How to select a pump for sanitary applications
Are you sure you have the right pump for your application?
Proper ingredient transfer equipment is crucial in maintaining optimal efficiency and high product quality while balancing operating costs. That’s why pumps are some of the most important pieces of equipment in your industry.
But are you sure you have the right pump for your application? You need to consider certain pump specifications related to the processing challenges to select with confidence.
In this article, we describe two common sanitary applications, and how the right pump for each of them was selected.
1. Application: Pumping jam
A jam-making plant in France had four large jam cooking pots running at a temperature of 95-100oC. From these, the hot jam was to be conveyed to heated conditioning machines. Here the jam would be thoroughly mixed to ensure a homogenous blend of the fruit pieces in the jam, before being piped into jars.
The company was looking for the correct type of pump to transfer the jam from the cooking pots to the conditioning machines. Although they were making a variety of jams such as strawberry, cherry and apricot, only one pump was required. This sanitary application threw up several specific challenges:
- The high temperatures involved meant that standard plastics could not be used as these would likely melt at 95-100oC.
- The stickiness and high sugar content of jam demanded a solution that would be quick and easy to clean during product changeovers in order to prevent cross-contamination.
- It was crucial to transfer the jam as fast as possible to prevent it from cooling down, otherwise extra energy would be needed to reheat the jam in the conditioning machine.
- Most of the jams being made contained large particles of fruit, up to 1 cm in diameter.
How did Graco meet these challenges?
To address the high temperature aspect of the application, an over-molded diaphragm made of EPDM was chosen, as this material works effectively up to a temperature of 121oC. This also addressed the issue of cleaning. An over-molded diaphragm has no central hole or bolt, which makes cleaning significantly easier.
To ensure fast transfer, a 3-inch or 4-inch pump was necessary. And the pump must be capable of pumping large particles. A pump containing balls would not work as it would crush the particles – but a flapper pump would be ideal. For example, a 3-inch flapper pump is suitable for particle sizes up to 6 cm in diameter. Upgrade to a 4-inch pump and you can pump particles of 10 cm diameter.
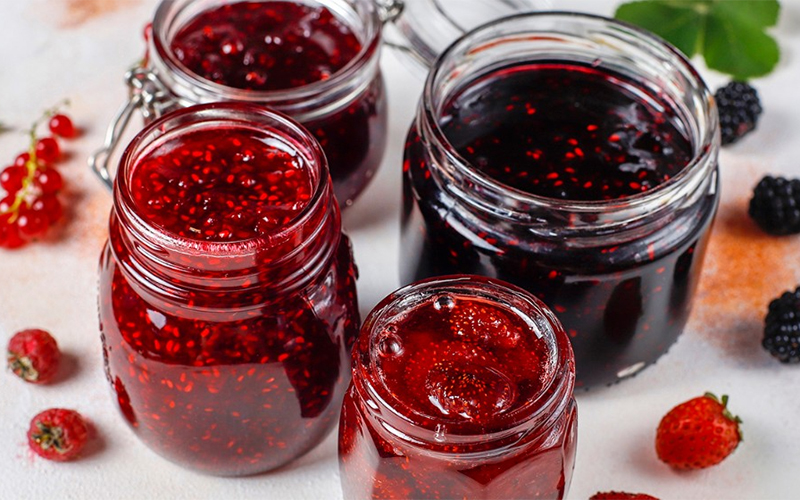
Which pump did Graco select to pump jam?
Graco offers a Sanitary Pump Selector Guide which makes it easy to translate specific application requirements into a particular product. For this jam application, Graco’s experts chose the SaniForce 3000e electric diaphragm flapper pump. The pump is specifically designed to meet the requirements for the most rigorous food, beverage, personal care, and pharmaceutical transfer applications. This high-speed 3-inch pump operates at 227 lpm (60 gpm). The center section is made from 316 stainless steel and the diaphragm as well as the manifold O-rings from 3A-approved over-molded EPDM. The SaniForce 3000e provides the same outstanding self-priming, stalling and seal-less design of Graco’s air-operated pumps but in an electric package.
Why select electric instead of pneumatic?
Graco chose the electric version of the SaniForce 3000e for a number of reasons. It operates with a very low noise level, improving the working conditions. It’s more efficient and consumes less electricity than the comparable pneumatic pump, reducing running costs. The absence of air* also reduces the risk of contamination of the production environment.
An electric pump can be fully automated using a Variable Frequency Drive with the appropriate inputs and outputs. And there is no need for a pneumatic changeover mechanism. In an air-operated double diaphragm pump this mechanism is located inside the body, which makes it susceptible to problems caused by high temperatures.
2. Application: Pumping toothpaste
A toothpaste manufacturer needed to pump toothpaste from a 200-liter drum to a filling/dispensing unit which would then fill individual toothpaste tubes. They were aiming to evacuate eight drums per day, and had a hose discharge length of 6-7 meters. The challenge was to select a pump capable of efficiently transferring a high viscosity and abrasive substance over a long distance.
How did Graco meet this challenge?
Unlike with the jam application, diaphragm pumps were not considered as these will not run at such high viscosities. Instead, attention turned to one of Graco’s 12:1 priming piston pumps. This has the possibility to be mounted on a ram to form a complete drum unloader.
To meet the challenge of abrasive material, it’s necessary to select packings that are resistant to abrasion. These are called U-cups and are made from polyethylene which is very resistant to abrasion. The U-cup scrapes the toothpaste off the piston rods before the toothpaste has an opportunity to cause abrasion or get stuck between the packing and the piston rods.
To optimize transfer efficiency, it’s necessary to automate every single drum that has to be emptied. Graco has developed a range of high-end drum unloaders with built-in automatic sequencing. This means that the level at which you start pumping can be automatically set, as can the level in the drum where you have low evacuation.
To ensure efficiency over long discharge distances, the 12:1 piston pump can deliver 100 bar of pressure at 60 cycles per minute. In other words, the 12:1 pump combines high volume and high pressure to provide an excellent solution for this toothpaste application.
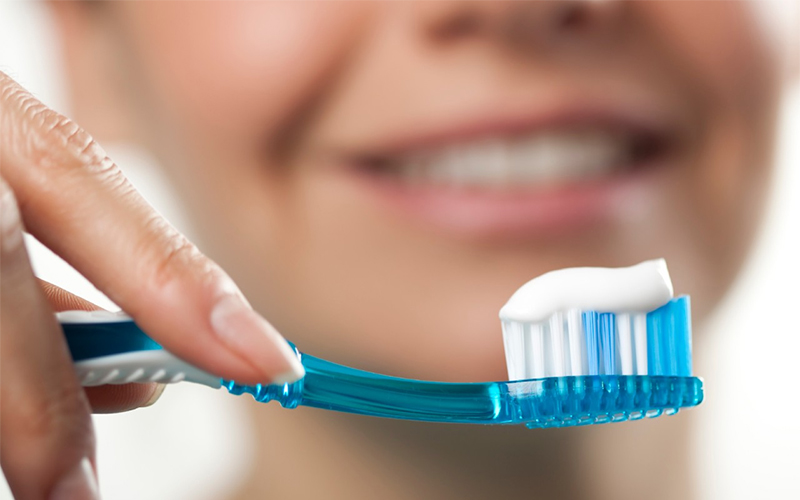
Which pump did Graco select to pump toothpaste?
Two characteristics of toothpaste have to be taken into account when choosing a pump to transfer it from one piece of equipment to another. Firstly, it is a high viscosity product, with a typical viscosity of between 100,000 and 150,000 cPs. Secondly, it is abrasive by nature. To ensure it works more effectively, toothpaste manufacturers add gritty ingredients such as mica, silica or chalk.
Again, Graco offers an easy way to select the right pump for a specific application. For piston pumps it’s via this Piston Pump Selector. The resulting pump was then combined with a ram to form a complete Sanitary Drum Unloader. In this case it was the SaniForce 12:1 Stainless Steel Drum Unloader Piston Pump Package. It features an on-demand workflow capability and can be taken apart quickly for applications that require frequent sanitation.
The pump ram has an inflatable seal, and the concave shape of the ram plate makes it easier to prime the pump. The ram plate and pump is lowered into the drum, just above the product. When the pumping starts the product is moved out of the drum, while the plate with inflatable seal travels down into the drum , scraping product from the sides of the drum. After the drum is emptied, the plate and pump can be lifted out by simply switching a button. In this way, evacuation rates up to 99% can be easily achieved.
Need help selecting your pump?
As mentioned above, Graco offers a number of pump selector guides. They will help you select the right pump for your specific sanitary application. If you require further assistance, or would like to see a demonstration of a sanitary pump, then please fill in the contact form below.
*Note that compressed air is still needed with this electric pump, to inflate the center section. The air can be supplied from an air line or from a small air compressor. Less than one liter of air per day is needed.
Related Articles
How to efficiently evacuate low to high viscosity products
Graco offers three ranges of unloaders to evacuate products of any viscosity. We explain the key differences between them.
How to pump large particles of food
Large-particle pumps are key pieces of equipment in the food processing industry where they are used to transfer a wide range of foods.