Truck Factory Paint Line Avoids Rejected Parts and Operator Error
Intrinsically safe barrier kit enables automation inside paint mix room’s hazardous area.
ProDispense solution controls equipment in hazardous and non-hazardous areas
CUSTOMER: Commercial vehicle manufacturer
GRACO EQUIPMENT: ProDispense Intrinsically Safe (IS) Barrier Kit
CHALLENGE: A heavy-duty truck manufacturer used a three-component material -- a resin, an accelerator and a catalyst -- to paint chassis for tractor-trailers. This made for extra challenges between the paint kitchen’s hazardous and non-hazardous areas.
Paint line operators hand mixed the resin and accelerator separately before sending it to the hazardous area to be combined with the catalyst. But hand mixing caused costly ratio accuracy problems.
- If not enough accelerator was added, the chassis would come out of the oven wet.
- If too much accelerator was added, the chassis would have a brittle finish with air bubbles or craters along the surface.
Such defects weren’t detectable until the end of the paint line. By the time they noticed a bad finish on one chassis, up to four more would be rejected.
This wasn’t their only downtime issue. The mixture needed to be stored in a separate tank and refilled often. To fill the tank, operators would use a dead-man pneumatic ball valve. To attend to other tasks, they would often wedge the ball valve open, leaving the tank unattended. This caused overflows of up to 273 litres (60 gallons) that required several hours of halted production to clean up.
Paint line operators needed a clean and safe way to automatically mix the material and refill tanks in the paint mix room. But electronic controls were not typically safe for hazardous areas.
SOLUTION: The paint line manager agreed to test the ProDispense Intrinsically Safe (IS) Barrier. This new technology would allow easier installation and control of key paint room equipment inside the hazardous area.
Now they could precisely mix the resin and the accelerator and automatically replenish material.
- The fluid dispense unit outside the hazardous area fed into a tank inside the hazardous area.
- The tank was equipped with Graco’s level sensor and remote fill solenoid technology. Whenever the tank ran low, it worked with the intrinsically safe barrier to communicate with the control panel.
- The ProDispense automatically refilled the tank.
RESULTS: The ProDispense Intrinsically Safe Barrier provided a way to safely install the solenoid valves and meters within the hazardous area. Reducing excess cable and fluid lines in installation by over 60 per cent.
The commercial vehicle manufacturer now can do something it could not do before: Run automated systems from within the hazardous area in a clean and safe way.
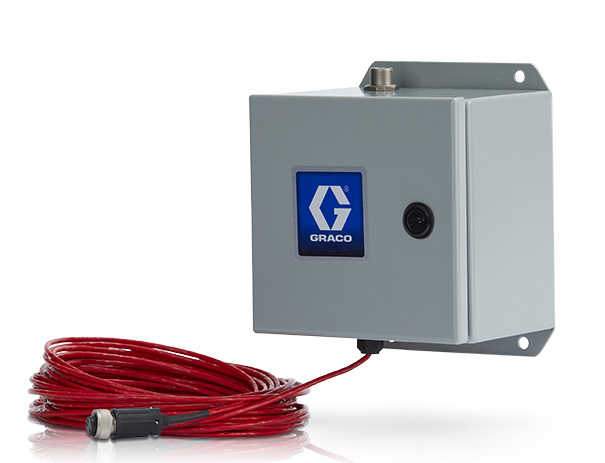
What’s an intrinsically safe barrier?
In an industrial paint kitchen, an intrinsically safe barrier is an approved way to regulate the energy running through the hazardous area. It provides enough energy to power the equipment, while limiting the maximum output.
The ProDispense Intrinsically Safe Barrier allows electronic controls to communicate with equipment that’s inside a hazardous area.
Related articles
No More Running Around
Military vehicle finisher finds solution to small batch mixing. Wireless start/stop switch allows control inside hazardous area.
Creative Mixing Eliminates $75,000 a Year in Bad Parts
Tier 1 supplier finds safe, compact option for precision mixing. Industrial fluid dispense system pays off in less than a year.