Can my Husky AODD pump handle high-viscosity fluids?
When configuring an AODD pump the most frequently overlooked specification is fluid density.
Fluid density is an important factor to consider because diaphragm pumps utilize ball checks that rise and fall as pressure changes occur within the fluid chambers of the pump. Ball checks come in a whole range of metal and elastomer configurations. Each of these materials has a different weight, or specific gravity. Understanding how this weight relates to the fluid has an influence on the material specified.
If a low-viscosity fluid is being transferred, the weight of the ball is not of critical importance because the fluid is not restrictive during the ball seating process. Only to reduce noise, one should work with a soft seat and hard ball configuration or vice versa. A 30% slurry, on the other hand, has a higher viscosity and therefore requires a heavier ball to move through the slurry so the ball seats properly. If the ball is too light, it will hang up in the slurry and will not seat, leading to poor pump performance that includes viscosity issues and cavitation. A rule of thumb is the denser the fluid, the heavier the ball check. Neoprene, stainless steel and PTFE ball checks have the highest specific gravity, or weight, allowing ball checks to seat reliably through high-viscosity fluids.
However, this is only part of the answer. Also important is the piping system to which the pump is connected. For example, when considering using a 1-inch AODD pump to transfer high-viscosity fluid, three questions are relevant:
a) Can the pump draw fluid at the desired flow rate through the suction line?
An approximate answer can be found by comparing the pump’s dry-lift rating to the suction line loss. In other words, check whether the pump’s dry-lift capability exceeds the suction line loss at the desired flow rate. To determine if the pump can draw in the process fluid, it is necessary to calculate the suction line loss for the desired flow rate. Pipe diameter and flow rate impact line loss greatly. It is not uncommon to increase the diameter of the suction line to overcome suction line loss.
A typical 1-inch AODD may have dry lift capabilities of 4.6 m / 15 ft of water or 6.5 psi / 0.45 bar. In practical terms, this means the pump cannot operate in systems where suction line loss exceeds 6.5 psi / 0.45 bar. To meet the desired flow rate, the suction line diameter may have to be increased to 2 inches, which will reduce the suction line loss to within the operating capabilities of the AODD pump.
b) Can the pump overcome the system’s total dynamic head (TDH)?
If the air inlet pressure exceeds the system’s TDH, then fluid can be transferred in the pump system. For pump longevity, AODD users should strive to design systems that operate in the mid-range of the pump’s capabilities. To calculate the TDH of the entire system, both the total static head and the discharge frictional line loss must be determined. The frictional line loss due to a 1-inch line exceeds the maximum operating pressure of most AODD pumps (120 psi / 8.3 bar). It becomes necessary to increase the discharge line diameter to reduce the losses to a level within the range of the AODD pump. Increasing the discharge line diameter from 1 inch to 1½ inches reduces the discharge line loss from 135 psi / 9.3 bar to 24 psi / 1.66 bar; a comfortable level for AODD pumps.
c) To what degree should the pump be de-rated, given the operating conditions?
A theoretical approach would be to use correction curves for AODD pumps, which summarize the frictional losses that occur when viscous fluid pass through the pump. Viscosity correction curves de-rate the pump’s capacity for process fluids with higher viscosities.
The viscosity correction charts are simply a guideline and should not be taken as fact, because every application can produce a different outcome. Graco recommends taking a specific application into account and using the pressure loss calculator tool (found on the website). When using the calculator, you can show (theoretically/mathematically) how much flow you can achieve with the application.
How to read a viscosity correction chart
To determine the maximum flow rate for any viscosity: On the horizontal axis, find the viscosity of the fluid. Move straight up to the intersection of the curve. From that point, read across to the maximum flow on the vertical axis.
To adjust the performance chart for higher viscosity fluids: (The performance charts are based on the viscosity of water, 1 centipoise). First determine (A) the fluid flow for water using the Performance Chart. Then find (B) the maximum flow using the Viscosity Correction Chart. Next, choose (C) the maximum rated flow for the pump:
- Hytrel diaphragms 26.5 l/min (7 gallons/min)
- Teflon diaphragms 24.6 l/min (6.5 gallons/min)
The adjusted flow rate of the higher viscosity fluid is equal to: A x B/C
For example: A Teflon diaphragm pump operates at 40.6 psi / 2.8 bar (0.3 MPa) fluid pressure at 71.1 psi / 4.9 bar (0.5 MPa) incoming air pressure. What is the adjusted flow rate for a fluid with a viscosity of 600 centipoise?
13.25 l/min. x 3.8 l/min. / 24.6 l/min. = 2.04 l/min (0.54 gallons/min)
Graco’s Husky pumps
Specific Graco Husky AODD pumps are ideal for high-volume evacuation of high-viscosity fluids (up to 20,000 cps) such as liquid concentrates from holding vessels or repackaging of fluids from the original container to smaller receptacles.
For more information on Graco’s AODD pumps for high-viscosity applications, visit www.graco.com/husky or fill in the form below.
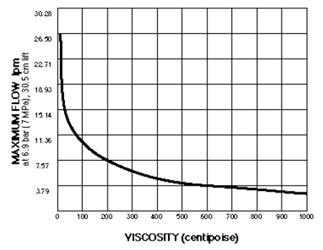
Typical viscosity correction curve
Husky Quick-Ship Service: get the Husky-pump you need when you need it
To help you avoid downtime, stay on schedule, respond to the unexpected and control costs in today’s challenging environment, the Husky Quick-Ship Service can meet your express needs.
Order your Husky-pump today and have it shipped tomorrow!
Related Articles
Troubleshooting some common problems with AODD pumps
Despite being highly robust and reliable, installation and operation problems can occur with air-operated double diaphragm (AODD) pumps. We look at some of the most common problems and how to fix them within minutes.
How to choose an AODD pump
A quick guide to selecting the correct AODD pump for your specific application