Contrôle de la qualité des emballages pour accroître la fiabilité et la rentabilité
Optimisation du processus de production
Dans de nombreux cas de fabrication industrielle, le facteur clé de rentabilité est un processus de fabrication à la fois efficace et efficient. Les ingénieurs de processus investissent beaucoup de temps et de ressources dans les tests et les améliorations pour aboutir à un processus optimisé avec une qualité améliorée.
Dans l’industrie automobile, la standardisation par conformité aux normes ISO et aux techniques de production au plus juste (lean manufacturing) sont monnaie courante. Dès lors qu’un processus est défini, son altération en cours de production équivaudrait à un suicide professionnel.
Conditionnement en bout de chaîne dans le cadre des normes ISO et de la production au plus juste
La volonté d’obtenir les homologations ISO 9000 et ISO 9001 a conduit de nombreuses entreprises à définir leurs processus et à s’y tenir. Ces homologations ne sont pas centrées sur ce que les processus doivent être précisément, elles sont simplement les vecteurs permettant de consigner les processus et d’utiliser la documentation pour vérifier que les fabricants maintiennent le niveau de qualité de leurs produits.
Lorsque les usines mettent en place des méthodes de production au plus juste, l’objectif est d’éliminer le gaspillage pour améliorer l’efficience et réduire les coûts, ce qui au final apporte de la valeur ajoutée au client.
En raison de trop nombreux facteurs au-delà de leur contrôle, les responsables qualité ont consacré peu d’efforts au développement de processus de conditionnement en bout de chaîne « au plus juste » ou optimisés.
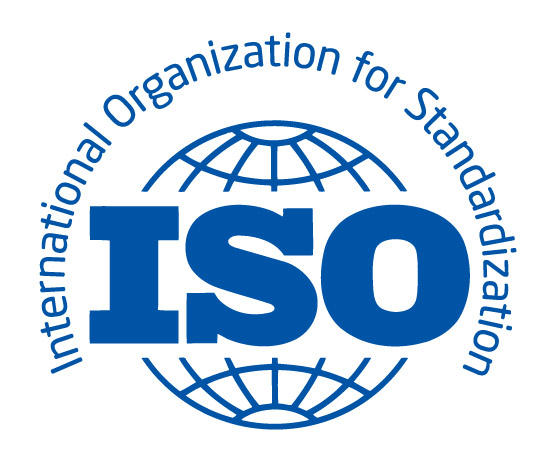
Technologie obsolète et fabrication sans gaspillage
Les programmes de production au plus juste tendent à exclure les applications de conditionnement en bout de chaîne, et ce, en grande partie car, en raison des capacités limités des systèmes, il n’existe aucun moyen d’optimiser le processus. La fusion en réservoir, technologiquement dépassée, et les pompes à engrenage rendent le processus quasiment impossible à standardiser.
Comme les appareils anciens font fondre l’adhésif à l’aide d’un réservoir, il est très difficile de maintenir une température d’adhésif constante. La colle située vers l’extérieur du réservoir chauffe plus vite et commence à se détériorer pendant que la colle située au centre atteint la température opérationnelle.
Les systèmes avec colle thermofusible équipés d’un réservoir provoquent des problèmes de réglage constants.
On considère généralement que les opérateurs de chaîne doivent régler en permanence la machine pour obtenir le résultat voulu. Ce manque de régularité réduit la possibilité d’exercer un contrôle de processus d’ensemble. Il est impossible de régler l’appareil une bonne fois pour toutes, car le réglage de l’opérateur du premier quart diffère souvent de celui de l’opérateur du troisième quart.
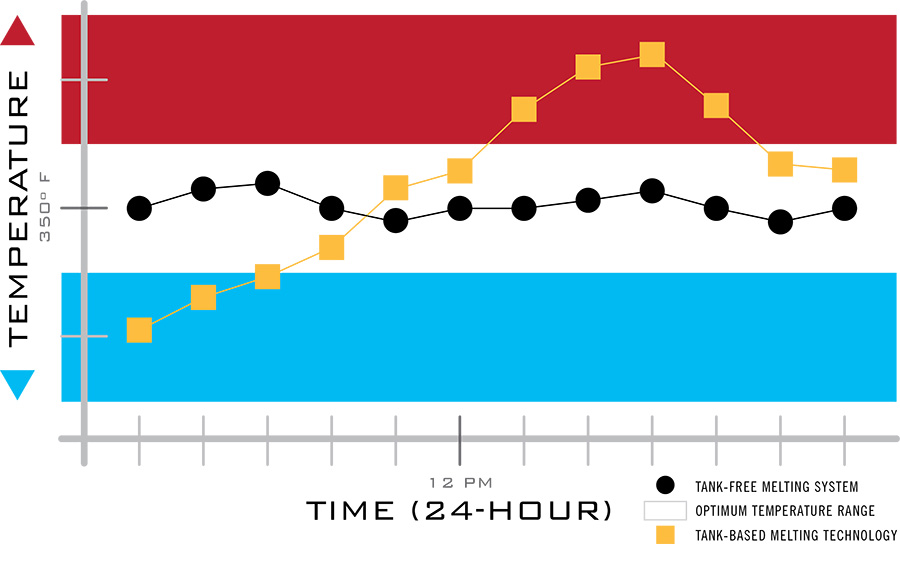
Certains appareils à colle thermofusible récents continuent de reposer sur cette approche ancienne de la thermofusion. Par exemple, certaines machines possèdent des réservoirs plus petits munis d’ « ailettes » situées au fond afin d’augmenter la surface de fusion. Il ne s’agit toutefois que de variations du réservoir chauffé, et cela ne permet pas de conserver une température constante de l’adhésif, en particulier si celui-ci reste stocké dans le réservoir, ne serait-ce que brièvement.
Lors de votre évaluation des systèmes de colle thermofusible, n’oubliez pas de poser au fournisseur les six questions essentielles, et demandez-lui de vous détailler précisément la façon dont l’adhésif est fondu.
Les adhésifs alternatifs contribuent à remédier aux incohérences des matériaux
Parallèlement à la technologie de thermofusion, une meilleure compréhension des adhésifs thermofusibles peut aider les ingénieurs à concevoir des processus de conditionnement en bout de chaîne qui soient optimisés. Les adhésifs thermofusibles possèdent quatre composants :
1) Mélange de base : la colonne vertébrale de l’adhésif, responsable de propriétés telles que la résistance mécanique, la souplesse, ainsi que de propriétés d’utilisation telles que la résistance thermique et la résistance chimique. Dans la majorité des cas, le composant de base de l’adhésif n’est pas utilisé seul.
2) Agent poisseux : ce qui donne sa tenue à chaud ou son caractère relativement collant à l’adhésif. L’agent poisseux utilisé dépend des propriétés d’adhérence nécessaires au support spécifique, et déterminent généralement la couleur et l’odeur de l’adhésif thermofusible.
3) Diluant : cire ou huile permettant de modifier la viscosité de l’adhésif et sa vitesse de durcissement.
4) Stabilisateur : ajouté au cours des dernières années pour stabiliser la viscosité et pour contribuer à empêcher la carbonisation des adhésifs stockés longuement dans les réservoirs.
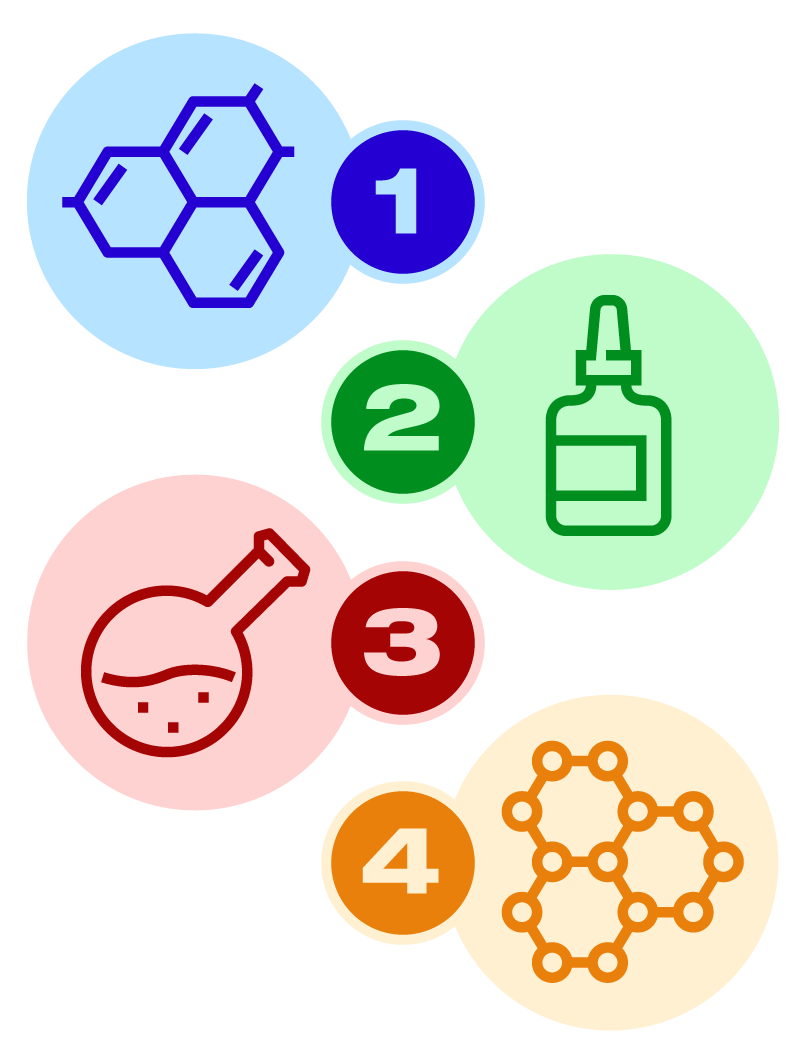
Contrôle de la qualité et performances
La standardisation des processus signifie que ces composants font l’objet d’une surveillance attentive lors de la fusion, du transfert et de la distribution de l’adhésif. L’objectif final est que les propriétés de l’adhésif thermofusible répondent aux critères de performance.
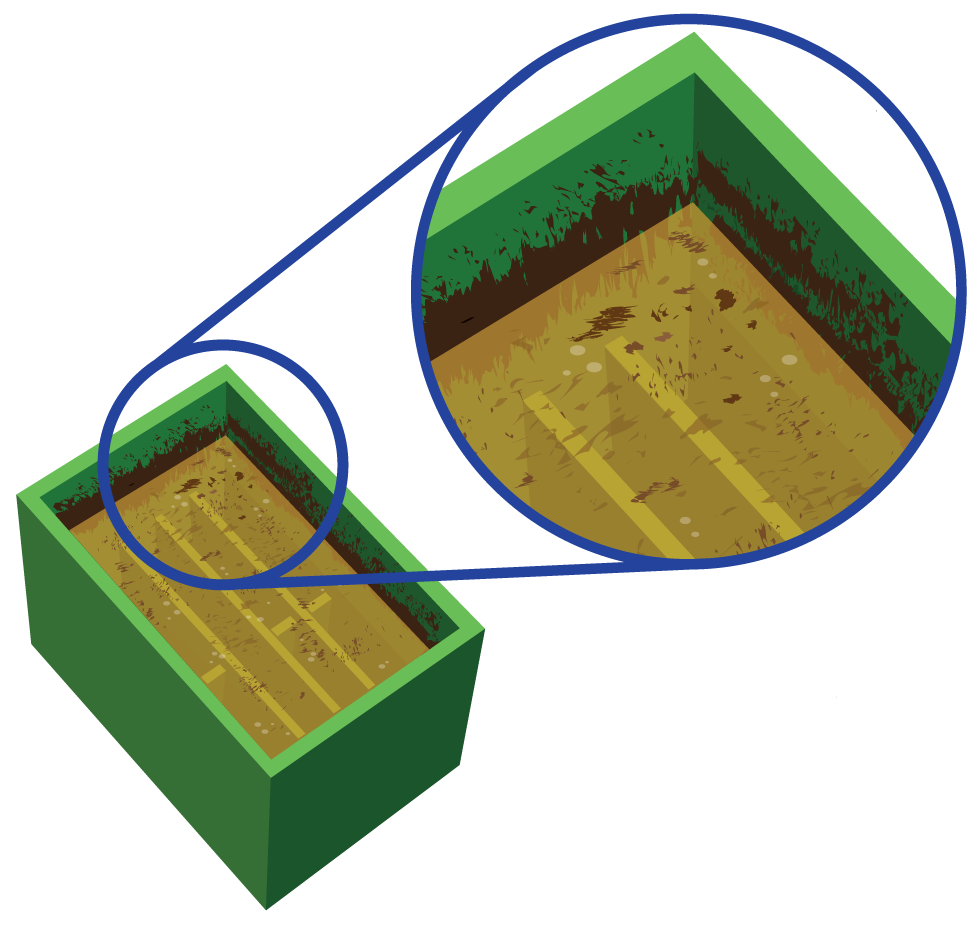
Avec la technologie de thermofusion traditionnelle à réservoir, la consistance de la colle est en perpétuelle évolution. Cette situation était acceptée comme faisant partie des applications de conditionnement en bout de chaîne, comme la dégradation de la colle et la carbonisation de l’adhésif.
Pour répondre aux problèmes de consistance et de carbonisation de l’adhésif, les fabricants se sont tournés vers les fournisseurs de colle pour demander des adhésifs thermofusibles alternatifs, tels que les métallocènes. Les métallocènes ont tendance à provoquer moins de colmatage, à posséder une plus grande stabilité de température, et à fonctionner sur des plages de température plus larges. Toutefois, ces adhésifs alternatifs sont plus coûteux pour les fabricants et donc moins rentables.
La qualité grâce à une technologie améliorée
Les systèmes de thermofusion récents dotés de chambres de fusion (ni cuve chauffée, ni réservoir à ailettes) sont les appareils véritablement dotés de la technologie Tank-FreeTM (sans réservoir). Dans la mesure où ces appareils font fondre l’adhésif par ordre d’entrée dans la machine, ils permettent de le maintenir à une température constante.
Avec ce mode de fusion, les cires ne s’évaporent pas et l’adhésif ne se détériore pas. Comme les propriétés sont conservées, l’opérateur n’a besoin de changer de paramètre une fois que le processus a été fixé. Le système de thermofusion est fiable et la même quantité d’adhésif est appliquée à chaque fois.
Avec un plus grand contrôle et avec la possibilité de surveiller la distribution d’adhésif thermofusible, les agents responsables du conditionnement en bout de chaîne peuvent désormais compter sur un processus optimisé et le plus efficient possible.
En standardisant le conditionnement en bout de chaîne et le processus de fermeture des boîtes et cartons, les fabricants contrôlent enfin les processus, mettent en œuvre des méthodes de production au plus juste et atteignent leurs objectifs de rentabilité.
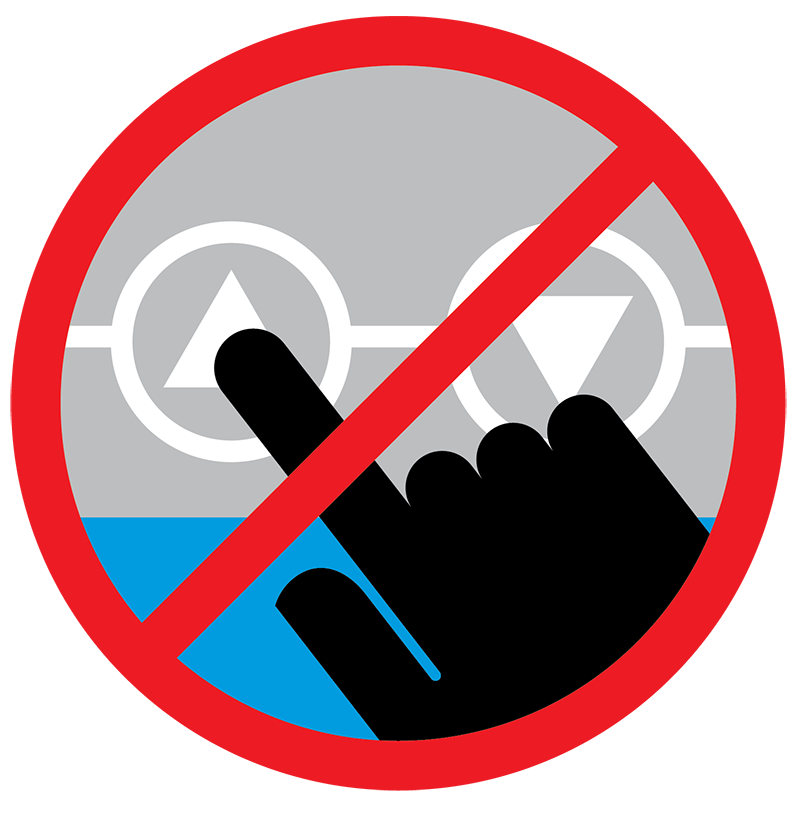
En fonction des applications, les opérateurs utilisant les systèmes de thermofusion Tank-FreeTM peuvent rester plus d’une année sans modifier le réglage, ni même toucher le système.
Articles connexes
6 raisons de choisir InvisiPac
Six raisons pour lesquelles de nombreuses entreprises sont déjà passées à InvisiPac sur leurs lignes d’emballage.
Adoption de l’InvisiPac par le site de Mondelēz Namur
Après une période d’essai de six mois, l’usine de Mondelēz située à Namur a décidé d’adopter définitivement l’InvisiPac de Graco comme système de distribution de colle thermofusible.
Améliorez la performance de votre système de thermofusion
Augmentez la rentabilité globale de votre ligne de conditionnement en prenant conscience du coût élevé des procédés obsolètes.