Don’t Let Grease Guns Get In the Way of Improving Your Productivity
Heavy equipment operators have alternatives when it comes to manually greasing machines
Heavy equipment owners and operators understand the critical role grease plays in preventative maintenance programs. Daily grease practices can be overlooked, especially when you’re relying on an operator to hit up to 50 grease points with a grease gun. On the surface, manual grease guns and tubes of moly or synthetic grease may seem like a cost-effective solution for equipment lubrication, but you must factor in some important considerations when deciding what’s right for you – operator inconsistencies and machine downtime.
The trouble with grease guns
Grease guns have been the go-to greasing tool for heavy equipment for years. But like most technologies, there are innovative solutions introduced. Manual hand pump grease guns made way to battery operated grease guns, reducing operator fatigue and shortening the time it takes to grease a piece of equipment. However, battery operated grease guns still require considerable time to grease a machine, and some of the same problems found in hand pump grease guns remain present in battery powered counterparts such as over greasing, under greasing, difficulties with couplers attaching to grease fittings and safety concerns with lube points near high heat or hard to reach locations.
The benefits of auto greasing heavy equipment
Automatic lubrication not only changes the way we grease our equipment, but also eliminates many of the issues surrounding manual lubrication with grease guns.
Automatic lubrication saves roughly an hour of equipment greasing per machine each day. As production demands continue to grow, the traditional method of dedicating an hour to greasing often results in shortcuts like skipping difficult grease points. During the most demanding times the entire hour may be completely neglected.
Automatic lubrication systems apply calculated amounts of grease to every fitting, meaning no more arbitrary amounts of grease being applied to every lube point. Manual greasing is based solely on the person operating the grease gun; when grease begins oozing out of the fitting this is the sign that the fitting doesn’t take any more grease. However, overflowing grease may also be caused by a poor fitting connection or dirt in the grease fitting causing a clog. Without proper diagnoses, the lube point may not be getting the adequate amount of grease.
Automatic lubrication reduces safety risks found in manual grease practices. Changing weather conditions, hard to reach grease locations, and hands carrying grease guns all play into potential safety risk associated with greasing equipment – like slips and falls, burns and other work related injuries.
The unique properties of grease in auto lube systems
If you’ve used a grease gun, undoubtedly you’ve greased with NLGI #2 or #1. One of the primary reasons that manual greasing calls for heavier, or NLGI #2 grease is because the heavier or the “stickiness” of the grease is often perceived as higher quality grease. But with auto lube, grease properties are unique.
NLGI grease ratings for auto lube systems are as low as #0 to #00. Systems pump smaller amounts of grease more frequently while the machine operates, ensuring a constant flow of grease that lubricates entire pins, so heavier grease is not needed.
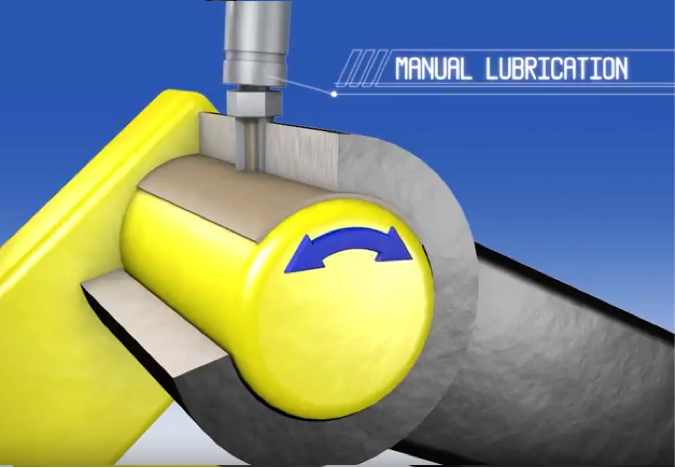
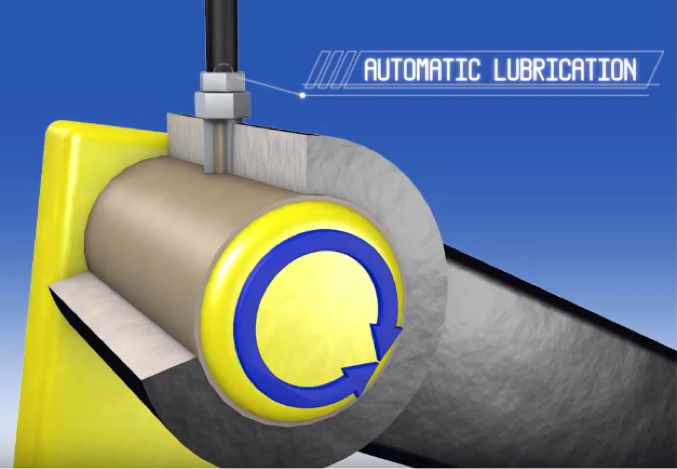
Auto greasing increases lifetime equipment productivity and profitability
Although the initial investment for auto lube may seem substantial, the ROI from automatic lubrication can be quick. It's not uncommon for break-even costs to be less than a year on a machine operating daily.
ROI is calculated by not only the downtime caused by manual greasing, but by component failures resulting from inadequate greasing practices. Take the typical costs of downtime and repairs and balance it with the cost of the auto lube system to discover the break-even cost.
Costs range for auto greasing systems on heavy equipment – with installation costs dictated heavily by the amount of grease line routing and protection required. For machines that have grease points in open areas the grease lines need to be well protected from the daily rigor of operation. Equipment costs depend on pump size and the number of grease fittings that require lubrication. For heavy equipment with many grease fittings the cost of the system is dispersed, because much of the system cost is in the grease pump.
Learn more about Graco automatic greasing systems
The basic components of an automatic lubrication system are a metering device, pump, controller, tubing/hose, and fittings to connect to the grease points. Many accessories are also available to enhance or compliment the operation of a system. Graco offers complete automatic lubrication systems for several machines, including excavators, wheel loaders, mining trucks, ag tractors, combines, forestry equipment and more.