Case study
Potting solar panel junction boxes
Background
Junction boxes are installed at the rear of photovoltaic (PV) panels and serve to protect electric components from environmental elements. To improve the junction box mounting and protect integral components, a solar panel manufacturer was exploring ways to decrease costs, improve manufacturing efficiency, and meet panel lifetime expectations.
Challenge
The customer was looking for the most efficient and consistent way to pot their solar panel junction boxes. It was paramount that they found a reliable solution that would protect the ribbon wire connection from corrosion as well as protect against moisture ingress through the back panel. In addition, the potting materials had to seal and adhere to a variety of substrates including a plastic junction box, metal ribbon wires, and the glass back panel.
Solution
Graco and its distributor partner worked to provide a metering, mix, and dispense system to process a 20:1 (by volume) silicone potting material with a shot size of approximately 30 cc. To verify the application, Graco qualified its PR70 posi-ratio metering, mix and dispense system at the Graco application lab in North Canton, Ohio. The 20:1 volumetric ratio was easily obtainable with the PR70v variable-ratio system. Ratio and shot size repeatability studies proved the system to be reliable in processing the potting material. An additional benefit of the PR70v variable ratio system is that the dispensing ratio can be fine-tuned without additional hardware or kits. If the ratio of the material needs to slightly change, the PR70v machine can handle it.
The PR70v was equipped with an MD2 dispense valve with a spring-loaded poppet nose to keep the base material separate from the catalyst material within the MD2 valve. Since the catalyst material is moisture sensitive, the catalyst tank was equipped with the nitrogen blanket accessory to displace moist air. Both the base and catalyst tanks were equipped with a low-level sensor to indicate when a refill is required. Additionally, the base tank was equipped with an automatic refill-kit for automatic refilling of the tank using a drum supply system.
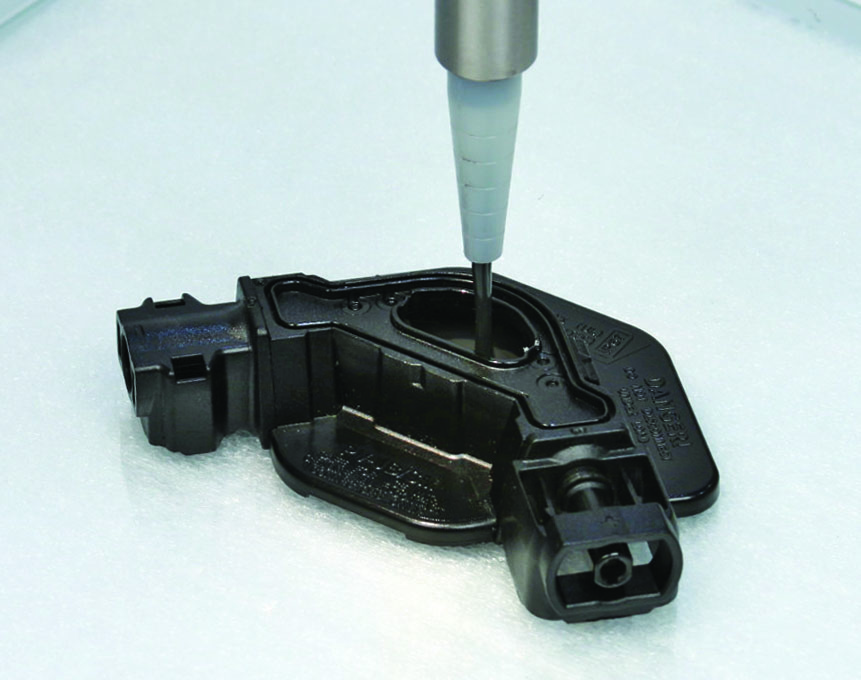
Results
Material ratio, flow rate, and shot size consistency were all critical factors when potting junction boxes. The Graco PR70v was able to perform exceptionally on all three requirements. With the level sensors and base side auto-refill, the system had the overarching capabilities to meet their goal of high volume solar panel production. With the PR70v posi-ratio metering, mix, and dispense system, the customer is well equipped to reliably and repeatedly dispense the potting material into the solar panel junction boxes in a mass production manufacturing environment.
For more on how the PR70 posi-ratio can assist your plant to succeed in reaching its goals, reach out to one of our experts today!
End user
Solar panel manufacturer
Industry
Solar panel manufacturer
Material supplier / distributor
Quantum Silicones - Richmond, VA
Material specs
QSil 6201 (UL pending)
Silicone potting material
Typical properties
- Ratio (A:B) by volume - 20:1
- Viscosity:
- Part A - 6,000 cps
- Part B – 30 cps
- Part B (catalyst) – moisture sensitive (requires nitrogen blanket)
Graco Equipment
PR70v metering, mix and dispense system
Configuration:
- System Part number: PR7E-JAYA1EACA334411JAJAANN3
- Blue side pump: 960
- Red side pump: 80
- Hoses
- 1/2 in. (12.7 mm) x 15 ft. (4.5 m) SS braid, TFE lined
- 3/16 in. (4.7 mm) x 15 ft. (4.5 m) SS braid, TFE lined
Accessories
- MD2 dispense valve with 10:1 nose poppet valve
- Pressure transducers
- 32 element static mixer or a combo mixer for optimum mixing
Delivery method
- 30 litre off-board high volume (base) tank with stand
- Equipped with high / low level sensors for automatic refilling
- 55 gallon drum supply pump: for refilling the tank from the material’s original container
- 30 litre low volume (catalyst) tank with low level sensor
- Nitrogen blanket kit to eliminate air (moisture) from the tank
- Nitrogen blanket kit to eliminate air (moisture) from the tank
Contact an expert
Related articles
Warm applied solar panel edge sealant
A solar panel manufacturer improves its bead profile and application speed while removing quality issues related to the dispensed edge seal adhesive.
Solar panel edge seal: Liquid-applied vs. tape
Uncover the advantages of pumpable solar edge tape (PSET) over traditional tape application methods and how PSET improves your manufacturing efficiency and product quality.
Silicone sealant for solar frame attachment
Discover how a solar panel manufacturer improved bead profile consistency for solar frames using Graco automated silicone dispensing solutions.