Peinture de moteurs de véhicules agricoles
Les équipements Graco jouent un rôle essentiel dans une nouvelle ligne automatique de revêtement de moteurs, dans l'usine du groupe MANTA en Italie.
Le groupe MANTA, basé à Foggia, en Italie, a mis l’accent depuis plus de 30 ans sur l'assemblage et le revêtement de composants aérospatiaux et automobiles. En 2021, l’entreprise s’est vu confier la peinture des moteurs de machines agricoles. Pour accomplir cette mission, MANTA a identifié un pool de fournisseurs pour construire une chaîne de peinture entièrement numérique, conforme à la norme Industry 4.0, automatisée, flexible et rapide.
Les objectifs de la nouvelle ligne de revêtement étaient ambitieux. Elle devrait permettre de peindre plus de 700 variantes de moteurs en quatre couleurs différentes, avec une capacité de 85 000 moteurs par an. Elle devait également être entièrement intégrée numériquement dans le système de gestion de l'entreprise, pour permettre un suivi attentif de chaque étape de revêtement et le respect des exigences de qualité.
Gaiotto, Savim et CM Automazione ont été impliquées dans les aspects techniques de l'ingénierie de l'usine et Graco s’est vu confier la responsabilité de l'application de la peinture. Le système de peinture monocouche à l'eau à appliquer sur les moteurs a été validé par un laboratoire externe (CRF) avant le démarrage de la production.
Des coopérateurs harmonieux
L'installation de peinture a été construite par Savim (Arbizzano, Vérone, Italie), équipée de robots Gaiotto et intègre un convoyeur pas à pas XD45/59 conçu et fourni par CM Automazione (Giussano, Monza e Brianza, Italie). La ligne peut accueillir jusqu'à 116 unités de manutention d'une capacité de charge maximale de 850 kg chacune. À plein régime, la chaîne est capable de peindre 370 moteurs par jour.
Pour l'alimentation en peinture, l'équipement d'application de la peinture et le système de changement de couleur, MANTA s'est appuyé sur Graco et son intégrateur Comaind (San Giovanni Lupatoto, Vérone, Italie), dont la collaboration a été fondamentale dans l'une des phases les plus critiques de ce projet.
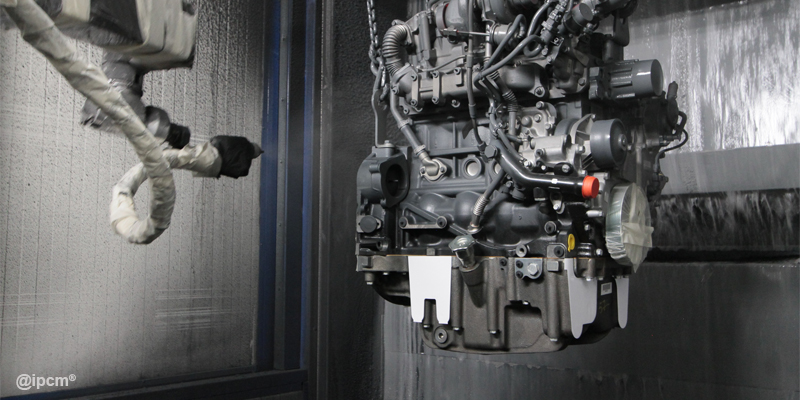
Un processus rationalisé
Chaque moteur passe par plusieurs étapes de préparation : masquage, prétraitement chimique avec phosphodégraissage, nettoyage à l'eau déminéralisée et séchage en trois étapes (tunnel de pré-séchage, soufflerie robotisée, four à 90°C) avant que les moteurs ne passent par une zone de refroidissement.
La peinture liquide est ensuite appliquée dans deux cabines à rideau d'eau pressurisées, à température et humidité contrôlées, fournies par Savim, chacune équipée d'un robot articulé Gaiotto tournant à 180° qui peint un côté du moteur. L'épaisseur minimale appliquée est de 50 microns. Une troisième cabine manuelle est utilisée pour les retouches. La ligne se termine par un tunnel d'évaporation et un four pouvant accueillir 50 moteurs à 100 °C pendant 90 minutes. Les moteurs sont ensuite soumis à un contrôle de qualité en ligne pour approbation finale.
Le système d'application de peinture
« Nous avons conçu le système d'alimentation et d'application de la peinture en collaboration avec Gaiotto pour gérer les quatre couleurs appliquées par MANTA », explique Davide Galvani, de Comaind. « La plus utilisée est le gris, qui représente près de 90 % de la production. Les trois autres couleurs sont le jaune, le gris Perkins et le transparent, qui occupent les 10 % restants des volumes. »
La planification du revêtement ne s’exécute pas par lots, mais par chaque moteur. Il fallait donc concevoir un système de changement de couleur très rapide, en 30 secondes seulement. L'unité de gestion des peintures est dotée d'un conteneur de 1 000 kg pour la couleur grise et de fûts de 200 litres pour les autres teintes. La peinture est maintenue agitée par un agitateur électrique certifié ATEX à ailettes extensibles et un système de remplissage relié à un réservoir de 100 litres où une pompe Graco Endura-Flo fait circuler la peinture à une pression de 2,5 à 3 bar. Ce réservoir pré-alimente le doseur multicomposants Graco PD1K équipé de quatre pompes séparées, une pour chaque couleur, afin de garantir une vitesse de changement de couleur maximale à bord du robot.
En outre, une filtration à 60 mailles est effectuée sur le produit recirculé. Le dispositif PD1K possède également sa propre unité de filtration à la sortie du pistolet. Les deux robots de revêtement sont équipés chacun de deux pistolets automatiques compatibles Graco AirPro. L’un des pistolets gère la peinture grise, tandis que l'autre est alimenté par des vannes de changement de couleur positionnées à environ 40-50 cm du pistolet, presque sur le poignet du robot; une vanne est destinée au rinçage du circuit, les trois autres aux teintes. L'unité de gestion de peinture alimente également la cabine de retouche, où un pistolet est disponible pour chaque couleur qui s’active avec la couleur correcte en fonction du moteur entrant.
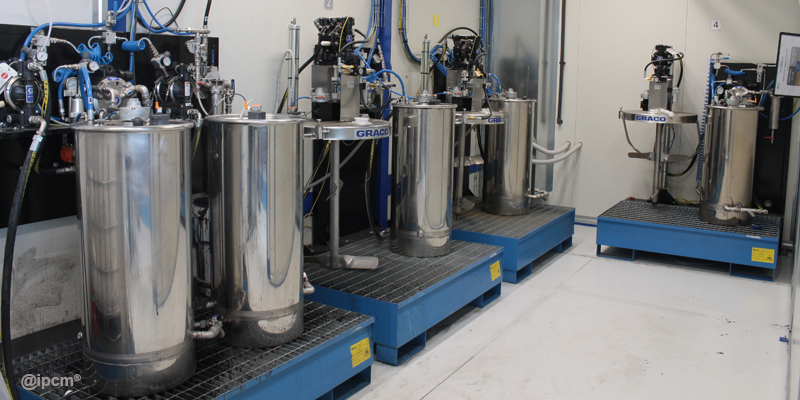
Le PD1K de Graco au cœur du système
« Nous avons choisi le doseur multicomposants Graco PD1K car il permet de contrôler directement le débit de peinture au niveau du pistolet et de l'ajuster en fonction du mouvement du robot pendant la phase de peinture », ajoute M. Galvani. « Cette unité permet également l’analyse des paramètres techniques/de production et des interfaces avec le système 4.0 de la ligne. »
Grâce à sa technologie unique d'entraînement des pistons par encodeur et à ses vannes de commande actives, le PD1K offre une précision du rapport de mélange inférieure à 1 %, garantissant une distribution fluide et exacte à chaque fois. Le système maintient cette précision exceptionnelle, indépendamment de la pression de refoulement, de l’altitude, de la viscosité des produits, de la température et de l’actionnement du pistolet.
De plus, le fait de rapprocher le point de mélange du pistolet diminue la zone de rinçage. Ceci se traduit par une réduction du gaspillage de produits, un rinçage plus rapide et une efficacité accrue. Il est possible de programmer un rinçage complet dans le module d'affichage avancé de l'unité, et même de pré-configurer jusqu’à cinq recettes de rinçage différentes avec des solvants individuels, des horaires spécifiques et d’autres facteurs.
MANTA s'intéresse également à la rentabilité du PD1K, grâce à un contrôle impeccable du débit, à des changements de couleur rapides et à une distribution efficace. Sa méthode de rinçage unique réduit la consommation de solvants et les pertes de produits à hauteur de 80 %, tandis que les dépenses liées à la maintenance sont bien moindres par rapport aux pompes à engrenage, ce qui en fait une option économique pour la ligne de peinture MANTA.
Le dispositif convient parfaitement aux applications tant manuelles qu’automatiques. Il est capable de faire fonctionner jusqu’à quatre pompes, de distribuer différents produits chimiques et de suivre la durée de vie de trois pistolets pulvérisateurs, le tout sur un seul système. Jusqu’à 30 couleurs peuvent être gérées dans des configurations 1K à 4K et il est possible de combiner des produits habituellement séparés comme l’époxy et l’uréthane ou les peintures aqueuses à base de solvant.
Opérationnel de qualité élevée
La ligne a commencé à produire à plein régime à la fin de l'année 2022. La phase de démarrage a nécessité un processus d'apprentissage, d'autant plus que la peinture à l'eau est beaucoup plus liquide que son équivalent à base de solvant. Au départ, quelques retouches manuelles ont été nécessaires car les programmes de peinture des robots n'étaient pas entièrement optimisés. Lorsque ces derniers ont été ajustés, le travail manuel nécessaire a été progressivement réduit.
MANTA - et ses clients - sont impressionnés par la haute qualité de la peinture des moteurs, en partie grâce à la qualité élevée et au contenu technologique des systèmes Graco.
La vision globale de cette ligne de peinture de moteurs
La nouvelle installation de peinture et la ligne de peinture de moteurs entièrement automatisée sont le fruit d’un travail d’experts unissant leurs forces. Ils combinent l'expertise de Gaiotto, Savim, CM Automazione, Comaind et Graco.
La ligne se compose de différentes stations. Notre système d'alimentation et d'application de la peinture est l'une d'entre elles. Examinons de plus près la situation dans son ensemble, chaque chiffre représentant une station distincte.
- La station de masquage. Pour protéger les surfaces sensibles des infiltrations d'eau lors du prétraitement
- Prétraitement chimique en 3 étapes avec graissage au phosphure, nettoyage à l'eau déminéralisée.
- Tunnel de pré-séchage. La première étape du processus de séchage.
- Soufflage robotisé. Pour éliminer toute eau de nettoyage restant dans les orifices.
- Four à 90 °C. La troisième et dernière étape du processus de séchage.
- Zone de refroidissement.
- Phase de masquage 2. Environ 100 dispositifs de masquage sont appliqués.
Le cycle se poursuit par l'application de la peinture liquide dans deux cabines à rideau d'eau pressurisées, à température et humidité contrôlées. L'épaisseur minimale appliquée est de 50 microns.
Une troisième cabine manuelle est utilisée pour les retouches.
La ligne de peinture de moteurs se termine par un tunnel d'évaporation et un four pouvant accueillir 50 moteurs à 100 °C pendant 1 heure 30 minutes.
Pour plus d'informations sur le système PD1K de Graco, remplissez le formulaire ci-dessous.
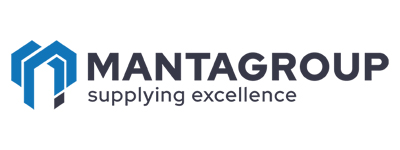
Articles connexes
L’usine John Deere de Mannheim installe le système d’alimentation en peinture 2KS de Graco
L’usine John Deere de Mannheim a investi dans un nouveau système d’alimentation en peinture Graco dans le but de répondre à des normes de qualité strictes et d’augmenter la fiabilité de son procédé.
Les processus manuels appartiennent au passé : l’automatisation pour une productivité accrue
Découvrez comment les pistolets pulvérisateurs AirPro de Graco s’intègrent parfaitement à votre processus d’automatisation.
Optimisation de l’application de peinture sur des boîtiers de vitesses pour machines autotractées
Bonfiglioli confirme la valeur des doseurs ProMix Easy et ProMix 2KS et des pistolets pulvérisateurs G40 et AirPro de Graco à son usine italienne de Forlì spécialisée dans les boîtiers de vitesses