The pitfalls of manual lubrication
Manual lubrication poses important disadvantages in terms of costs, safety and productivity.
Manual lubrication systems are no guarantee for the right amount of lubricant at the right time and in the right place. This leads to serious risks for industrial applications where an optimal lubrication is necessary to ensure efficient processes and a minimum of downtime and maintenance costs.
The ongoing cost efficiency trend forces industrial plants worldwide to downsize their maintenance departments. At the same time the number of production machines and lubrication points that require regular lubrication stay the same. On top of that there is an increase in environmental and safety regulations that require plant maintenance managers and personnel to perform time-consuming tasks. These universal challenges will not go away, putting most industries under pressure to be more efficient and improve machine uptime.
Why manual lubrication does not match with today’s industrial challenges
Manual lubrication is not consistent with today’s cost efficiency challenges and pro-active maintenance strategies. A conventional lubrication system such as a grease gun cannot guarantee an optimal lubrication that provides your equipment with the right amount of lubricant at the right time and in the right place – usually while the machine is in operation.
With manual lubrication methods, you risk under-lubrication or over-lubrication, with both having a range of negative effects on your machine components, productivity and overall costs.
DISADVANTAGES OF MANUAL LUBRICATION
Choosing a manual lubrication system for your industrial applications might seem a cheap solution at first sight. However, when you take into account all issues that come with it and compare it with the advantages of an automatic lubrication system, this last one will prove to be the most profitable solution at the end of the line.
The issues with manual lubrication:
- Many machines are dangerous to lubricate while running
- Safety is an issue when lubricating hard-to-reach bearings
- Lock-out and tag-out procedures are time consuming and result in lost production
- Over lubrication can cause:
- excess heat build-up
- product spoilage
- bearing seal damage
- clean-up issues
- increased downtime
- Under lubrication can cause:
- increased component wear
- bearing damage
- premature failure
- higher energy usage
- increased operating and maintenance costs
- increased component wear
- Removing guards and covers is time consuming, leading to high labour costs
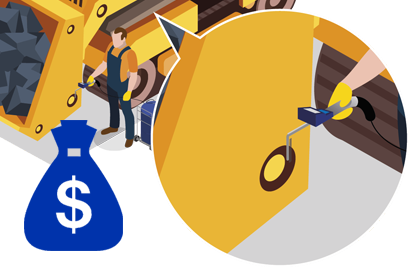
THE IMPORTANCE OF AVOIDING BEARING FAILURE
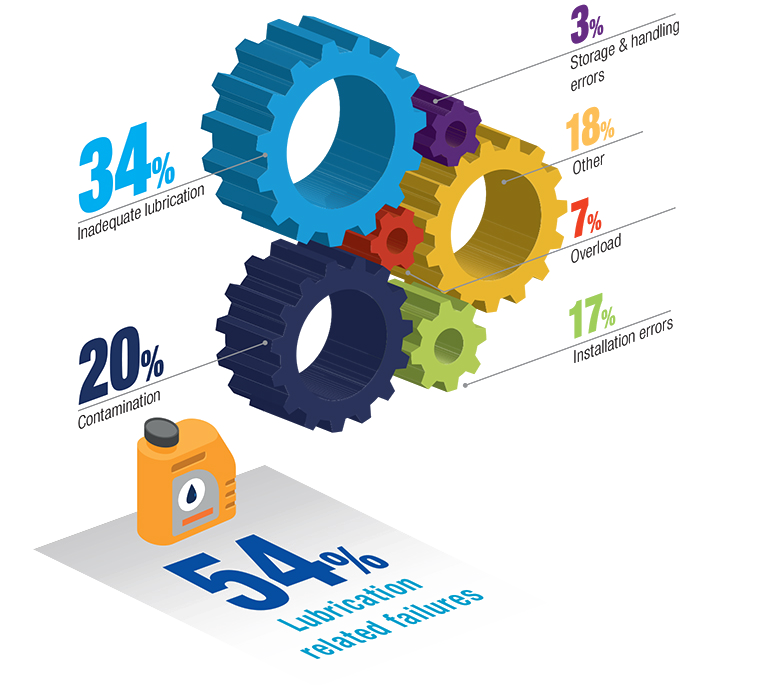
Inadequate lubrication heavily increases the risk of bearing failures. Studies point out that over 50% of bearing failures are the result of improper lubrication. It is crucial to avoid bearing failures in any way possible, because the costs can add up to much more than the replacement cost of the bearing. Take into account the following costs as a result of a bearing failure:
- Loss of production due to downtime
- Labour for repair
- Replacement bearings and related materials
- Production labour cost
- Missed customer deliveries
- Increased safety risks when repairing machinery
5 Reasons Why You Need Automatic Lubrication
Protect your equipment and your employees by utilizing automatic lubrication to grease critical lube points.
Related Articles
What is lubrication and why is it important?
Lubrication is a crucial element in the efficiency and life-expectancy of any rotating equipment.
7 significant advantages of automatic lubrication
Automatic lubrication systems offer many advantages such as reduced downtime and maintenance costs.
The components of an automatic lubrication system
An automatic lubrication system consists of a pump with reservoir, a controller, metering devices, hose and fittings and accessories.