile mantenere una temperatura costante dell’adesivo. La colla che è vicina all’esterno del serbatoio si scalda più in fretta e inizia a deteriorarsi mentre quella che sta al centro del serbatoio sta ancora andando in temperatura.
L’utilizzo di sistemi a caldo con serbatoio genera una costante lotta per la regolazione.
È opinione diffusa che gli operatori della linea debbano continuamente regolare le impostazioni del sistema per ottenere i risultati desiderati. Questi continui interventi alla fine riducono la capacità di controllo totale sul processo. Riuscire a “impostare e dimenticare” il sistema per l’applicazione di adesivi a caldo è impossibile, poiché le impostazioni dell’operatore del primo turno spesso sono diverse da quelle dell’operatore del terzo turno.
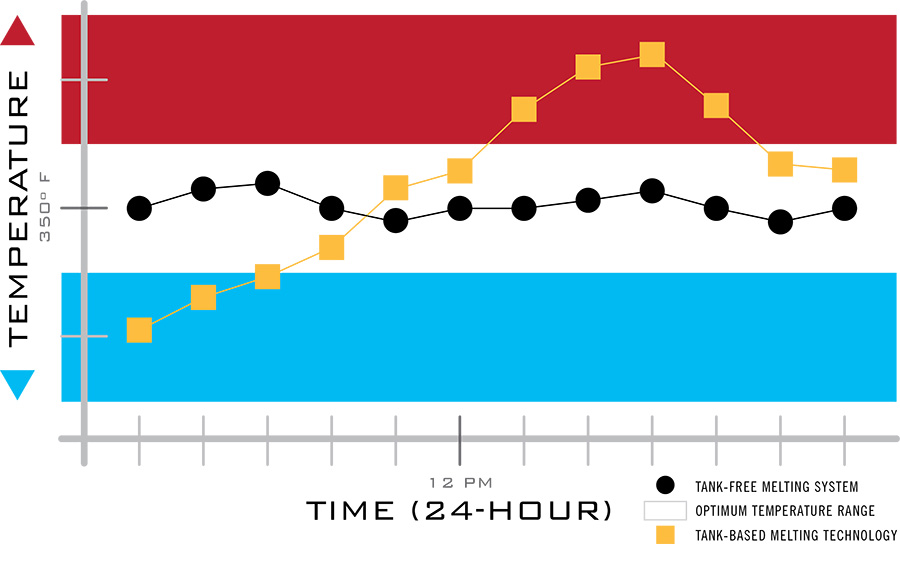
Alcuni sistemi a caldo più evoluti usano ancora delle variazioni di questo vecchio approccio per sciogliere l’adesivo. Ad esempio, alcuni sistemi usano serbatoi più piccoli che contengono delle “alette” in prossimità del fondo del “serbatoio” per cercare di aumentare la superficie dell’area di fusione. Tuttavia, si tratta di una variazione del serbatoio riscaldato che non mantiene costante la temperatura dell’adesivo all’interno del sistema, soprattutto se l’adesivo rimane all’interno per un tempo prolungato.
Quando si valutano i sistemi a caldo, è bene porre ai fornitori dell’apparecchiatura queste sei importanti domande e chiedere che venga fatta una dimostrazione dettagliata di come avviene la fusione dell’adesivo.
Adesivi alternativi per avere caratteristiche di materiale più costanti
Oltre che la tecnologia dei sistemi a caldo, conoscere a fondo i materiali adesivi può essere di supporto per i tecnici per aiutarli a sviluppare un processo ottimizzato per l’imballaggio a fine linea. Gli adesivi a caldo hanno quattro componenti.
1) Composti di base: sono la spina dorsale o il nucleo delle caratteristiche che deve avere l’adesivo, come la resistenza meccanica,la flessibilità e le proprietà finali di resistenza al calore, al freddo e alle aggressioni chimiche. Nella maggior parte dei casi, gli adesivi di base non vengono usati da soli.
2) Miglioratori di viscosità: danno al materiale l’adesività a caldo o la collosità relativa. Il miglioratore di viscosità utilizzato dipende dalle specifiche proprietà di adesione richieste per un particolare supporto e in genere determina il colore e l’odore caratteristici di un particolare adesivo a caldo.
3) Diluenti: cere o oli che modificano la viscosità e il tempo di fissaggio dell’adesivo, chiamato anche ‘set time’.
4) Stabilizzatori: aggiunti in anni recenti per dare stabilità alla viscosità e contribuire a evitare la carbonizzazione dell’adesivo che rimane a lungo nei serbatoi riscaldati.
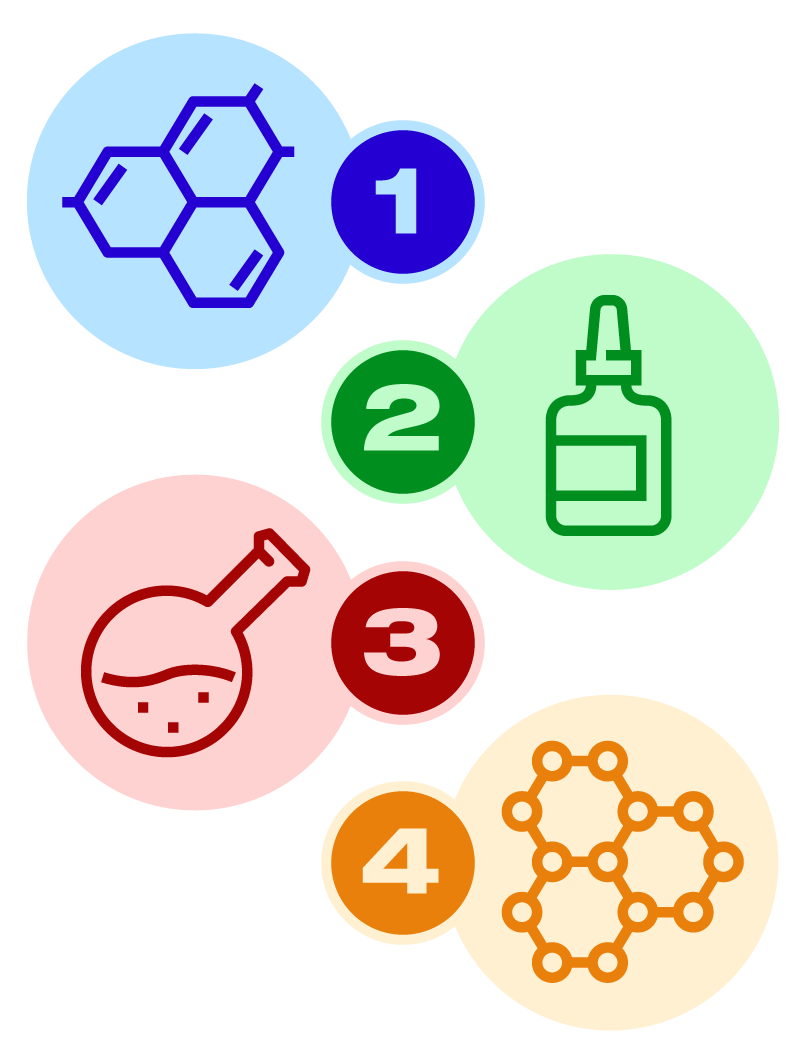
Controllo qualità e prestazioni
Avere un processo standardizzato significa che tutti questi componenti vengono controllati da vicino nelle fasi di fusione, trasferimento ed erogazione. L’obiettivo finale è far combaciare le proprietà dell’adesivo a caldo con i requisiti in termini di prestazioni dello stesso.
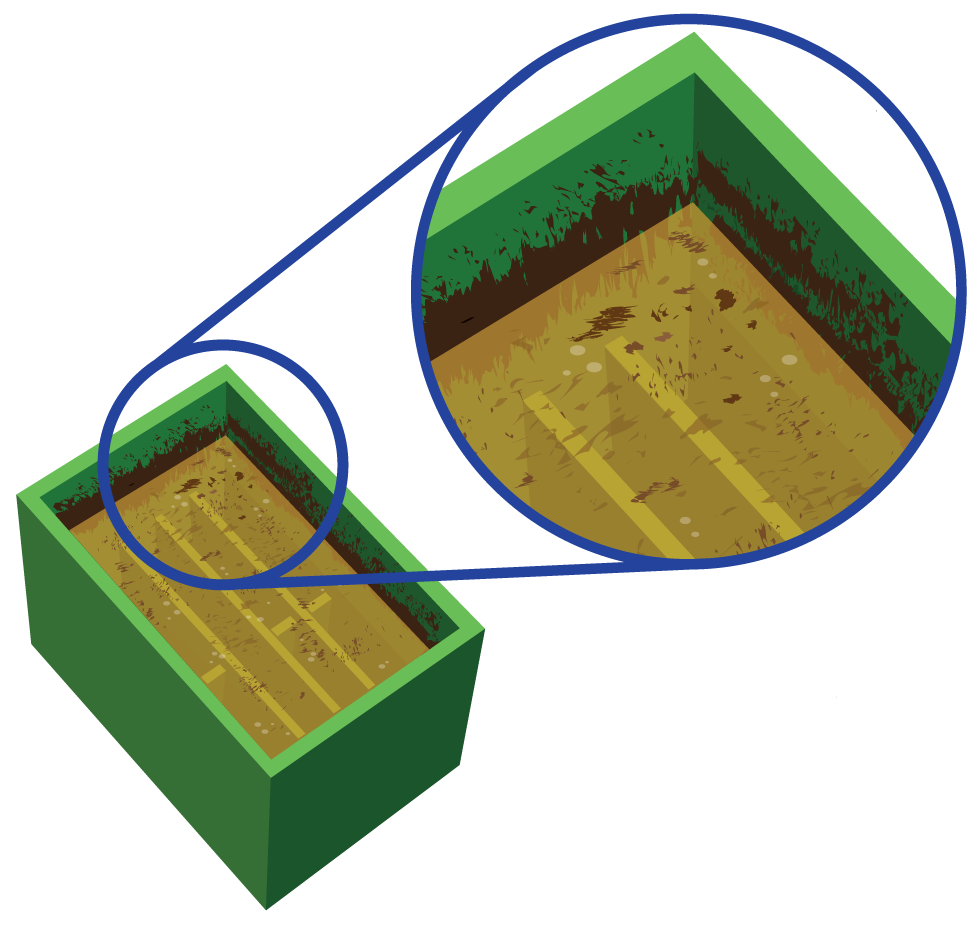
Degradazione e carbonizzazione della colla
Con la classica tecnologia a caldo con serbatoio, la consistenza della colla varia costantemente. Questa condizione è stata accettata come inevitabile nelle applicazioni per gli imballaggi di fine linea, insieme alla degradazione della colla e alle problematiche di carbonizzazione dell’adesivo all’interno del sistema a caldo.
Per risolvere i problemi di carbonizzazione e consistenza dell’adesivo, i produttori si sono rivolti ai fornitori di materiali chiedendo che venissero sviluppate delle alternative agli adesivi a caldo, come i metalloceni. Gli adesivi metallocenici alternativi tendono a raggrumarsi di meno, ad avere una maggiore stabilità della temperatura e a funzionare con una gamma più ampia di temperature. Ciononostante, questi adesivi alternativi sono più costosi e quindi riducono la redditività dei processi produttivi.
Qualità grazie al miglioramento delle tecnologie
I sistemi di adesivi a caldo che utilizzano le più recenti camere di fusione (senza serbatoi riscaldati e contenitori con alette) sono i veri sistemi Tank-FreeTM. Dato che la fusione dell’adesivo avviene secondo una logica first-in-first-out (la prima colla che entra è la prima a uscire), questi sistemi riescono a mantenere costante la temperatura dell’adesivo.
Con questo approccio alla fusione dell’adesivo, le cere non evaporano e l’adesivo non si deteriora. Mantenendosi le proprietà dell’adesivo, non è necessario che l’operatore cambi le impostazioni una volta che il processo è stato ottimizzato. Si ottiene così l’affidabilità del sistema a caldo e la qualità di adesivo che viene applicata è sempre la stessa.
Grazie a un maggiore controllo e alla possibilità di monitorare l’erogazione dell’adesivo a caldo, i responsabili delle applicazioni per l’imballaggio di fine linea possono ora contare su un processo ottimizzato e lavorare con la massima efficienza possibile.
Standardizzando l’imballaggio di fine linea e i processi di chiusura di scatole e cartoni, i produttori possono finalmente ottenere processi controllati, attuare metodi di produzione snella e infine raggiungere i propri obiettivi di redditività.
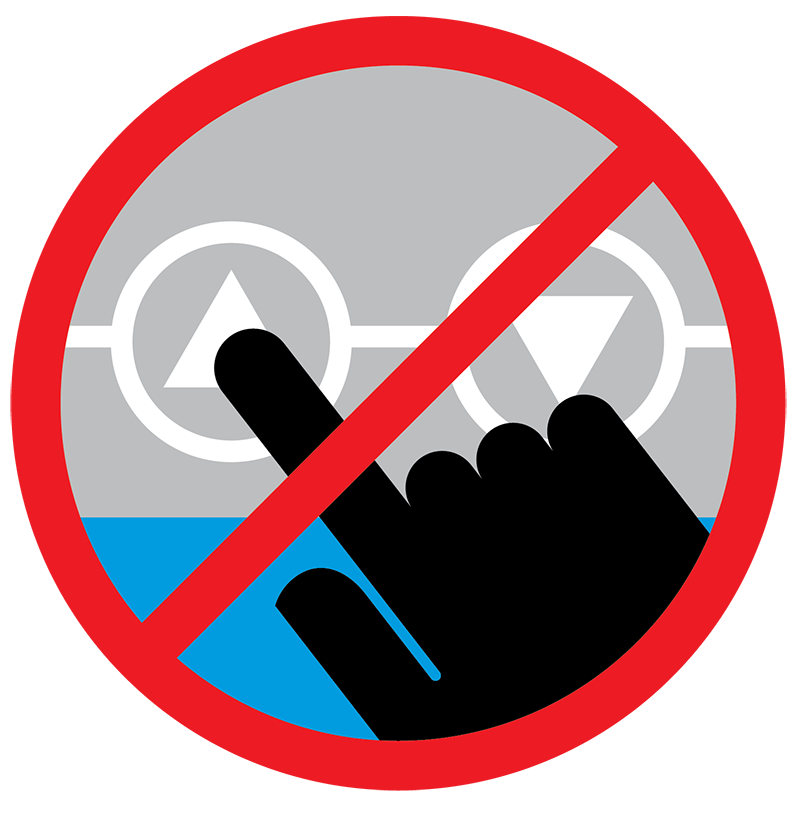
A seconda delle applicazioni, gli operatori che usano i sistemi a caldo Tank-FreeTM possono lavorare per un anno o più senza dover cambiare le impostazioni e persino senza toccare il sistema.
Articoli correlati
6 ragioni per scegliere InvisiPac
Sei ragioni per cui molte aziende sono già passate a InvisiPac nelle loro linee di confezionamento.
Aspetti da considerare quando si seleziona un sistema di applicazione a caldo
5 aspetti da considerare quando si sceglie il sistema di applicazione a caldo per la propria operazione di imballaggio.
Come ridurre i costi di manutenzione della linea d’imballaggio
Scoprite i vantaggi del passaggio da un sistema con serbatoio a un sistema tank-free