Gear Pumps vs. Piston Pumps
Which is More Accurate?
Both gear pump and piston pump technology are used in spray foam and polyurea spray equipment. Which of these is the ideal pump technology to handle the challenging spray parameters and conditions inherent in spraying foam and polyurea? To understand the answer to that question, it helps to first understand the how each of these pumps work.
How Gear Pumps Work
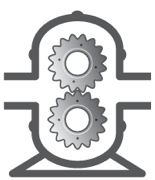
A gear pump is a type of positive displacement pump. Gear pumps move fluid repeatedly, enclosing a fixed volume using interlocking gears and transferring the fluid mechanically using a cyclic pumping action. Gear pumps are nothing new and have been around for hundreds of years.
How Piston Pumps Work
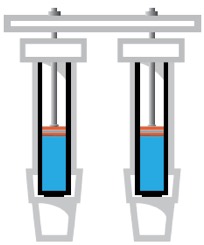
Piston pumps are positive-displacement pumps that use a piston and plunger to displace and pressurise fluids. Either single or double-acting, piston pumps operate by using the force of the pumping mechanism to expand and contract an internal movable volume of liquid.
Video: Gear vs. Piston Pumps
Side by Side Comparison
When doing a side by side comparison of gear pumps versus piston pumps, it’s easy to see which one is more accurate and has everything you need for successfully applying spray foam and polyurea:
Qualities of a Good Pump | Gear Pump | Piston Pump |
Accurate, repeatable dispensing with every stroke or cycle | ![]() | ![]() |
Independently maintains ratio in plural component applications | ![]() | ![]() |
Handles a large variability of ambient conditions | ![]() | ![]() |
Handles a wide range of material viscosities | ![]() | ![]() |
Handles varying triggering patterns and speeds | ![]() | ![]() |
Handles the effects of isocyantes (gumming, crystallising, hardening) | ![]() | ![]() |
Holds static pressure when not triggering | ![]() | ![]() |
Provides long-term reliability and minimal downtime for the user | ![]() | ![]() |
Easy to service at a reasonable cost | ![]() | ![]() |
The Downfall of Gear Pumps
Although gear pumps may be capable of dispensing materials, when selecting a pump for two-component isocyanate, users should understand there are risks, costs and other potential issues inherent to gear pumps. The biggest risk is built on the assumption that the flow meters used in gear pump systems are accurate and will remain accurate.
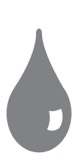
1. Leakage
Fluid leakage results from the imperfect fit between components in a gear pump assembly. Regardless of how well the two components conform to one another, gaps will exist and fluids will move through them. Clearances at the gears and across the faces of gears are the largest contributors to internal leakage. Fluid leakage increases as the internal parts wear through usage.
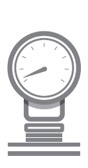
2. Stall Pressure
Due to internal fluid leakage, stall pressure cannot be maintained and ratio cannot be accounted for without being dependent on flow meters.
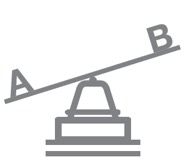
3. Ratio Imbalance
Being unable to maintain stall pressure leads to ratio overshoots and undershoots as the flow is corrected to compensate for fluid leakage.
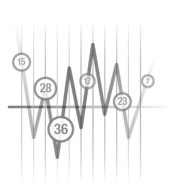
4. Recalibration
Depending upon flow meters will require field calibration of the meters to maintain accuracy. Calibration is necessary to account for changes in materials, viscosities, flow rates, ambient conditions and equipment wear due to usage. If flow meters are not recalibrated, the system may not know the true ratio.
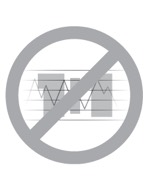
5. False Ratio
If the flow meters are not accurate, the ratio will not be accurate. However, the system will still report and display perfect accuracy and that the material is on-ratio, even if spraying off-ratio product.
Contact an Expert
Related articles
Spray Foam Rigs - What You Need to Know
What size generator will you need? Which style trailer is best? What about safety equipment? Get answers.
How to Bid Spray Foam Jobs
Bidding spray foam jobs is more than just price per square foot. Learn about understanding your competition, avoiding discounts, protecting profits and more.