Pneumatic pump control and hybrid mode resolve shift change problems
Intelligent Paint Kitchen advances automation and quality for agricultural equipment manufacturer.
Manufacturer overcomes temperature changes, circulation balance and personnel issues
CUSTOMER: Agricultural equipment manufacturer
GRACO EQUIPMENT: Intelligent Paint Kitchen
CHALLENGE: An agricultural equipment manufacturer coated hay tool implements with a two component (2 K) urethane material. Although their equipment worked well, they struggled with paint mix room management.
Only the first shift maintenance technician knew how to mitigate issues. If these problems came up during second or third shift, they would go unaddressed:
- Empty paint drums would run dry and cause pump runaway.
- Overfilled supply tanks leaked paint all over the floor and took several hours to clean up.
- Throughout the day, 40 to 50 degree temperature fluctuations affected paint viscosity, throwing the circulation system out of balance.
This left them with two shifts of bad parts or no usable parts at all.
When the first shift maintenance technician came in, it took at least 30 minutes to fix problems from the other shifts and restart production.
SOLUTION: A webinar about Graco’s Intelligent Paint Kitchen sparked the manufacturing engineer’s interest enough to get a quote. At the time, the system managed only electric pumps. After investing in new pneumatic pumps, they could not justify the cost of converting to electric.
When the manufacturing engineer heard Graco was testing Intelligent Paint Kitchen control of pneumatic pumps, he was first in line.
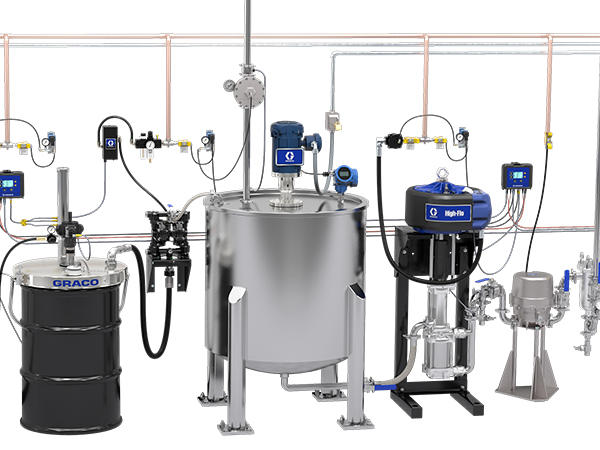
RESULT: The Intelligent Paint Kitchen works well with their High-Flo pumps with NXT 2200 air motors and 1000cc sealed 4-ball lowers. Oversight of pump metrics and tank levels from outside of the paint room mitigates many issues.
The Intelligent Paint Kitchen’s hybrid mode allowed them to program the knowledge of their first shift maintenance technician into the system.
- Flow and pressure rates were automatically adjusted to changing temperature and paint viscosity throughout the day.
- Pumps running colours not in use automatically slowed production to save on paint and pump wear
- Alerts provided real time troubleshooting on problems inside the paint kitchen.
Since Intelligent Paint Kitchen sensors, actuators and control modules were added to their pneumatic equipment, they have not needed adjustment. The agricultural equipment manufacturer has saved hours in downtime, cut down on numerous quality issues and thousands of headaches.
Free webinar
How to integrate electric circulation pumps
Learn more about alternatives for advanced monitoring and controlling a paint mix room during a 60-minute webinar.
Contact an expert
Related Articles
Intelligent control improves productivity for a Tier 1 supplier
Paint technicians are happier with more productive activities than manually monitoring an otherwise automated system.
5 most common paint mixing room challenges (and how to tackle them)
Paint mixing rooms enable a safe storing and mixing of paints, but also bring along some challenges.
Automation and electrification lower reject rates and warranty claims
To avoid rejected parts and warranty claims, the paint technician for a large cabinet maker had to check more than 30 stations, many times a day. A six-month, side-by-side trial showed the best way to get him back to other job essentials.