Diaphragm pumps vs centrifugal pumps - pros and cons
Understand the advantages and disadvantages of diaphragm pumps compared to centrifugal pumps, and their common industrial applications.
What is a centrifugal pump?
Centrifugal pumps are classified as a dynamic pump type that use centrifugal force to turn mechanical energy into hydraulic energy. They are by far the most commonly used pumps on the market because they are reasonably priced and offer a good price/performance ratio for high flow applications. However, centrifugal pumps have a number of limitations that make them less than ideal for a range of industrial and hygienic applications. Electric diaphragm pumps solve many of these common issues.
Disadvantages of centrifugal pumps
Centrifugal pumps have several disadvantages compared to diaphragm pumps. Graco’s QUANTM pump is an electric double diaphragm pump (EODD) that addresses many of these common disadvantages of centrifugal pumps.
- Narrow optimum operating range and efficiency point
Centrifugal pumps have a specific impeller diameter, which means they only operate at optimum efficiency at a specific flow. Possible flow ranges below or above this best efficiency point (BEP) are quite narrow. Not only does working outside the pre-set range significantly reduce the pump’s efficiency, but it also, eventually, leads to cavitation, vibration, impeller damage, suction and discharge recirculation, or reduced bearing and seal life requiring complete rebuilds of the whole unit. QUANTM electric diaphragm pumps are well suited to varying flow, pressure, and applications. They pose no risk to shear-sensitive liquids and can easily handle abrasives and solids. - Impact of changes in viscosity
Some liquids can vary in viscosity due to temperature, a chemical reaction or separation (varied layers or solids). The performance of a centrifugal pump is especially impacted when pumping more viscous liquids because of the increased resistance to flow as the impeller rotates. The volume pumped by a centrifugal pump depends on the head (back pressures) viscosity and the homogeneity of the material. If these values vary dynamically in a certain application, it is difficult to keep a centrifugal pump operating close to its best efficiency and also without prematurely wearing out the pump. - Damage caused by deadheading
When a discharge valve is closed or a line blockage occurs, it causes the fluid to recirculate in the pump, and pressure to continue to build up, resulting in an increase in motor temperatures. When a pump is run in a deadheaded condition for too long, the excess heat damages the expensive seals and reduces pump life. Without purchasing additional sensors and controllers, a centrifugal pump will continue to run until something fails. The extra cost of these additional sensors and controllers needs to be included in the total cost evaluation. - Not self-priming
Centrifugal pumps are not self-priming. For the pump to work properly, its casing must be filled with liquid before start-up. When the casing fills with vapours or gases, the pump impeller becomes gas-bound and incapable of pumping. To make sure the pump remains primed and does not become gas-bound, centrifugal pumps need to be installed below the fluid level from which the pump takes its suction. Alternatively, the pump can be primed by supplying liquid under pressure through another pump placed in the suction line. QUANTM pumps are self-priming and have excellent suction capabilities. - Unsuitable for abrasives and solids
Particularly in the chemical industry, selecting a centrifugal pump for pumping solids is quite a challenge since process owners need a pump that is not only compatible with the chemicals being processed but also capable of handling solids without choking the impeller and thus causing increased pump wear and potential blockages. The centrifugal pump types that are suited to this specific set of applications tend to have lower performance ranges and are more expensive. - Unsuitable for shear-sensitive liquids
High-speed systems, such as the centrifugal pump, tend to shear liquids which is why this technology is not the best choice for shear-sensitive liquids. - Unsuitable to run dry
A centrifugal pump cannot be allowed to run dry without causing damage to the system. The system needs to have resistance to dissipate the rotational speed of the impeller. The QUANTM electric diaphragm pump can run dry without causing any damage to the system thereby avoiding expensive repairs.
Common centrifugal pump applications
While centrifugal pumps are commonly used in various industries because of their efficiency with low viscosity materials and high flow rates, they may not always be the best fit for every application. Here is a look at how centrifugal pumps are used in specific industries and QUANTM’s potential advantages:
- Food and beverage manufacturing
Centrifugal pumps are commonly used to transfer beverages and other low-viscosity liquids in the food industry. However, the forces generated by centrifugal pumps can sometimes damage sensitive fluids, altering their quality. QUANTM pumps are able to maintain the integrity of shear-sensitive products like creams and yogurts. Their hygienic design also ensures compliance with food safety standards. - Water treatment and transfer
Centrifugal pumps are often used for their ability to move large amounts of water, but they can struggle under varying pressure conditions and in the presence of solids. QUANTM pumps are able to handle a wider operating range, including higher solid content fluids without the risk of clogging. Their resistance to harsh conditions makes them an ideal alternative for water treatment applications.
Centrifugal pumps vs diaphragm pumps
Graco’s QUANTM electric diaphragm pump provides much more flexibility and reliability compared to centrifugal pumps. Take a look at the benefits:
Centrifugal pumps | Graco QUANTM EODD pumps |
Narrow best efficiency point and preferred operating range | Consistent reliability over the operating range |
Deadhead/stall causes severe damage | Easily manages a deadhead/stall with no additional equipment which prevents pump failures |
Process changes can lead to cavitation | No degradation due to changing conditions |
Difficult to choose the correct pump | Simple pump selection (pressure/flow/chemical composition) |
Shaft alignment is difficult to maintain | No spinning shaft seals; no alignment necessary |
Not self-priming | Excellent dry running/self-priming |
Special requirements for use in harsh environments | Can withstand harsh environments |
ROI calculator
Interested in going electric?
Answering three easy questions, calculate how much you could save by converting your facility to Graco electric double-diapragm pumps.
1) What industry are you in?
Based on your industry, we can set some default system requirements, like pump size, flow rate, and fluid pressure. Have you got a highly customised setup? Try our Advanced configurator.
2) How many pumps do you have?
We will estimate your savings based on the number and energy consumption of the pumps you already own.
3) What are your energy costs?
We will estimate your energy savings based on the average energy prices in your area.
Annual operational savings:
Check out our Advanced ROI calculator to learn how we calculated your savings.
Start again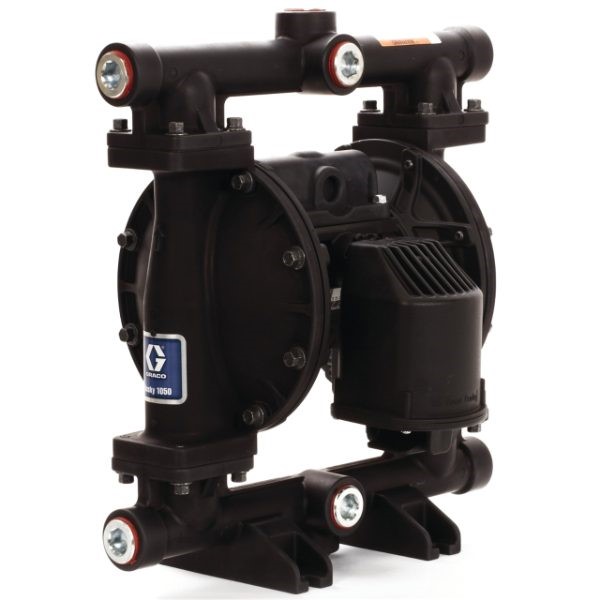

Related articles
The eleven benefits of an electric diaphragm pump
Understand the working principle of a diaphragm pump, the different types of diaphragm pumps, and the common uses and applications.
Electric diaphragm (EODD) pumps vs other technologies: pros and cons
There are many different types of industrial pumps, including diaphragm pumps, gear pumps, peristaltic pumps, and more. See an overview of each.
Electric oil pumps lead the way to improve energy efficiency and sustainability goals
Electric pumps lead the way to energy efficiency and sustainability goals