Cleaning Polyurethane Foam On Concrete
Tough Polyurethane Stains: Vapour Abrasive Blasting Does The Trick
As a field representative for a manufacturer of pressurised surface cleaning equipment, I often encounter challenging clean-up situations on concrete and brick surfaces. One of the more stubborn materials is polyurethane foam, which has gained wide acceptance as an insulation and concrete-repair solution. The high-density foam expands to fill voids and lift sunken concrete, but when spilled onto unintended areas, it can be particularly challenging to remove. Its chemical properties make it difficult to scrape, sand, or remove with chemicals and its brownish colour does not generally blend well with concrete surfaces.
Using Graco’s EcoQuip 2 Vapour Abrasive® blasting equipment, I’ve found a highly effective solution to handling polyurethane foam spills. Vapour Abrasive blasting systems combine water and abrasive media in a pot under pressure, then inject the mixture into an air stream, providing a precisely controlled system to treat stains resistant to other measures. Because the water is pressurised instead of air, as with wet or dry blasting systems, the operator can set the blast pressure to approximately 2.75 bar (40 psi) and remove stains without damaging the concrete substrate. Vapour Abrasive blasting also uses little water, hence the name vapour, which avoids slurry messes that accompany wet blasting operations.
On a recent demonstration project in Panama City, Florida, polyurethane foam had leaked onto a concrete pad over a 1.22 metre by 6.1 metre (4-by-20-foot) area at SprayPolyParts, a distributor of spray foam equipment and products. Removal by other methods had proven ineffective. Using a Graco EcoQuip 2 EQp, we removed the stains in less than an hour with vapour blasting.
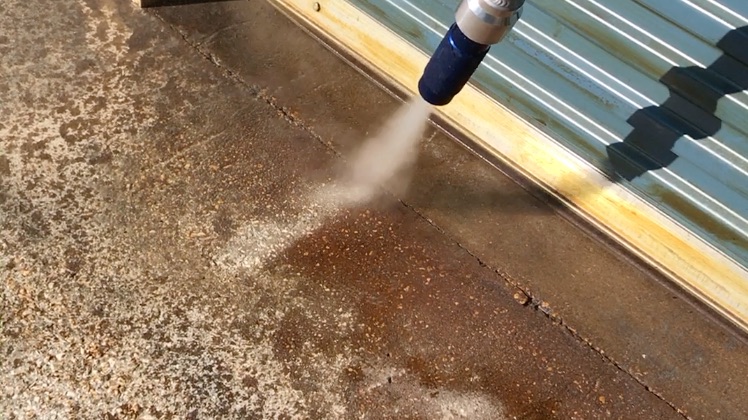
Before abrasive blasting
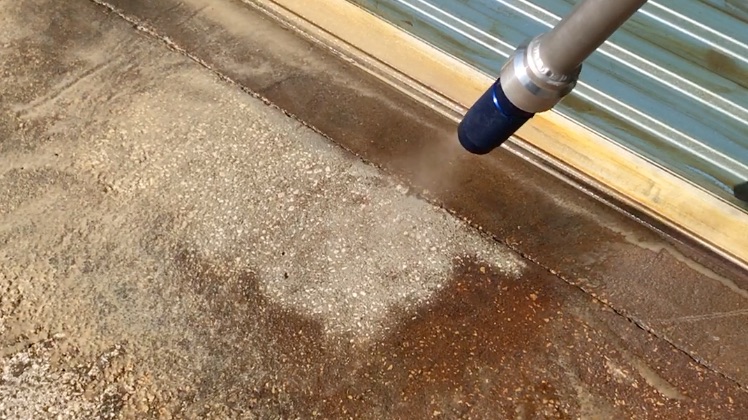
After abrasive blasting
Type of Abrasive Media Used
On this project, we used a 40/70 crushed glass abrasive with approximately 27.2 kg (60 pounds) of media. The 40/70 represents a blended grit size, with a combination of coarse and fine crushed glass. As a demonstration, I treated a small area, then handed the blast hose to the owner of the company who had no experience in abrasive blasting, but he completed the pad with ease.
The abrasive media residual required no special clean-up, as crushed glass is a non-toxic material. Because a gravel area surrounded the concrete pad, the residual could simply be washed into the adjacent gravel. The crushed glass media has a sand-like texture and does not contain sharp shards of glass.
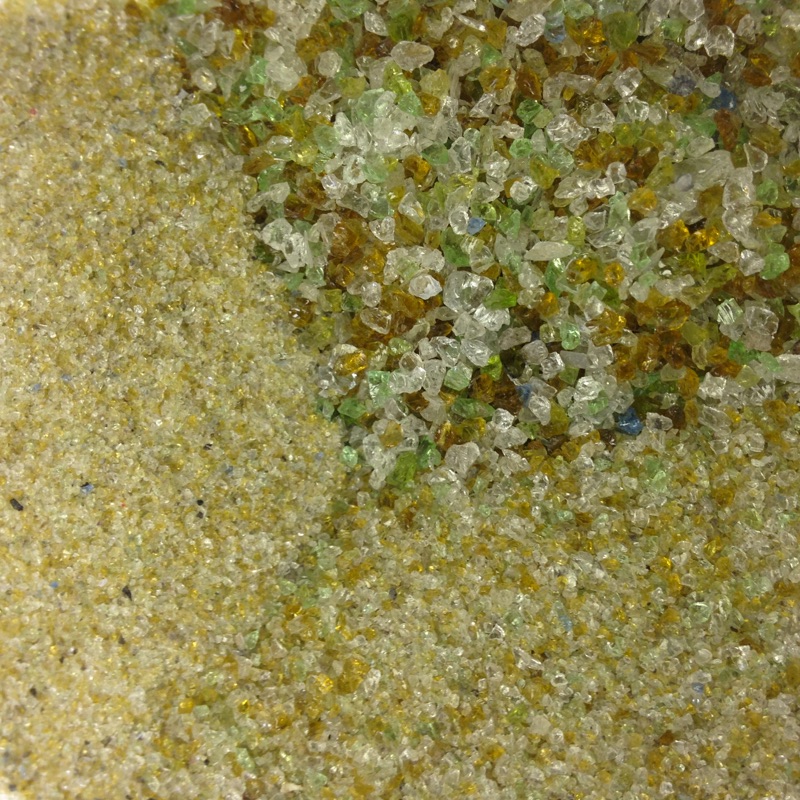
Beyond Cleaning Polyurethane Stains
Vapour Abrasive blasting can address a variety of removal and restoration situations. For example, on bridges and parking ramps, Vapour Abrasive blasting can remove paint and coatings without damaging the substrate. A wide range of pressures and abrasive media can be used, providing flexibility for numerous applications. The adjustable settings also improve efficiency. Traditional wet blasting equipment is typically on or off, which can decrease production and over-use water and media. Vapour Abrasive blasting uses such little water that often no containment is necessary. Remaining particles and residue can be swept up, leaving virtually no sign of the spill and treatment process.
Although thorough cleaning and minimal dust generation make Vapour Abrasive blasting a natural fit for cleaning up polyurethane foam spills, the Vapour Abrasive blasting equipment has many other uses that make it beneficial to cleaning, prepping surfaces and removing coatings and stains. The environmental and efficiency gains make it an attractive option to public and private agencies facing a wide variety of tough clean-up tasks.
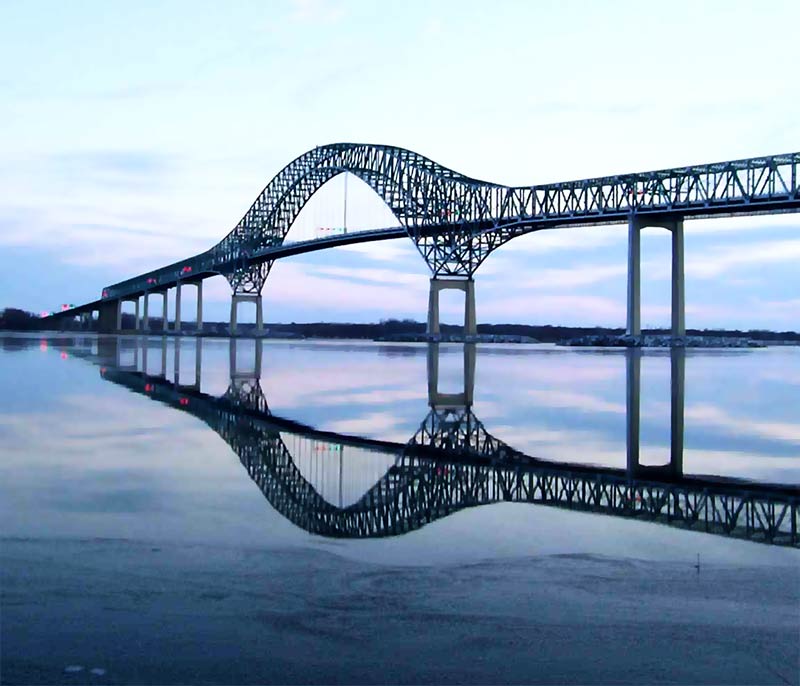
Related articles
Silica Dust and Wet Abrasive Blasting
Innovation in abrasive blasting technology being driven by the need to control silica dust
How to Prevent Flash Rust When Wet Blasting
As wet cleaning methods have increased, so has the prevalence of flash rust and the need to prevent it - here are a few tips.
How to Choose the Right Blast Nozzle for Wet Abrasive Blasting
What you need to know to choose the right nozzle for your abrasive blasting application