Automation and electrification lower reject rates and warranty claims
To avoid rejected parts and warranty claims, the paint mix room technician for a large cabinet maker had to check more than 30 stations, many times a day. A six-month, side-by-side trial showed the best way to get him back to other essential job duties.
Remote monitoring and control frees up paint technician time for other essential duties
CUSTOMER: Wood cabinetry manufacturer and finisher
GRACO EQUIPMENT: Intelligent Paint Kitchen
CHALLENGE: In the cabinet industry, a consistent finish can be everything. Inconsistent finishes frequently led to rejected parts and warranty claims at one large cabinet manufacturer. The problem was that the stain colour depends on how the material circulates. If it moves too fast or too slow, it will affect the final colour.
Because there are so many variables in their system that affect circulation speeds, the paint technician had to check cycle rates, agitator speeds, and fluid pressure on more than 30 stations, multiple times per day. This kept him from tending to his other job duties.
SOLUTION: They needed to circulate and agitate the material at the right speed in order to provide a higher quality, more consistent finish. The solution needed to free up the technician to fulfil all job duties, while still overseeing paint kitchen parameters.
They considered three options:
- A Binks paint supply and circulating pump solution with a custom configuration that seemed complicated to the company.
- A system put together by the customer’s engineering and IT that could alert them of parameter changes, but did not provide control from outside the paint room. This homemade solution seemed inexpensive. However, it was not serviceable, or even usable, if the designers were no longer working at the plant’s location.
- Graco’s Intelligent Paint Kitchen with an out-of-the box setup, all Graco standard parts, and a way to remotely monitor and control paint room pumps and tanks.
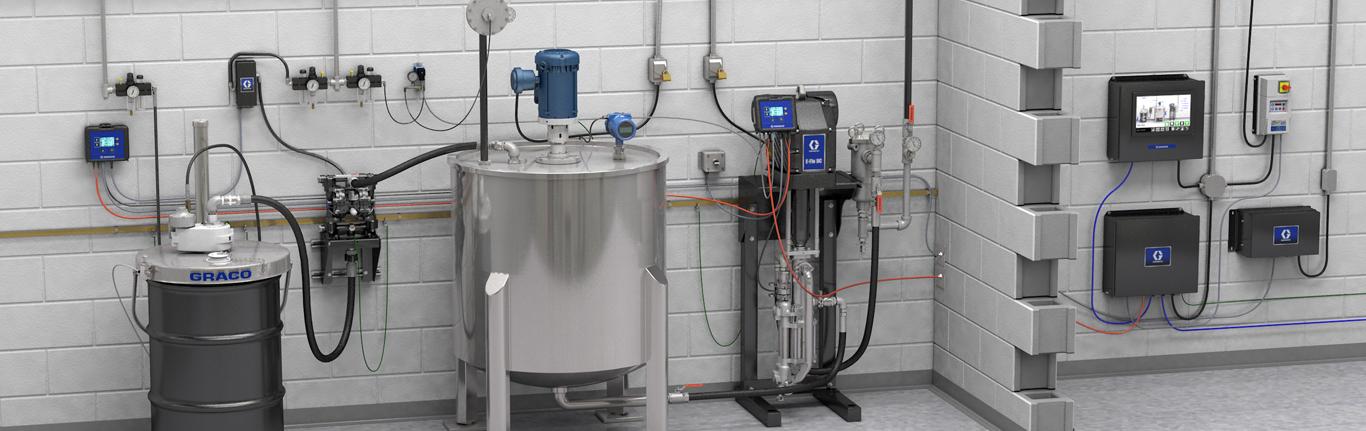
RESULT: They set up a side-by-side trial between the homemade the solution and one Intelligent Paint Kitchen unit that controlled an E-Flo DC electric pump, electric agitator, material level sensor. The Graco system quickly won over the cabinet manufacturer.
During the six-month trial, they lowered reject and warranty claims enough to justify the purchase of several more Intelligent Paint Kitchen units. The paint technician’s time was freed up immensely, allowing him to move forward with the rest of his job responsibilities.
Paint line employees can now oversee agitation, pump pressure, cycle rates, fluid PSI, flow rates and barrel levels from anywhere during the workday. All of this information is available at their fingertips with real-time notifications from the touchscreen control panel outside the paint booth, a mobile device, or email.
How to make your paint room Industry 4.0 ready
Make your paint mixing room Industry 4.0 ready by adding advanced control and interconnectivity.
Free webinar
How to integrate electric circulation pumps
Learn more about alternatives for advanced monitoring and controlling a paint mix room during a 60-minute webinar.
Related Articles
How to improve operator safety in the paint mixing room
Improving operator safety in the paint mixing room is key for any paint line owner.
How to make your paint room Industry 4.0 ready
Make your paint mixing room Industry 4.0 ready by adding advanced control and interconnectivity.
Wooden reel production facility installs an Automatic Paint Line
Learn how HES decided to invest in an automatic paint line for their wooden reel production units.