How to avoid pin bushing wear and minimize repair costs
Auto Lube reduces contamination and wear of pin bushing, extends machine life and prevents downtime.
Proper lubrication reduces excessive contamination and wear of bronze pin/bushings. In turn, that helps to maximise the profitability of capital equipment and uptime, decreasing the need for costly repairs.
Today’s construction and mining equipment use the most sophisticated form of bronze pin bushings, which reduce wear significantly. The purpose of wear materials is to reduce damage to structural steel components. After all, it’s much cheaper to replace a bronze bushing than something like a wheel loader boom arm. However, there is an issue with the material: bronze is not contamination-proof.
THE EFFECT OF CONTAMINATION
The effect of contamination on pin bushings is a direct result of scaring, skidding/ploughing and smearing. Excessive contamination build-up between a pin and bushing surface restricts the pin’s movement by increasing friction.
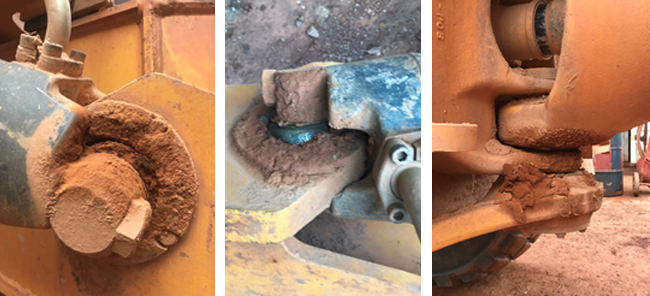
Open lube points that lack fresh grease allow dirt to easily enter the system.
Without a solution, the increasing friction and load pressure lead to the pin gouging the bronze, eroding the bushing’s material so it can keep rotating. The material deposits then cause a vicious cycle of continued contamination and wear. When all the bronze bushing material is worn away, the pin will start digging into the steel structure of the equipment.
Wear evolution due to contamination:
- Good bushing
- Worn bushing
- Worn bushing affecting the frame
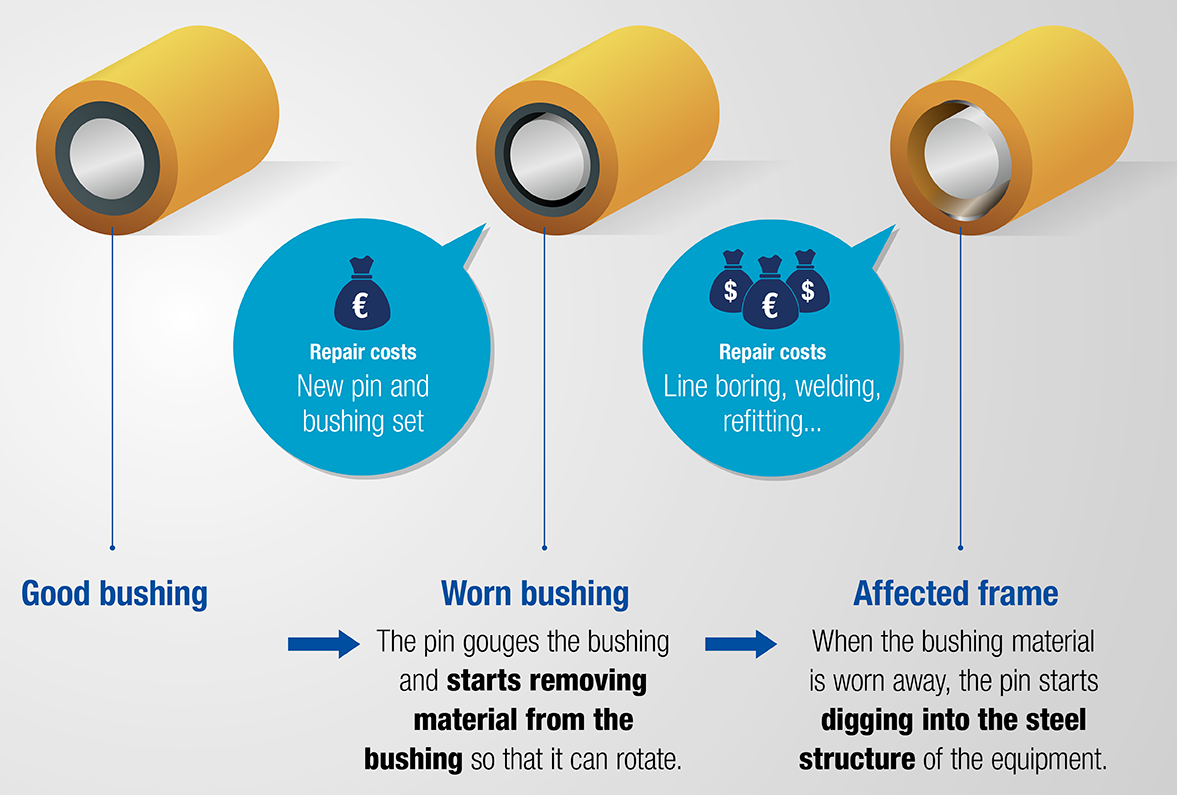
A worn bushing may need replacing, which means production machinery is generally put out of service.
- If only the bushing is damaged, the pin and bushing set may need to be replaced.
- If the structural steel of the equipment is damaged, you will probably need a ‘line bore’, increasing costs exponentially.
Cost of bushing pin repairs
Replacing a damaged pin/bushing can cost up to $1, 500 and is quite time-consuming, as your equipment may need to be moved to an off-site workshop. A “simple” replacement of worn parts lasts between 5 to 8 hours if the pin/bushing is not stuck.
When a worn pin has damaged the equipment's structural steel, you are faced with replacement costs, additional downtime, repair costs for line boring ($500 per hole), welding, and refitting
The importance of proper lubrication maintenance
Proper lubrication can significantly reduce the need for replacement or repair of pin bushings. Most pin bushings have ‘grease grooves’ on the inner diameter where applied lubricants form a thick film for the pin to rotate on.
These lubricants also help to “purge” contaminants from the bushing by forcing out unwanted materials. However, if these grooves aren’t lubricated (and purged) on time, they become home to contamination – resulting in wear.
Automatic lubrication minimizes damage and costs
Automatic lubrication systems consistently dispense accurate doses of lubricant while the system is working. Therefore, the entire pin is coated and the circumference is purged thoroughly.
A well-lubricated pin increases equipment life extends machine performance and reduces the maintenance- and repair frequency. That leads to minimal downtime, preventing loss of revenue.
Would you like to access all this information in a handy overview?
FIND YOUR PERFECT GRACO AUTOMATIC LUBRICATION SYSTEM
Graco manufactures automatic lubrication systems designed explicitly for yellow iron construction and mining equipment. Use our Yellow Iron Kit Selector to find out which automated lubrication system is the perfect match for your installation.
Contact an expert
Related Articles
Keeping Komatsu dump trucks up and running
The Graco Mining Kit was installed on 14 Komatsu dump trucks to provide efficient automatic lubrication in tough conditions.
How to avoid grease contamination and clogged Zerk fittings on construction and mining equipment
Automatic lubrication systems prevent clogged grease fittings by dispensing accurate doses of lubricant during operation.
What’s the return on investment (ROI) of an automatic lubrication system?
An automatic lubrication system provides many benefits, but how do you calculate its ROI?