Single line parallel or series progressive?
Which automatic lubrication configuration to choose?
Single line parallel or series progressive: what’s the difference and when should you use one rather than the other?
Automatic lubrication systems lubricate multiple points from a single centralized system. There are many configurations, such as single-line parallel, series progressive, dual-line and multi-line. Each has its specific advantages and disadvantages, and thus its specific application areas.
Centralized automatic lubrication systems lubricate multiple points from a single system, offering significant advantages compared to conventional lubrication systems like a grease gun. There are many configurations, such as single-line parallel, series progressive, dual-line and multi-line. Each has its advantages and disadvantages, and thus its specific application areas. Graco focuses on single-line parallel and series progressive systems.
SINGLE-LINE PARALLEL SYSTEM
A single-line parallel system is the simplest automatic lubrication system. A pump pressurizes the main supply line and fills several individual piston distributors or injectors. Each injector serves one lubrication point and can be easily adjusted to deliver a precise amount of lubricant with a high degree of accuracy.
The injectors operate independently of each other. The advantage of this is that failure of an individual injector, or a blocked supply line, does not disrupt the rest of the system.
Installation and monitoring of a single-line parallel system
With a single-line parallel system, a blocked lube point would not be detected easily at the system level. To monitor the performance of the injectors electronically/automatically, each injector would need to have a sensor connected to the PLC, so lube point monitoring is not possible at an economic level. This places greater importance on regular inspection.
A single-line parallel system is easy to install, maintain and modify. Main supply line distances can go up to 50 meters or even more. Viscous lubricants can be pumped – but you need to consider pressure build-up time and vent time.
System design, adjustments and expansions of a single-line parallel system
System design and quotation are generally easier for a single-line parallel system. The system designer simply has to count and group the lubrication points on a machine to obtain the total number of injectors needed.
Moreover, with a single-line parallel system, it’s easy to increase or decrease the amount of lubrication which will be dispensed. It’s a simple matter of screwing/unscrewing an adjustment nut on the measuring chamber. It’s also easier to expand a single line parallel system. If the pump is capable of providing the additional volume, it’s easy to add extra injectors; this is not so straightforward with a series progressive system.
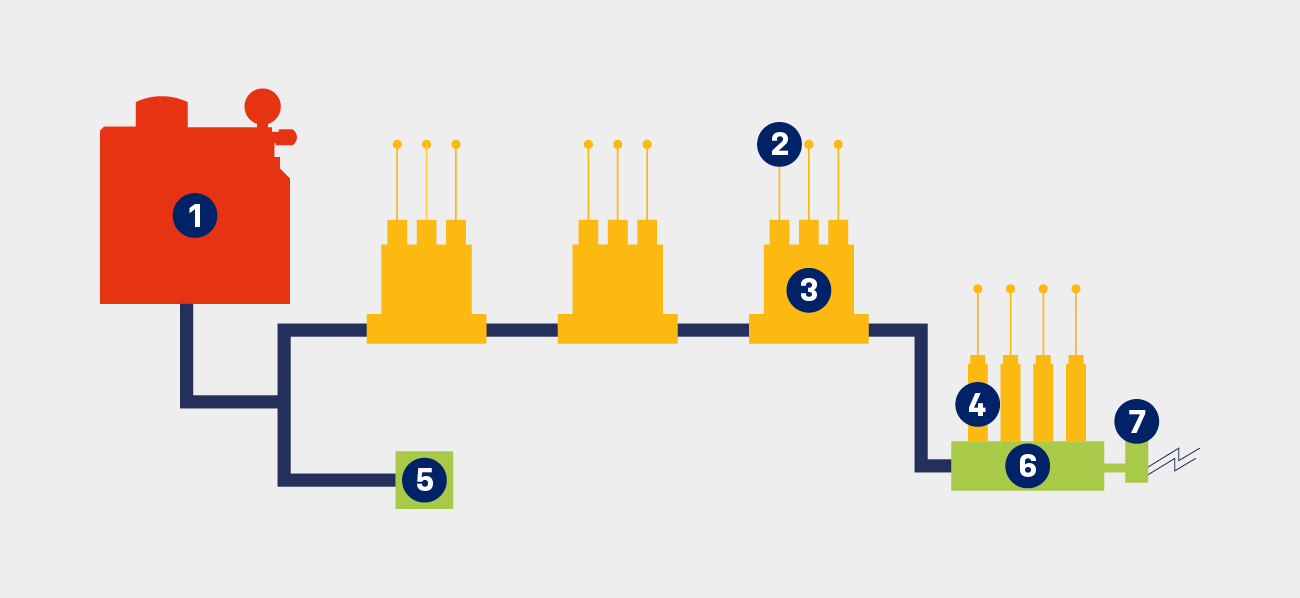
1) Lubrication pump – 2) Lubrication dispense – 3) Piston distributor – 4) Injector – 5) Vent valve – 6) Manifold – 7) Pressure switch
Benefits
- Basic monitoring with pressure switch ensures the system is operating properly
- Designed for higher pressures to handle a wide variety of lubricants up to NLGI #2 as well as oil
- Different sized injectors give you a wide output range to lubricate any size bearing
- One-to-one relationship between the metering device and the lube point for precision dispensing
System considerations
- System requires venting for metering device reset
- Blocked or pinched lines allow the system to continue to work, but those bearings will not receive lubricant
- Monitoring of the pressure build-up and the relief is possible with a pressure switch and visually if the injectors are working
SERIES PROGRESSIVE SYSTEM
In a series progressive system, a pump supplies the lubricant through a master metering valve and optional secondary metering valves to the lubrication points. The metering valves are custom-sized for each lubrication point to deliver the required amount of lube. Each piston inside a divider block is dependent on the flow of the previous piston. Lubricant is therefore delivered to each lube point in succession. This means that if lubricant reaches the final lube point in the network, you know that each point in the network has received its specific amount.
System design, adjustments and expansions of a series progressive system
A series progressive system requires more extensive engineering to set up, and it’s more difficult to add lube points and adjust the delivery volume without considering the whole system set-up. If a line gets blocked and stops delivering grease, it backs up and the entire system stops working. Likewise, if one valve fails, the entire system fails, resulting in increased pressure at the pump and no lubricant delivery.
Monitoring of a series progressive system
If you want to monitor your automatic lubrication system and get feedback on whether it’s working or not, a progressive system should be selected. A central signal can be generated to alert the user to failure, thus making fault detection easy. A failure at any point in the system, upstream or in the divider blocks, will be propagated through the rest of the system, allowing for easy and economic monitoring.
Graco MSP series progressive systems can easily be fitted with a performance indicator to make troubleshooting more effective and to avoid long machine shut-downs.
Series progressive systems can be equipped with a proximity switch to monitor the movement of a piston. The proximity switch can trigger a visual or audio alarm or can be connected to a PLC to indicate a fault. The beauty of this arrangement is that you only need to monitor one of the pistons because if one is not moving, it will not open a channel for the next one. You can, therefore, have scores of lubrication points, yet only one proximity switch will be necessary to monitor the complete system. This is especially useful in applications in remote areas where it might be difficult for a maintenance engineer to access the machine and check the injectors. It’s also useful where the lubrication points are hidden.
For some applications, a broken line indicator can be added to the system to monitor whether the lubricant is reaching the lubrication point. This is especially useful for applications where either the bearing is extremely expensive or the change of the bearing takes a long time, resulting in machine downtime and production losses.
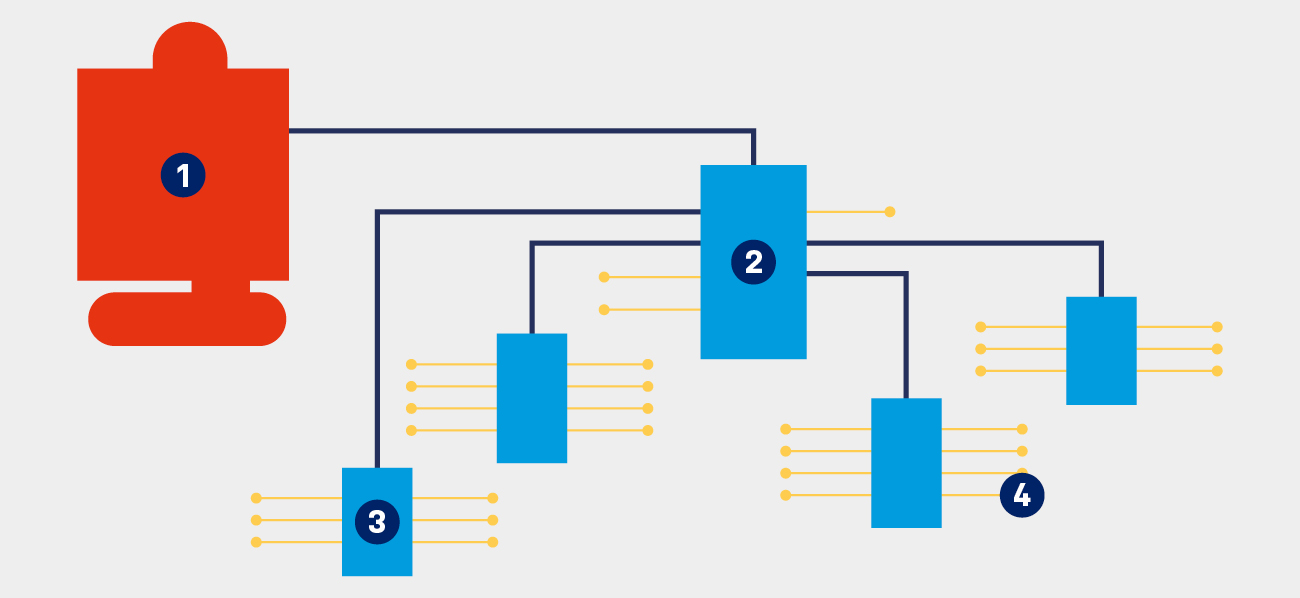
1 Lubrication pump – 2 Master divider block – 3 Secondary divider block – 4 Lubrication dispense
Benefits
- Large number of outputs to handle a full range of oils and greases
- Most advanced and precise monitoring with overall system diagnostics plus troubleshooting at the lube point
- With a zone valve, you can decide where and when to lubricate
- Covers the broadest range of small to large applications
System considerations
- Highly customizable
- Multiple zoning options
- Configure to any application
- Many pump choices
- Multiple feedback and controller options
GRACO LUBRICATION EXPERTS HELP YOU FIND THE BEST SOLUTION
In whatever industry and for whatever application you need automatic lubrication, it’s important to choose the right solution. Graco’s lubrication experts can take you through a series of questions to help you work out which solution is the best for your application. Fill out the form below and we'll be in touch.
Take a look at Graco’s leading automatic lubrication solutions
Things to consider when selecting the right automatic lubrication system:
- How many lube points are there?
- What kind of power source do I have?
- How long is the lube line run length?
- What type of lubrication material do I use oil or grease
- What kind of feedback do I want?
- Indoor or outdoor use?
5 Reasons Why You Need Automatic Lubrication
Protect your equipment and your employees by utilizing automatic lubrication to grease critical lube points.
Related Articles
The components of an automatic lubrication system
An automatic lubrication system consists of a pump with reservoir, a controller, metering devices, hose and fittings and accessories.
Graco’s leading automatic lubrication solutions: a brief overview
Graco provides a wide portfolio of complete automatic lubrication solutions for any application.
How to avoid grease contamination and clogged Zerk fittings on construction and mining equipment
Automatic lubrication systems prevent clogged grease fittings by dispensing accurate doses of lubricant during operation.