Case Study: Li-ion Battery Manufacturing
Étude de cas : Fabrication de batteries li-ion
An EV battery manufacturer had to determine the best foam encapsulation process for a new cell module design. Quick collaboration with Graco put it into production by a critical deadline.
Un fabricant de batteries li-ion optimise le processus d'enrobage de mousse
Un fabricant de batteries li-ion avait besoin d'une solution de coulée des cellules pour répondre aux exigence du secteur en matière de prévention de l'emballement thermique et de la propagation de la chaleur pour la conception de son module de batterie à cellules cylindriques. Le fabricant éprouvait des difficultés à déterminer les points d'injection appropriés, les paramètres de distribution et l'impact de la dynamique complexe des fluides. Mis à part les problèmes de conception, le fabricant devait faire face à une date de lancement critique et avait besoin d'un processus prêt pour la production afin de pouvoir planifier sa ligne de production.
Problèmes liés au processus
Chaque conception de module de cellule cylindrique présente des caractéristiques et des exigences uniques qui peuvent avoir une incidence sur les débits et les points d'injection pour distribuer la bonne quantité de matériau dans le module de manière uniforme. Avec cette conception, les problèmes liés au processus étaient les suivants :
- La conception de la batterie ne pouvait pas être modifiée à ce stade avancé
- La distribution devait s’exécuter par le haut du module de batterie, avec une certaine flexibilité pour l’injection depuis le côté du module.
- Les cellules de la batterie étaient très rapprochées et présentaient une distance minimale entre elles, entraînant une restriction supplémentaire de débit.
- Accès pour que la mousse s'écoule dans le module de la batterie par le haut avec des restrictions très strictes.
- La durée du processus était cruciale pour les opérations du client.
Notre processus de collaboration
Notre équipe d'ingénieurs en application a travaillé directement avec l'équipe de designers du fabricant de batteries et le fournisseur de matériaux pour mettre au point une solution de traitement répondant aux exigences en matière d'efficacité opérationnelle, de qualité de produit et de répétabilité de l'application des matériaux. Grâce à notre laboratoire de développement, à notre équipe d'experts en application et à notre partenariat avec le fournisseur de matériaux, nous avons réalisé des essais pour déterminer la méthode d'application optimale, laquelle a permis de définir les débits, les techniques d'application et les points de distribution pour le procédé de production final.
Essai des matériaux - Une étude approfondie du rapport et de la répétabilité a été menée pour définir les exigences optimales en matière de mousse et d'équipement.
Spécification des équipements - À partir d'essais antérieurs sur des applications similaires et de notre évaluation des matériaux, nous avons spécifié la combinaison idéale d'équipements en fonction de l'application visée.
Essai d'application - À l'aide de modèles de prototypes et de modules fournis par le fabricant de batteries, nous avons évalué et validé les spécifications du processus proposé.
RÉSULTATS
- Remplissage de & mousse de qualité : la soupape de mélange dynamique Voltex et le système de distribution de mélange EFR (plein débit amélioré) ont permis d'obtenir une mousse soigneusement mélangée, une distribution uniforme dans tout le module et la répétabilité des doses requises pour le processus de production.
- Optimisation de la distribution : en fonction des essais en laboratoire, nous avons déterminé les paramètres de mélange, les débits et les points d'injection appropriés pour distribuer une quantité précise de matériau dans le module de manière uniforme.
- Réduction du temps de traitement : grâce à la modélisation et aux essais de distribution, nous avons optimisé le jet de mouvement pour réduire davantage le temps de traitement.
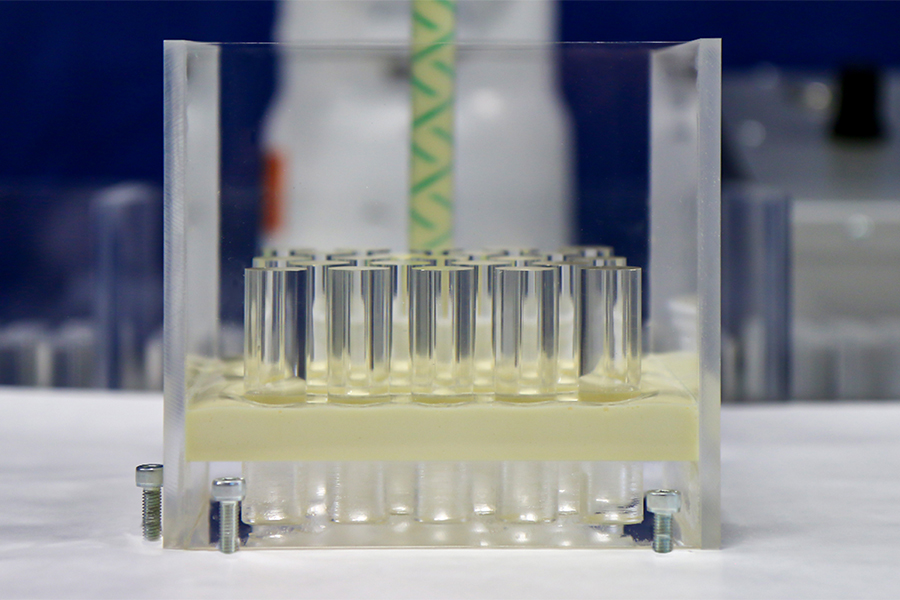
- Quality foam and fill: The Voltex Dynamic Mix Valve and Electric Fixed Ratio (EFR) Metering System provide thoroughly mixed form, even distribution throughout the module, and shot repeatability.
- Optimized dispense: With the proper mixing parameters, flow rates, and dispense injection points, an accurate amount of material is evenly dispensed into each module.
- Rapid process time: The modeling and dispense trials helped optimized the motion pattern to reduce the required processing time.
Collaborate with Us
Innovation truly comes through collaboration with Graco expertise and material supplier partnerships. We strive to deliver custom solutions backed by our global support network.
Contact our team for help with your application.
Related Articles
Enrobage de mousse des cellules de batterie cylindriques
Découvrez l’enrobage de mousse et son rôle dans la fabrication de modules de batterie haute performance qui restent sûrs dans toutes les conditions de défaillance.
Régulation thermique pour la fabrication de batteries et d'électronique de véhicules électriques (VE)
Qu'il s'agisse d'assembler des batteries de véhicules électriques (VE) et des produits électroniques ou de miniaturiser des cartes de circuits imprimés (PCB), la régulation thermique demeure essentielle pour la longévité, l'efficacité et la sécurité.
Joint du bloc batterie - Batterie pour VE
Un joint de qualité est essentiel pour les performances et la longévité des batteries des véhicules électriques et pour la protection des composants intégrés contre les infiltrations d'eau et d'autres conditions environnementales difficiles.