Sucker Rod Maintenance
An Introduction to Sucker Rod Pumps & Related Maintenance Operations
The Basics of Sucker Rod Pumps
Sucker rod pumps are commonly utilized in the oil and gas industry to extract fluids from wells. This process, also known as beam pumping, uses a mechanical device - the sucker rod pump. This pump is comprised of three main components: the pump itself, the rod string, and the surface drive, all of which play vital roles in the operation of the pump.
The submerged pump lifts the fluid, while the rod string connects the pump to the surface drive, which powers the pump. The rotation of the surface drive prompts the rod string to move up and down, triggering a plunger within the pump to create a low-pressure zone. This allows the fluid to flow into the pump, and the upward movement of the rod string forces the fluid out of the pump and up to the surface.
The sucker rod pump is praised for its simplicity, versatility, and ease of use, making it a cost-effective solution for many pumpers in oil fields. It can handle a wide range of fluid viscosities and well conditions and can be easily adjusted to optimize production rates and adapt to changing reservoir conditions.
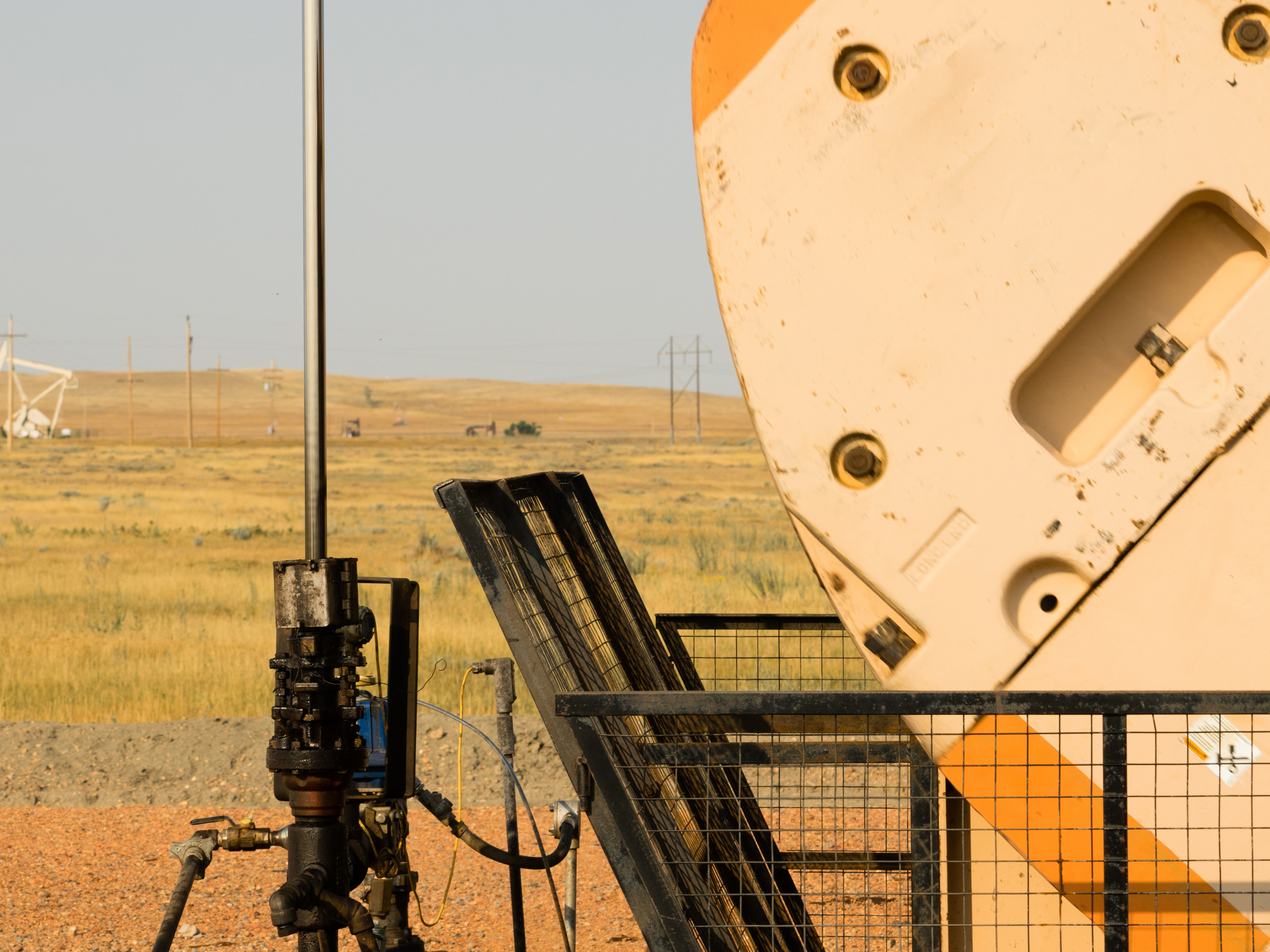
The Components of a Sucker Rod Pumping System
To extract oil and gas efficiently from wells using a sucker rod pumping system, a solid understanding of the different components and their functions is essential.
The primary components of a sucker rod pumping system include the pump, the sucker rods, the couplings, the polished rod, and the tubing. The pump is responsible for creating the necessary pressure to lift the fluid from the well. The sucker rods transmit the reciprocating motion from the surface to the pump, providing the required mechanical energy. The couplings ensure a continuous transfer of motion by connecting the sucker rods. The polished rod acts as an extension of the sucker rods, enabling the transmission of motion to the pump.
Various types of rods are used in sucker rod pumping systems, including steel rods and fiberglass rods. Steel rods are favored for their strength and durability, while fiberglass rods offer benefits such as corrosion resistance and lighter weight.
The coupling maintains the integrity and strength of the sucker rod string by ensuring that the sucker rods are securely connected. The polished rod, or the walking beam rod, is a crucial link between the surface unit and the pump. It converts the reciprocating motion of the surface unit into a vertical motion, enabling the pump to lift the fluid from the well.
The Role of Sucker Rod Pumps in the Oil and Gas Industry
Sucker rod pumps play a crucial role in the oil and gas industry. They provide an efficient and reliable method for extracting fluids from wells. Used in various applications across the industry, these pumps offer numerous benefits and incorporate the latest advancements in design.
Sucker rod pumps are primarily used in artificial lift systems to raise the pressure in the wellbore for efficient extraction of oil or gas. Suitable for wells with low to moderate flow rates, these pumps can handle a wide range of fluid viscosities and are used in both conventional and unconventional oil and gas production.
The benefits of using sucker rod pumping technology are significant. These pumps are known for their simplicity, reliability, and low maintenance requirements. They can operate efficiently in various well conditions, including deviated or horizontal wells. Furthermore, they offer excellent control over the production rate, allowing for optimization based on specific well characteristics. Additionally, they are cost-effective, making them an attractive option for many operators in the oil and gas industry.
As technology evolves, so does the design of sucker rod pumps. The latest advancements focus on enhancing performance, durability, and efficiency. Innovations in materials, such as the use of composite materials for rods, improve strength while reducing corrosion and wear. Improved sealing systems and better pump geometries contribute to higher efficiency and increased production rates.
At Graco, we understand the importance of sucker rod pumps in the oil and gas industry. Our range of high-quality lubrication pumps meets the demanding requirements of mechanical lift operations, ensuring reliable system performance. With our commitment to innovation and customer satisfaction, we strive to provide cutting-edge lubrication solutions that optimize production and reduce operational costs across the oil and gas market.
.png)
Recognizing and Resolving Common Failures in Sucker Rod Pumps
Like any mechanical equipment, sucker rod pumps can experience failures that may disrupt operations and result in costly downtime. It is crucial to understand common failures, diagnose pump issues, and implement effective mitigation strategies to maintain optimal pump performance.
Common failures in sucker rod pumps include rod parting, tubing wear, pump barrel damage, and valve failures. Regular inspections and monitoring can help identify these failures at an early stage.
Diagnosing pump issues involves visual inspections, data analysis, and the use of diagnostic tools. Visual inspections can identify visible signs of wear, leaks, or misalignment. Data analysis involves monitoring pump parameters such as pressure, temperature, and flow rates to identify abnormal patterns or deviations. Diagnostic tools like dynamometers and acoustic sensors provide detailed information about pump performance and potential issues.
Effective strategies for mitigating pump failures include regular maintenance, routine servicing, and proactive measures. Regular maintenance involves cleaning, lubricating, and inspecting the pump components. Routine servicing includes replacing worn parts, repairing leaks, and addressing any identified issues promptly. Proactive measures may include preventive maintenance schedules, operator training on proper pump operation, and the use of advanced technologies like condition monitoring systems to detect early signs of failure.
At Graco, we understand the significance of reliable sucker rod pump performance for your operations. Our range of high-quality pump products and solutions enhance efficiency, durability, and productivity. With our expertise and innovative technologies, we can help you mitigate common failures and optimize the performance of your sucker rod pumps. Reach out to us today to learn more about our pump offerings and how we can support your pumping needs.
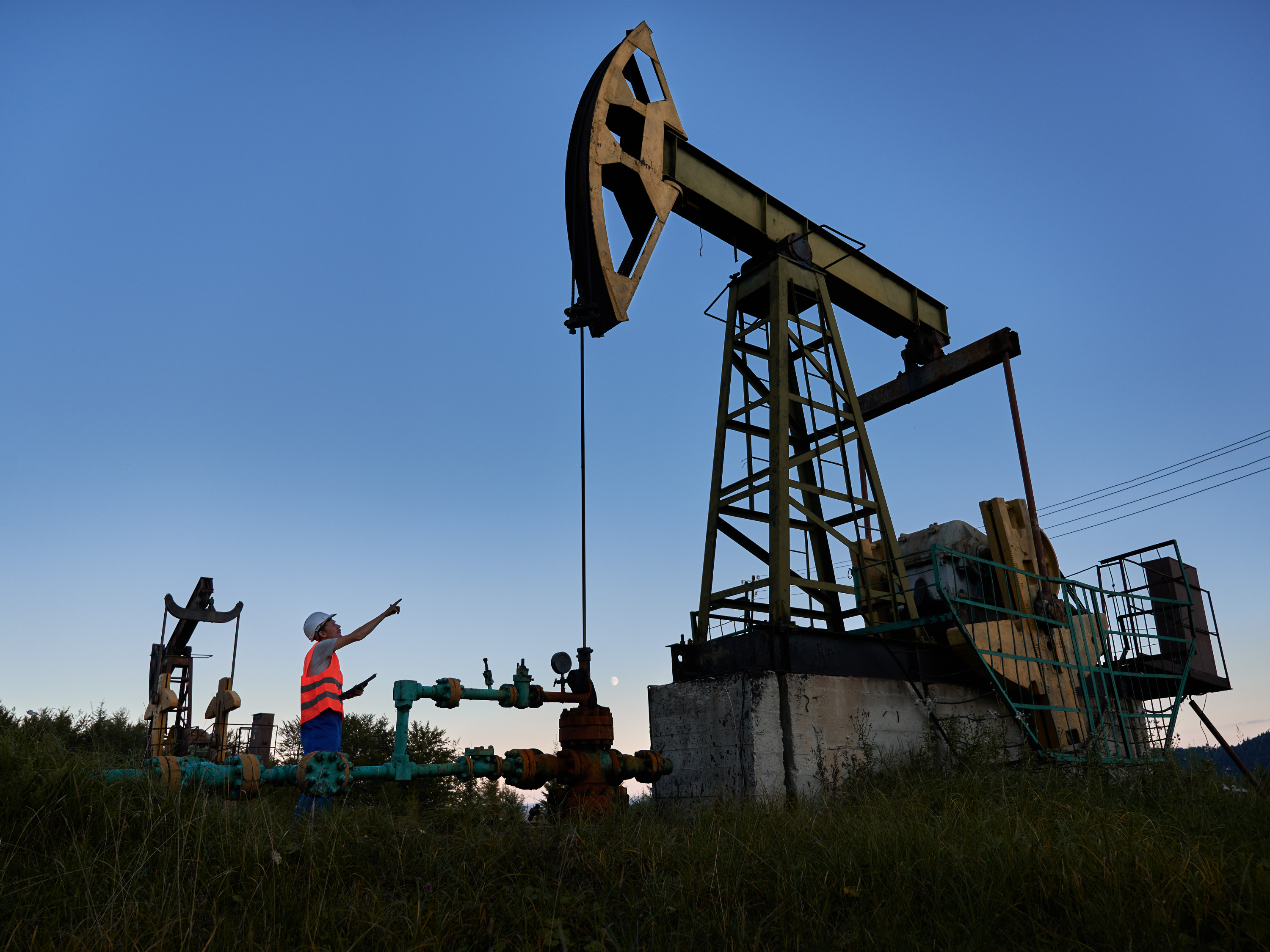
Maintaining and Optimizing Sucker Rod Pumping Systems
Proper maintenance practices are essential for extending the life of your sucker rod pumping system and ensuring optimal performance.
Regular inspection of pump components to check for signs of wear, leaks, or corrosion is crucial. Damaged parts should be replaced immediately to prevent further damage to the system. Regular lubrication of the pump reduces friction and prolongs the life of the components.
.png)
Many of the deeper system malfunctions for sucker rod pumps occur by improper condition maintenance of surface components. The polished rod's motion is directly linked to the downhole pump. Issues at the surface like misalignment or excessive vibration can transmit down the rod string, leading to accelerated wear or failure of downhole components.
Graco has developed a pump-to-point automatic lubrication solution specifically to maintain the packings of the polished rod stuffing box and resolve those issues that result in operational inefficiencies and breakdowns. Automatic lubrication, opposed to manual oiling or beam pump operated lubricators, is designed to provide optimized lubrication for machinery that extends component life while leaving out room for error.
A poorly maintained stuffing box can fail to seal properly, leading to fluid leaks. This not only poses environmental risks but also reduces the operational efficiency of the pump. Leaks can introduce contaminants into the system, which may clog or damage internal components. Excessive friction can cause an exhaustive list of issues that range from component replacements to full system inoperability.
G3 Technology
Experience Total Cost of Maintenance Reduction with Automatic lubrication for Rod Pimp Stuffing Boxes
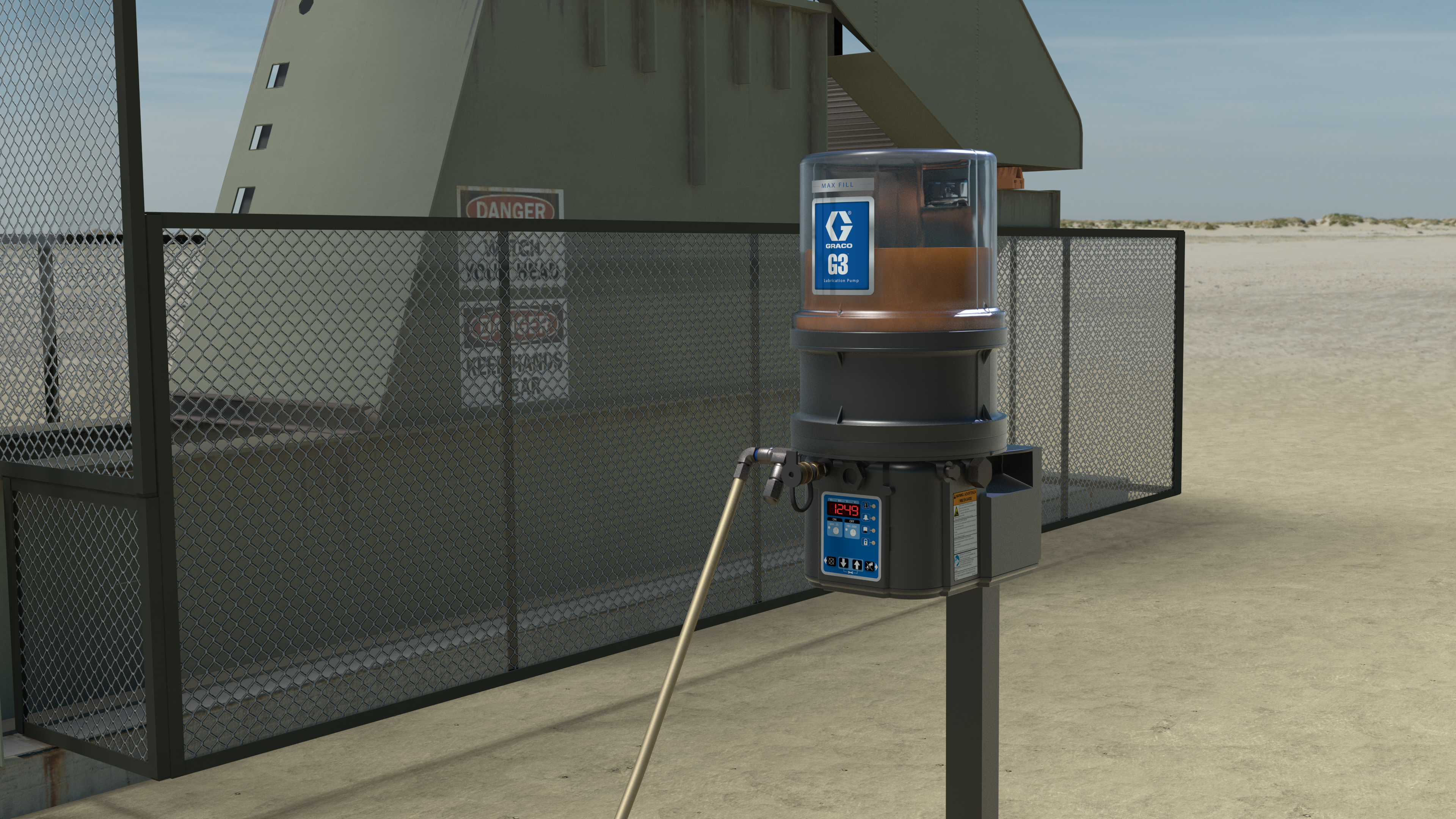
G3 TECHNOLOGY
Experience Total Cost of Maintenance Reduction with Automatic lubrication for Rod Pimp Stuffing Boxes