Reducing SLU Scheduling Issues
Installing Self-Levelling Underlay Faster and More Efficiently
Introduction
With ever-growing pressures to complete buildings on tight schedules, flooring and subflooring contractors often feel pinched from multiple sources. Modern flooring materials such as tiling and the associated adhesives are advancing to dry faster than before, and various construction trades demand access to rooms sooner.
Owners, designers and general contractors demand high quality, along with rapid installation. For contractors installing self-levelling underlay (SLU), this means new approaches are needed to complete work faster and more efficiently. Pumping of SLU can help address these challenges.
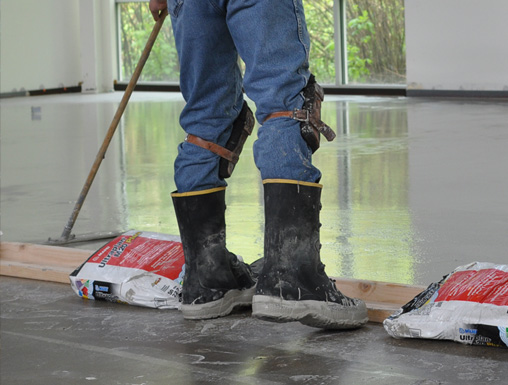
A New Approach
With SLU pumping, scheduling challenges can be greatly reduced. Placement can generally be completed faster with fewer people. Since larger rooms do not necessarily require additional workers, these resources can be applied elsewhere on the project or on other projects.
Time savings begin with the material mixing process. Using combined mixing and pumping units such as the Graco Toughtek MP20, water can be mixed automatically with cement-aggregate compounds in prescribed amounts. SLU mixtures can be pumped up to distances of 91 metres (300 feet) and heights of 18 metres (60 feet).
In addition to time savings and simplified batch placement, SLU pumping can simplify set-up and equipment transportation. The MP40 (a larger version of the MP20) is approximately 163 centimetres (64 inches) long, 81 centimetres (32 inches) wide and 135 centimetres (53 inches) tall, so it can typically be loaded and transported in a standard ute. With built-in wheels, it can be transported around a job site easily.
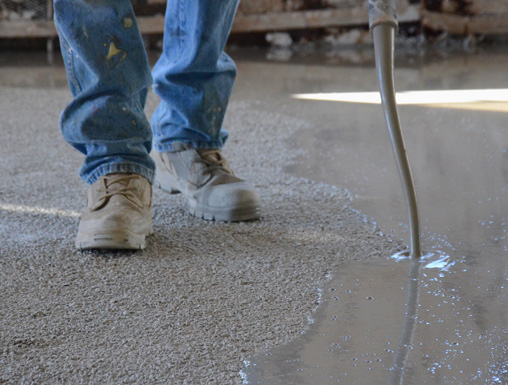
Simplified, continuous placement of SLU
Coordination of batch placement is another challenge greatly simplified with pumped SLU. Instead of manually placing batches that must be matched and tied together, pumped SLU can be placed in a more continuous manner, with multiple passes made in a zig-zag pattern, as shown in Figure 3. This enables workers to place SLU in widths of just a few centimetres at a time, or several metres at a time, while maintaining a “wet edge” and more continuity in the SLU layer.
In addition to time savings and simplified batch placement, SLU pumping can simplify set-up and equipment transportation. The MP40 (a larger version of the MP20) is approximately 163 centimetres (64 inches) long, 81 centimetres (32 inches) wide and 135 centimetres (53 inches) tall, so it can typically be loaded and transported in a standard ute. With built-in wheels, it can be transported around a job site easily.
The automated approach also improves mix consistency and placement precision. With water flow rates set according to manufacturer’s recommendations, compound materials and water can be mixed within the mixing chamber at the same rate all day long. The units can be used to correct uneven floors, repair damaged concrete and provide a smooth surface for carpet, tile or other floor covering.
While skilled workers are still needed to place SLU, skill sets from other crafts are often transferable. Crews that can place stucco can generally place SLU. Daily profits can be substantially higher when pumping SLU, when compared to pumping other types of mortar products. Some examples clarify how this works.
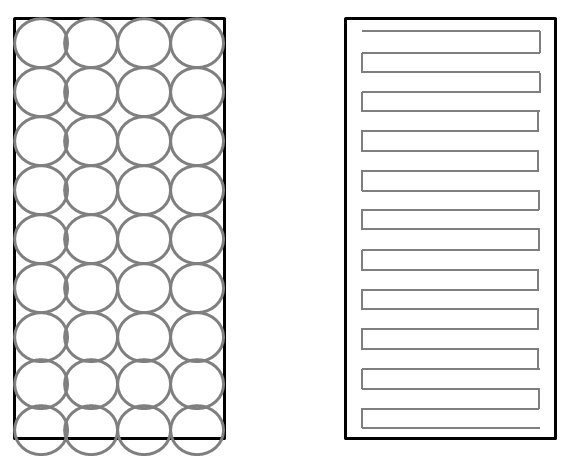
Rendering vs SLU Pumping
Consider a typical day of pumping stucco versus a typical day of pumping an SLU overlay. Assuming an 8-hour day, the cost breakdown might look something like this:
Rendering (418 m2 (500 Square Yards), 12.7 mm (1/2-Inch) Base Coat)
Labour: 6 workers x 8 hrs @ $40/hr = $1,920
Materials: 418 m2 (500 sq yds)/2.5 m2 (3 sq yds)/bag x $6.20/bag = $1,033
Subtotal = $2,953
40% overhead & profit = $1,181
SLU (1510 m2 (16,250 Square Feet), 6.35 mm (1/4-Inch) Overlay)
Labour: 6 workers x 8 hrs @ $40.00/hr $1,920
Materials: 6.5 hrs x 100 bags/hr x $20.00/bag = $13,000
Subtotal: $14920
40% overhead & profit = $5,968
In the above scenario, the potential gross profit for a given day of pumping SLU is five times that of the same day pumping rendering. This is a very conservative estimate, as some mixing pumps can mix and place 200 bags per hour.
SLU Pumping vs Manual Placement
As another example, assume two crews of six persons each, with one crew pumping SLU and the other placing SLU manually. The individual roles might be as follows:
Mixing Pump
- 2 people taking turns breaking sacks into mixing pump hopper
- 1 person managing excess hose as the room is poured from the furthest point
- 1 person holding the end of the hose controlling placement of mixed material
- 1 person on gauge rake
- 1 person with smoother trowel
Hippo Drill/Barrel Mixers (2 Mixing Units)
- 4 people for breaking bags, adding water, mixing and wheeling mixed material into place
- 1 person on gauge rake
- 1 person with smoother trowel
The pumping crew can mix and place approximately 200 sacks per hour. This equates to 1300 sacks, or 3019 m2 (32,500 square feet) at 6.35 mm (¼-inch) thickness, for an average day of 6.5 hours of actual pumping.
The manual crew, at an average of five bags in 7 minutes per barrel, can mix and place 90 sacks per hour. This equates to 585 sacks, or 1325 m2 (14,265 square feet) at 6.35 mm (¼-inch) thickness for the same 6.5 hours of pumping.
Based on these parameters, a pumping crew can apply more than twice the square footage in a given day. This is accomplished while working at a smooth constant pace, placing consistently mixed material and not overworking personnel. Assuming a mark-up for SLU toppings of $.50 per square foot and a typical eight-hour day (6.5 mixing hours), this can equate to nearly $10,000 per day in added profits.
Related articles
Spraying Techniques for Electrostatic Airless Disinfectant Sprayers
Learn more about the power of high-pressure electrostatic airless sprayers and maximising efficiencies when spraying disinfectants.
Spraying Techniques for Airless Disinfectant Sprayers
Using a dedicated airless disinfectant sprayer provides the fastest way to achieve consistent coverage of disinfectant materials across any surface being sprayed.
Spraying Techniques
Understanding and applying these basic spraying techniques will be the difference between a sloppy looking paint job and a professional one.