The Smart Way to Mix Paint
Graco ProMix PD2K paint mixing machines play a key role in the digitalization of painting lines at Pieffeci Turin
Italian company Pieffeci handles outsourced industrial processes such as coating for large industrial groups. Its activities cover production, technology management, and plant maintenance. It also designs new systems for its customers, and supervises their supply, installation, and start-up.
Since 2001, Pieffeci has managed the axle coating line of FPT Industrial in Turin. FPT Industrial is dedicated to the development, production, sale and support of powertrains under the brand name CNH Industrial for on-road, off-road, marine and power generation applications. It’s one of the leading world players in engines, axles and transmissions for the industrial sector.
Pieffeci’s activities are closely linked to FPT’s production process. As raw workpieces come off the end of the FPT assembly process, they are loaded onto an overhead conveyor that is directly linked to the paint shop. Here the products are coated, retouched, and prepared for direct shipment to the FPT warehouse.
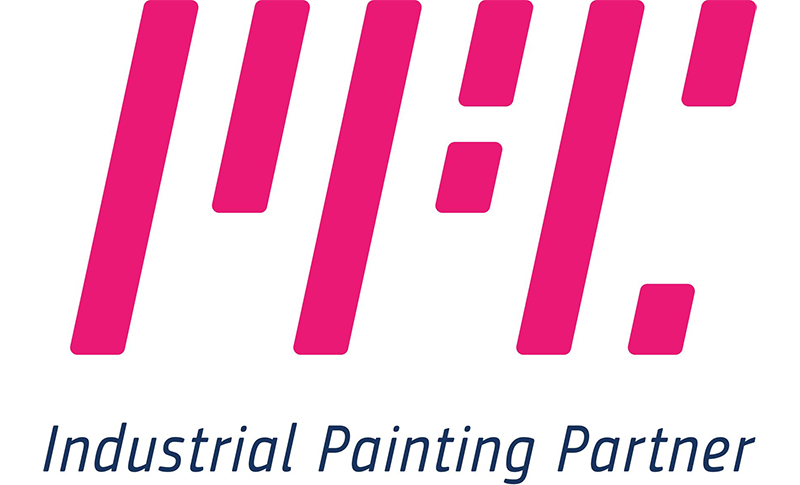
Digitalizing the factory floor
In 2017, Pieffeci instigated the “Plant Supervisor” digitalization program. The objective was to create an interconnected system that would guarantee quality and product traceability, continuously monitor working conditions and process parameters, and digitalize and automate previously manual operations. The overall benefit would be increased efficiency of the entire production process.
A first step involved tagging all workpieces with RFID tags so that they can be identified and tracked by eleven RFID readers. This enables all process parameters to be controlled at each station of the coating line. Further work involved the installation of sensors and actuators throughout the production plant; the implementation of a Manufacturing Execution System (MES) that connects with the PLCs of the machines and the factory IT systems; and the integration of remotely controllable machines to improve the control of all coating parameters.
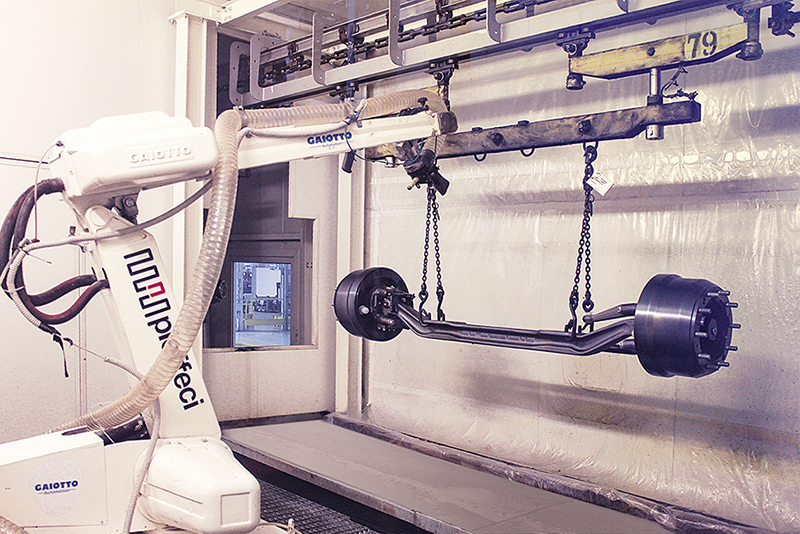
New Graco paint mixers
A key goal of this digitalization program was the optimization of two-component paint mixing operations to improve the coating quality. At the same time, it would rationalize paint consumption and application through reducing the need for touch-up operations. With these objectives in mind, Pieffeci installed new Graco ProMix PD2K positive displacement proportioning systems, linked to Gaiotto Automation robots integrated in the primer and enamel application booths.
The ProMix PD2K mixes the material close to the gun so the flush zone is significantly smaller. This allows customers to use less paint, spend less on disposal costs and allows for faster color changes. And because there is limited mixed material in the system, the ProMix PD2K is ideal for short pot life materials. It is also compatible with acid-based materials.
Pieffeci was the first company in Italy to install these new paint mixing machines. A pilot project was first carried out in October 2017, involving one mixer. After fine-tuning and proving its high reliability, ProMix PD2K proportioners replaced the older Graco Promix 2KS proportioners previously in place.
Close communication between Graco’s and Gaiotto’s engineers allowed the development of a communication protocol between the PLCs of the various machines and the MES, in order to ensure product traceability, monitor consumption, and carry out predictive maintenance.
The new Graco proportioners are connected to the LAN via special gateways, which allow them to connect with and be remotely controlled by the factory management software system. The mixers receive data on the required paint flow rate directly from the PLCs interconnected with the MES software package and they send consumption data back to the PLCs (and then to the MES) at the end of each cycle.
In addition, sensors monitor the pre-treatment parameters, the coating parameters of the robots, the actual paint consumption, the catalysis rates, the conditions of the paints in use and in preparation, the environmental conditions of the coating booths, and the oven temperatures.
Benefits of ProMix PD2K proportioners
Based on FPT’s specifications, Pieffeci applies a coating thickness of 70-80 microns on the workpieces, with spraying programs that require flow rates from 50 to 350 cc. Graco’s unique ProMix PD2K dosing piston pumps stall under pressure and use 100% positive displacement technology to always provide accurate mix ratios and consistent performance. Moreover, they work well even with very low flow rates because they can perform optimized mixing programs in terms of consumption and overspray.
The Graco mixers have increased the accuracy that paint is dosed and delivered. This is because the machines are highly stable as they are controlled in a closed loop, which leads to a significant increase in finishing quality. As the mixing point is closer to the gun, the ProMix PD2K has significantly reduced solvent use and mixed material waste. This has contributed to Pieffeci reducing maintenance in terms of both frequency and duration. Finally, interconnection with the MES management software system allows the mixers to be remotely controlled, thus gathering paint consumption and alarm data in a precise, accurate, and constant way.
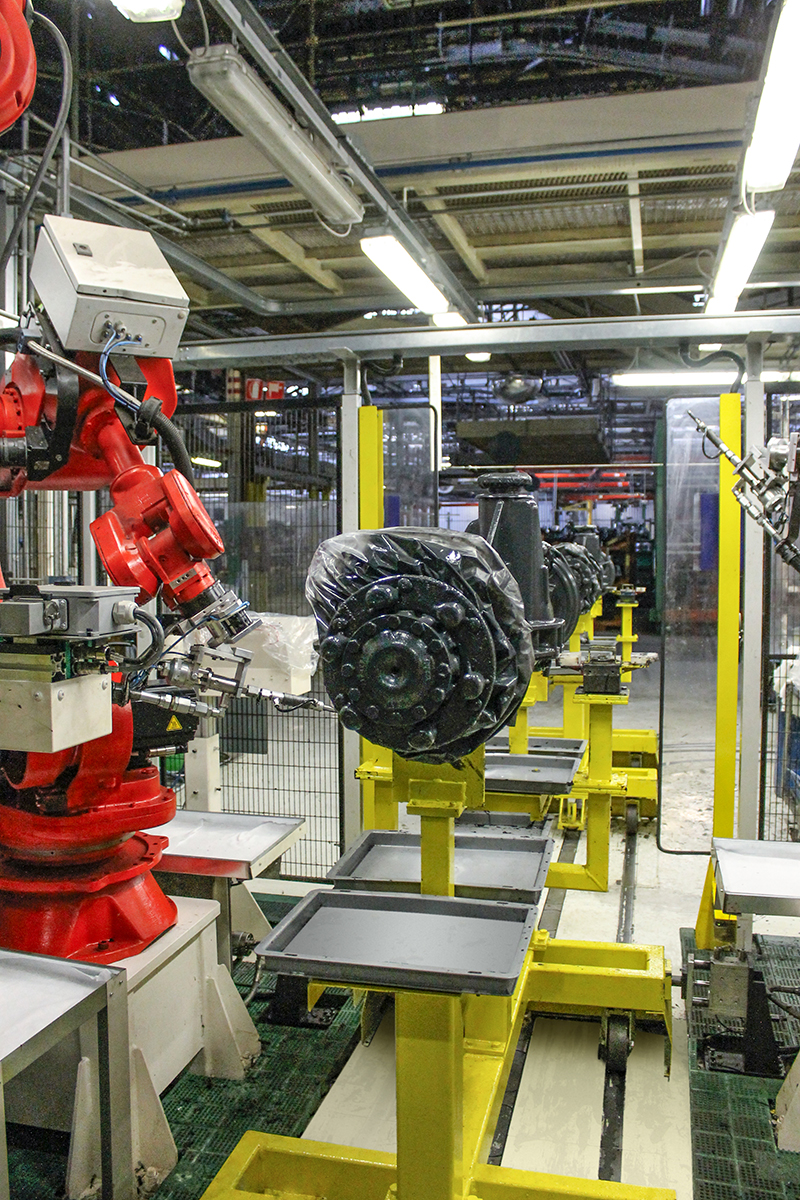
Successful digitalization
Thanks to the “Plant Supervisor” project and its investments in automation and in the ProMix PD2K mixers, Pieffeci is now able to constantly monitor all work in progress in the various sections of the plant; track the position of specific workpieces in the system; assign an urgent status to specific workpieces; and receive immediate notifications about system anomalies. The company can also digitalize all reports on production, quality, and defects, and precisely assess and ensure repeatability of the coating quality.
Further information
If you would like to know how Graco’s ProMix PD2K proportioners can improve finishing quality and reduce paint consumption in your paint shop, fill in the form below.