Keeping an annealing furnace running
Lionoil has equipped the rollers of an annealing furnace at steelmaker Aperam in Genk, Belgium with a fully automatic, fully monitored lubrication system from Graco.
Aperam is a global player in stainless, electrical and specialty steel, with customers in over 40 countries. In 2020 the company shipped 1.68 million tonnes of its steel. It has six production facilities in Brazil, Belgium and France. Its melt shop in Genk, Belgium includes two electric arc furnaces, argon-oxygen decarburization equipment, ladle refining metallurgy, a slab continuous caster, and slab grinders. It also includes a cold rolling mill facility.
In 2020, Aperam invested several million euros in a high-tech annealing and pickling line in Genk, which specializes in the production of the highest quality stainless steel.
Automatic lubrication is a must
Right from the start, the objective was for the new line to function continuously with a minimum of maintenance. To meet this goal, an automatic lubrication system is essential. Such a system includes lubrication pumps that automatically supply grease in small amounts at frequent intervals, ensuring proper lubrication when the rollers need it most – when they are in use. They thus significantly cut maintenance and repair costs, and maximize machine up-time.
When lubrication is applied manually there is always a risk of either over- or under-lubricating the rollers, which can eventually lead to machine failures. And if a steel annealing line goes down, production losses can quickly add up.
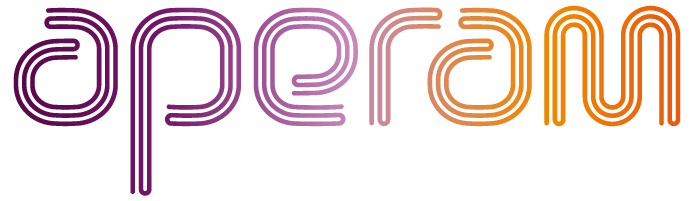
Lionoil chooses Graco equipment
For this demanding application, Aperam called on the lubrication management company Lionoil from Antwerp. Lionoil had earlier equipped an Aperam annealing furnace in Genk with a lubrication system in 2017.
Lionoil equipped the rollers of the annealing furnace with a fully automatic, fully monitored lubrication system. They selected two Graco LD 50:1 grease pumps to use with 181 kg grease drums (one as backup and during drum change). These affordable and full-featured pumps are compact, flexible and durable.
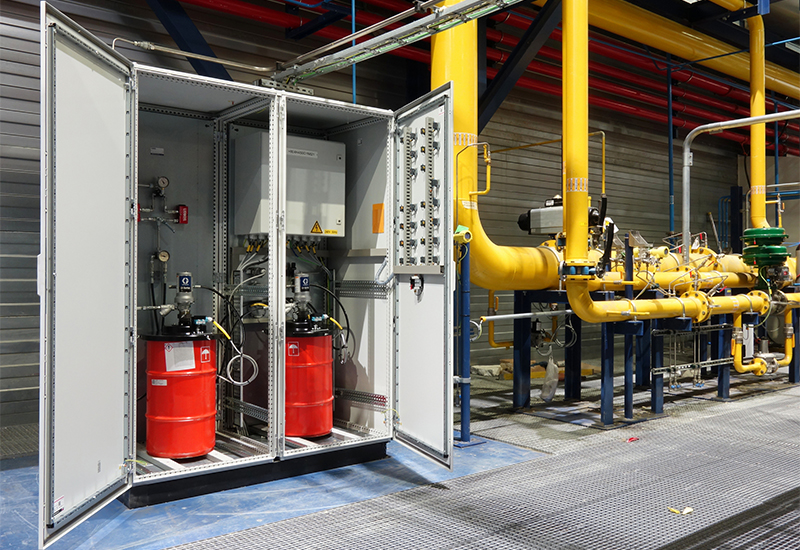
The patented cup and plate design of the LD pump eliminates the need for O-rings that can quickly wear out, thus ensuring a more durable, longer-lasting solution. Their in-line pump design aligns the air motor piston and fluid piston rods to maximize seal life. And a patented self-cleaning design increases reliability in dirty air environments and minimizes pressure drop with rapid changeovers for reduced stalling and smoother flow.
Complementing the LD pumps are Graco’s Trabon MSP Series Progressive Divider Valves. These feature quick-change valve sections that can be removed from the base assembly without disturbing any lube lines – minimizing labor cost and maximizing machine uptime. They can be easily accessorized with magnetic and electronic proximity switch cycle indicators to provide real-time assurance of a successful lube event. The alternate outlet on the face of the valves can be fitted with optional performance indicators, taking the guesswork out of troubleshooting. Finally, built-in outlet check valves ensure accurate lube delivery, every time.
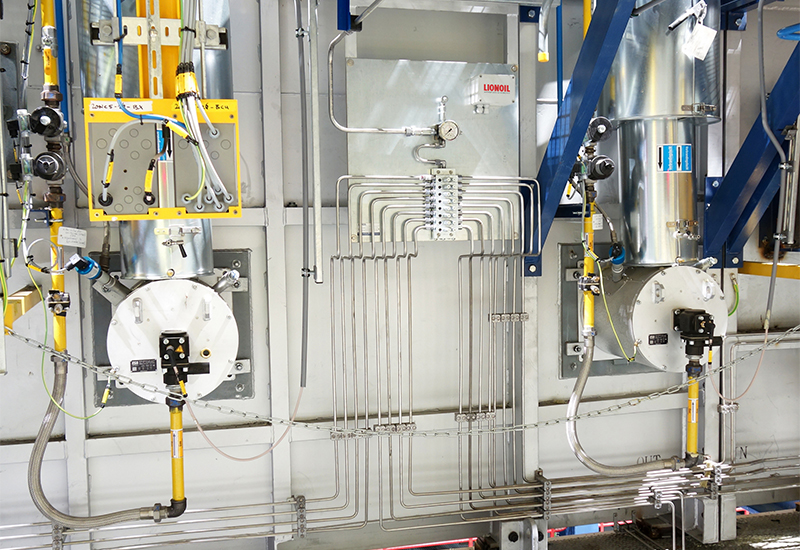
Automatic lubrication keeps the line running
The installation at Aperam is divided into four zones controlled from a main cabinet. Each zone has specific requirements for lubrication quantity within a certain time period. The Graco LD drum pump in the central mounting station feeds the Trabon progressive distributors placed on eight mounting plates. The second LD pump ensures continuous operation during lubricant barrel change. This means it’s possible to move from one pump to the other without interrupting lubrication.
Installation was done in several phases by specialized Lionoil technicians, who also did extensive testing before delivery. Thanks to Lionoil’s specialization and flexibility, it was possible to develop and install the completely automatic lubrication system based on the project specifications and the demands of the customer.
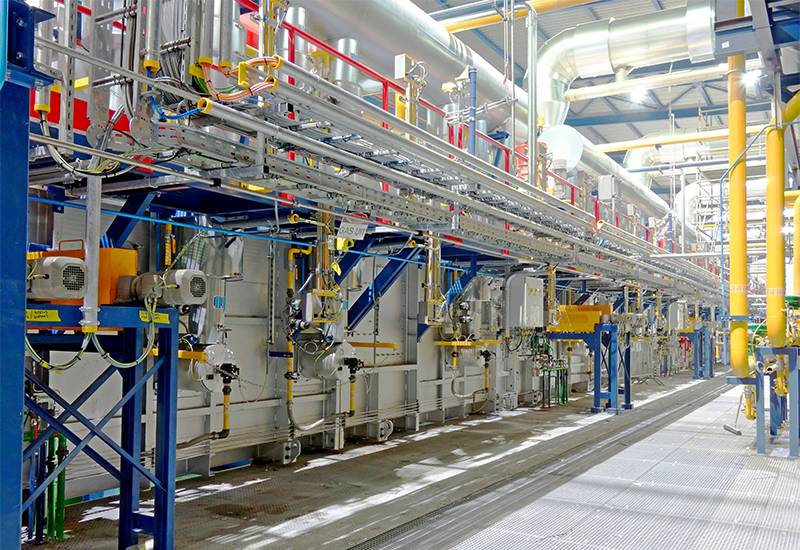
MORE INFORMATION
If you are interested in learning more about Graco’s automatic lubrication products, fill in the form below.
Related Articles
Belgian brewery reaps the benefits of automatic lubrication
The Duvel Moortgat Brewery has selected a 1725-point automatic lubrication system from Graco for its 180,000 per hour bottling line.
Understanding the Basics of Automatic Lubrication Systems
Discover what components make up an automatic lubrication system.
What is lubrication and why is it important?
Lubrication is a crucial element in the efficiency and life-expectancy of any rotating equipment.