Gear pumps vs diaphragm pumps - advantages and disadvantages
What are the advantages and disadvantages of gear pumps compared to electric diaphragm (EODD) pumps?
Gear pumps vs diaphragm pumps
Gear pumps are used in a wide variety of industries and applications, in part because of their relatively small footprint and low weight, simple design, pulseless flow and ability to withstand high temperatures. However, they suffer from certain disadvantages that can lead to frustrating downtimes, expensive repairs, and even product replacement.
Specifically, in low pressure applications, electric double diaphragm pumps (EODD) have important advantages compared to gear pumps. Electric diaphragm pumps can handle abrasives effortlessly, whereas gear pumps will suffer significantly from increased wear. Unless a gear pump is designed specifically for low viscosity fluids, it will lose efficiency when pumping such fluids. Moreover, unbalanced forces on the bearings will dramatically increase wear and noise levels.
What are gear pumps?
Gear pumps are a type of positive displacement pump, which means they move a fixed amount of liquid by means of mechanical action through the meshing of gears. This creates a suction at the pump inlet and a dispense at the outlet. There are two common types of gear pumps: internal and external. The main difference between the two is internal gear pumps that have an internal and external gear that work with each other, while the external gear pumps have two identical gears rotating against each other.
Advantages of gear pumps
- High efficiency and precision
Gear pumps are known for their efficiency and precision in fluid transfer. Their unique design helps to ensure a smooth and consistent flow of fluids to minimize waste and enhance productivity. - Easy to maintain
Gear pumps generally only have two gears, which makes them easy to maintain and use. The downsides come from gear pumps being expensive to repair and maintain over time with use.
Disadvantages of gear pumps
Gear pumps have several disadvantages compared to diaphragm pumps. Graco’s QUANTM pump is an electric double diaphragm pump (EODD) that addresses many of these common disadvantages of gear pumps.
- Limited operating ranges
Because of their size, gear pumps are unsuitable for operations involving higher flow rates. Each gear pump unit/size has a clearly defined, narrow operational range. Operating outside of these parameters leads to reduced life and ineffective pump performance. Furthermore, the rigid design of the configuration makes it hard to adapt the pump to more demanding fluids. Conversely, the QUANTM electric diaphragm pump has a wide operating range, accommodating a broad spectrum of fluids without compromising performance. - Challenges with low viscosity fluids
For a gear pump to effectively pump fluids at high pressure, the working parts inside must have very tight clearances. If not, very thin fluids (solvents) can slip through these tight spaces from the high-pressure (outlet) side to the low-pressure (inlet) side of the pump. Depending on the outlet pressure, the viscosity of the fluid, and the working clearances inside the pump, the slip causes a reduction in flow rate and pump efficiency. Additionally, thin fluids can lead to increased pump wear because of their poor lubricating properties. - Challenges with abrasives
The gear pump’s close tolerances and tight spaces make it a less than ideal solution for pumping liquids containing abrasives. Abrasive particles can work their way into these tight spaces and cause accelerated wear and rapidly reducing pump performance. The resulting wear rate from pumping abrasives depends on the hardness, size, and concentration of the particles, and the operating speed of the pump. QUANTM is engineered to handle abrasives and solids without damage to extend pump life and reduce potential for costly repairs. - Unable to run dry
Gear pumps have limited priming capacity and cannot be allowed to run dry for prolonged periods without causing damage to its stators and rotors. Fluid must be present to lubricate the contacting surfaces between rotor and stator, to dissipate the friction and heat generated by the pump. QUANTM is designed to run dry, offering peace of mind and protection against dry run conditions. - High maintenance costs
Gear pumps have a number of rotating parts that need precision tolerances, which makes them expensive to manufacture and maintain. In addition, expensive and sensitive seals can leak and require replacement. QUANTM’s fewer moving parts can translate into significant savings on maintenance and replacement costs over time.
Common gear pump applications
While gear pumps are commonly used in various industries due to their precise flow control and ability to handle viscous fluids, they may not always be the best fit for every application. Here’s a look at how gear pumps are used in specific industries and QUANTM’s potential advantages:
- Water - wastewater treatment
Gear pumps are used in water treatment facilities for dosing and transferring chemicals. However, their limitations become clear when handling diverse ranges of fluid viscosities and compositions found in these settings. QUANTM electric diaphragm pumps offer more flexibility to ensure reliable operation in the demanding water and wastewater treatment environment, where varying flow rates and chemical resistance are crucial. - Chemical mixing and blending
The precise metering capabilities of gear pumps make them a common choice in chemical mixing and blending. Where they fall short is their high maintenance requirements and difficulty with low-viscosity fluids. The seal-less design of QUANTM eliminates leaks, making it a safer and more efficient choice for handling aggressive and corrosive chemicals. - Paint transfer
In the automotive and paint industries, gear pumps facilitate the transfer of high-viscosity products. The presence of solids and abrasives in paint can accelerate wear on gear pump components. QUANTM’s diaphragm pumps are able to transfer viscous, abrasive, and shear-sensitive materials to increase operational reliability and reduce wear-related costs in paint transfer applications. - Ink transfer
Gear pumps are used for ink transfer because of the steady flow they provide, which is needed for consistent print quality. However, the intricate cleaning required between jobs to prevent contamination is a significant disadvantage. QUANTM pumps, on the other hand, are easy to clean and maintain to provide a contamination-free solution for ink transfer processes.
In each of these industry applications, QUANTM electric diaphragm pumps have their own unique advantages over traditional gear pumps by offering versatility, lower maintenance costs, and the ability to handle a wider range of fluids. By incorporating QUANTM pumps into these applications, facilities can achieve more efficient, reliable, and cost-effective operations.
Graco QUANTM electric diaphragm pumps
QUANTM electric diaphragm pumps provide much more flexibility and a significantly lower maintenance cost over gear pumps. Take a look at some of the benefits:
Gear pumps | Graco QUANTM EODD pumps |
Running dry for less than a minute will destroy the stator | Can run dry indefinitely - avoiding expensive repairs |
High repair cost for spare parts | Easy to repair at low cost |
Deadhead/stall causes severe damage | Easily manages a deadhead/stall with no additional equipment which prevents pump failures |
Abrasive-containing fluid can quickly cause a failure | Easily handles all fluids with abrasives |
Shaft alignment is difficult to maintain | No spinning shaft seals; No alignment necessary |
Very expensive for larger flow rates | Can handle large bulk flow rates |
Minimal suction capability | A self-priming pump with smooth flow |
Not suited for water or other low viscosity fluids | Suitable for all types of fluids, including abrasives and solids |
ROI calculator
Interested in going electric?
Answering three easy questions, calculate how much you could save by converting your facility to Graco electric double-diapragm pumps.
1) What industry are you in?
Based on your industry, we can set some default system requirements, like pump size, flow rate, and fluid pressure. Have you got a highly customised setup? Try our Advanced configurator.
2) How many pumps do you have?
We will estimate your savings based on the number and energy consumption of the pumps you already own.
3) What are your energy costs?
We will estimate your energy savings based on the average energy prices in your area.
Annual operational savings:
Check out our Advanced ROI calculator to learn how we calculated your savings.
Start again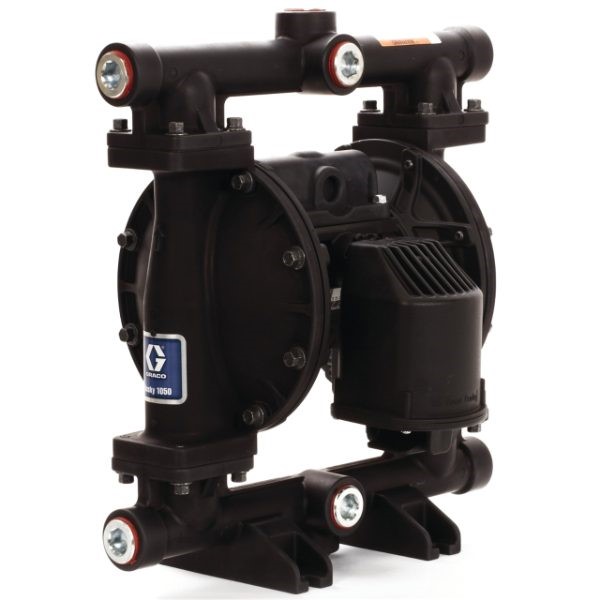

Related articles
The eleven benefits of an electric diaphragm pump
Understand the working principle of a diaphragm pump, the different types of diaphragm pumps, and the common uses and applications.
Electric diaphragm (EODD) pumps vs other technologies: pros and cons
There are many different types of industrial pumps, including diaphragm pumps, gear pumps, peristaltic pumps, and more. See an overview of each.
Electric oil pumps lead the way to improve energy efficiency and sustainability goals
Electric pumps lead the way to energy efficiency and sustainability goals