What determines transfer efficiency of automated paint systems and how to improve it
Understanding the importance of the transfer efficiency of automated paint strategies, and what affects it.
Transfer efficiency is critical to the spray finishing industry, from both a cost and a regulatory standpoint. Although transfer efficiency is a relatively simple concept, it can lead to considerable confusion if it is not clearly understood. Knowing what influences transfer efficiency is important to enable the most efficient automated spray paint solution.
Understanding the influences of transfer efficiency and how it is used in the industry is important for factory owners. By exploiting transfer efficiency, manufacturers can save money and reduce maintenance and VOC emissions.
WHAT IS TRANSFER EFFICIENCY?
When spraying an object, there is always a part of the sprayed material that is sprayed around the object. The term transfer efficiency refers to the amount of paint that is sprayed on the object compared to how much material is dispersed from the spray gun(s). Transfer efficiency is expressed as a percentage. A 60% transfer efficiency means that 60% of the material sprayed actually reached the target. The balance of 40% was lost to the spray booth or other areas during the spray finishing process.
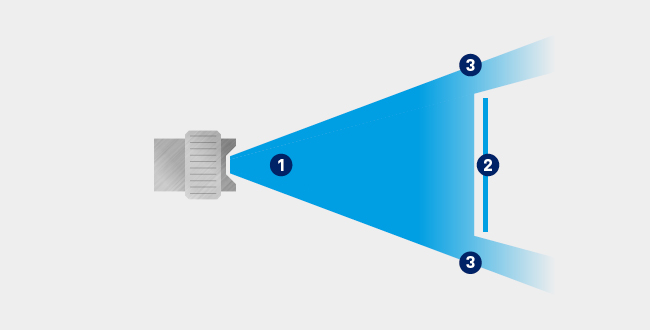
Transfer efficiency = amount on target vs amount sprayed
(1) Fluid (2) Surface (3) Overspray
Why is transfer efficiency important?
By increasing transfer efficiency, we reduce paint loss. This leads to a reduction in released VOCs and improves the life of your mixing room filters. Transfer efficiency can be increased as a result of using different spray applicators. By maximising transfer efficiency and spraying less paint, manufacturers can save money, reduce maintenance and lower both filter costs and VOC emissions.
What determines transfer efficiency?
The biggest factor in achieving high transfer efficiency is choosing the right spray gun. Selecting the most efficient spray gun for the intended application is important in optimising the efficiency of your spray operation. Conventional air spray, compliant, HVLP, air-assist, electrostatic and rotary atomiser all offer excellent benefits depending on the application.
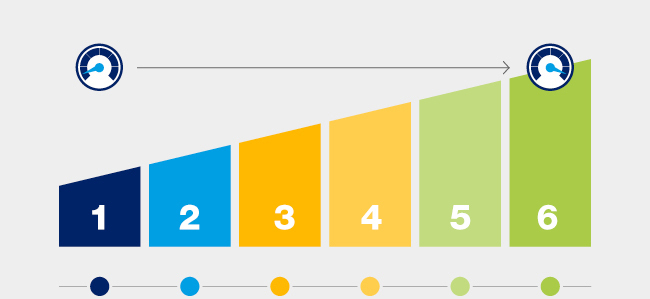
Transfer efficiency
- Conventional
- HVLP
- Airless
- Air-Assisted
- Electrostatic
- Rotary
Overall, there are advantages and disadvantages to each spray technology. Determining the highest requirement for your production line will assist you in identifying which spray technology will fit your application. Other factors can impact transfer efficiency too, such as operator techniques, a proper gun set-up, spray pattern height, grounding and air conditions in the mixing room.
Transfer efficiency & electrostatics
If you are looking for a spraying solution for waterborne materials that provides high transfer efficiency and high-quality results, be sure to check out the HydroShieldTM system. The system works with professional Pro Xp WB electrostatic guns combined with a variety of nozzles and other equipment providing excellent transfer efficiency for a wide range of high- and low-pressure applications.
As portrayed by the above graph, rotary bell atomizers, such as Graco’s ProBell® series, will provide the best possible transfer efficiency rates for automated paint systems. In combination with electrostatics they can achieve a transfer efficiency as high as 95%!
Related Articles
Lift your spraying precision to another level with the ProBell Rotary Atomiser
Discover the many benefits of Graco’s ProBell Rotary Applicator series for automatic painting applications.
3 tips for limiting paint overspray of electrostatic spray guns
Limiting paint overspray of electrostatic spray guns increases cost-efficiency and reduces VOC emissions.
How to achieve the best results with electrostatic spray painting guns
5 simple steps to get the best finish quality and transfer efficiency with electrostatic sprayers.