Dispensing silver epoxy with jet valves
Dispensing conductive adhesives — like silver epoxy — using jet valves requires high process accuracy and application flexibility. Non-contact jetting applications are commonly used to assemble microprocessors and other electrical parts that require unparalleled precision dispensing. These electrical components are manufactured to go into smartphones, computers, smartwatches, vehicles, batteries, medical devices, and scores of other products.
Silver epoxy is ideal for manufacturing these components because of the material’s high thermal resistance properties. The material contains actual silver flakes that when compacted generate high thermal and electrical conductivity.
Silver epoxy application challenges
In a typical die attach application involving semiconductor chip manufacturing, operators must secure the chip to a lead frame substrate (Figure 1). Silver epoxy is one type of die to attach adhesive that’s dispensed directly onto the die pad. The chip is then placed with some pressure on the substrate and given time to cure.
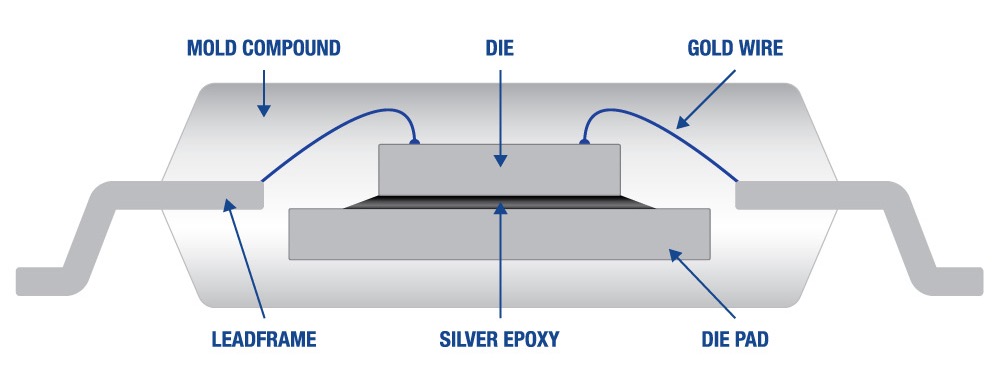
Figure 1. In a typical die attach application involving semiconductor chip manufacturing, operators must secure the chip to a lead frame substrate. A jet valve applies a microscopic line of silver epoxy to the die pad. The chip is then placed with some pressure on the substrate and given time to cure.
One of the most significant challenges manufacturers face when using silver epoxy is laying down precise amounts of the material in individual doses to create a perfect bond-line thickness, while preventing the epoxy from encroaching into other areas of the device.
To accomplish this, Graco’s Advanjet jet valves can dispense dot diameters of 300 µm; and as small as 200 µm depending on material rheology.
Nozzle clogging and inconsistent dispensing caused by silver particles within the epoxy is another challenge manufacturers must deal with when working with the temperamental material. The clogging can slow down or halt production entirely.
One of the world’s largest chip producers contacted Graco Advanjet to try to solve this exact problem. It seems the company’s existing jets were prone to continuous clogging, which led to costly line shutdowns and unplanned maintenance. After over a year of testing Graco’s solution, they replaced their old jets with Advanjet plug-in-play diaphragm jet valves, which did not clog.
Specifying the right Advanjet jet valve for your silver epoxy application
Production managers and engineers can specify jet valves, nozzles, nozzle plates, diaphragms, feed tubes, and syringe brackets to meet any size production requirement. One of many available silver epoxies is Henkel Loctite’s Ablestik 84-1LMISR4. This electrically conductive die attach adhesive has been formulated for use in high throughput, automated die-attach equipment.
A good match for this material would be the following Graco parts:
- Advanjet HV-2000b jet head, Graco PN 26B961 – valve, HV-2000b base 60-2335 – kit, mount, 30/55CC
- NPK-38-125-CA – kit, nozzle plate, 125µm, ceramic
- DK-121 – kit, diaphragm, SB, FKM, COL
- FT09-2811 – tube, kit, FT, Sil, BLK, 55mm, 50PK
Modernise manufacturing with Advanjet high-performance jet valves
Manufacturing engineers need reliability and high-performance jet valves when laying down silver epoxy. Consistent bond-line thickness is also imperative when dealing with fragile and expensive electronic components. Graco’s line of Advanjet microdispensing jet valves offers the industry’s lowest cost of ownership along with ease of maintenance and quick setup, making it an ideal solution for silver epoxy applications which are prone to extensive wear of spare parts and downtime. Fewer moving parts and a patented clog-free design are providing modern manufacturers with a performance edge.
Video 1: Advanjet jet valves