Controlling and Managing Excess Heat
Dissipating Heat In Electronics Manufacturing
As electronic devices continue to get smaller and more compact, the circuit density involved with internal electronics will continue to increase. Manufacturing challenges are compounded when there is less ambient space to move unwanted thermal energy generated from semiconductors, processors, control modules and printed circuit boards.
In order to provide the high performance and long-term reliability that end-users demand, electronics manufacturers must continually look to find more efficient ways of dissipating excess heat to keep components running optimally.
Critical for Electronic Devices of any Application
Slower operating speeds or compromised durability are the death knell of most electronic devices – regardless of size or application. In addition to generating unwanted excess heat, key internal components are often sensitive and fragile, requiring protection from vibration and environmental contamination. As a result, applications of thermal interface materials (TIMs) and other materials on or around these components must be as accurate as possible to avoid damage during the product assembly process.
For design and production engineers tasked with refining electronic manufacturing processes to increase performance, durability and control excess heat, their efforts require a deep understanding of Fourier’s Law and the concepts of thermal conductivity and thermal resistance. Depending on the part or component and other potential considerations like surface imperfections, thermal equations for design engineers seeking heat dissipation solutions can be complex to determine the best process, materials and equipment involved.
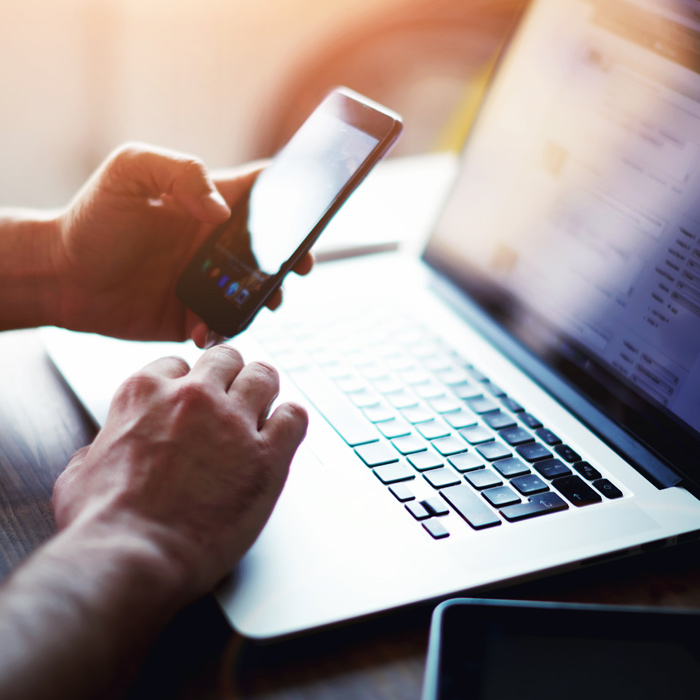
Surface Imperfections
Imperfections on surface areas of the components provide unwanted spaces or air gaps that act as thermal insulators and make it more challenging to dissipate heat. Increasing the MTBF (Mean Time Between Failures) with a new or redesigned device often comes down to choosing the right thermal interface material (grease, thermal paste, thermal pad, etc.) and pushing the boundaries of that material to achieve the desired thermal resistance within the desired cost parameters.
Success often requires ongoing collaboration with material suppliers to confirm how thermal management disciplines work for a desired application. Production engineers and operations managers must also understand the handling characteristics of the material to understand how the manufacturing process will be affected.
What About Thermal Pads?
Pre-formed thermally conductive pads are known for being easier to install, but they typically require costly manual labour and may result in higher application thermal resistance when compare to a small amount of dispensed thermal interface material. These dispensable TIMs are often a more efficient choice for controlling excess heat in electronics manufacturing.
Previously dismissed as messy and too difficult to control, these fluid TIMs help provide a more streamlined approach. With an easier validation & testing process, an efficient transfer from design to production and flexibility to support subsequent design changes without pad retooling costs – dispensable TIMs can ultimately help provide a lower manufacturing cost per unit.
Dispensable Materials are Ideal for Precise Tolerances
Given the accuracy requirements and tolerances with today’s ultra-small electronic devices, manufacturers have been typically cautious about switching to a dispensable material as success largely depends on the process involved and the capability of the material dispensing solution. In addition, a lack of proper training and ongoing support is another challenge for electronics manufacturers as automated dispensing solutions typically consist of parts and components from multiple suppliers.
To properly support thermal interface dispense processes, Graco has developed a new line of highly capable solutions for dispensable thermal interface materials. The Graco UniXact automated dispense solutions deliver the accuracy, repeatability and throughput required by electronics manufacturing engineers and operations managers.
UniXact automated dispensing solutions are the only end-to-end automated fluid dispense systems - utilising all of the components, XYZ motion and software from one source, Graco. With facilities located in Europe, Asia Pacific and the United States, Graco provides a personalised, end-to-end partnership experience for electronics manufacturers with solution planning and testing, as well as on-going, in-person support from our worldwide distribution network.
Thermal Interface Solutions
To learn more about how Graco can help electronics manufacturers accurately dispense thermal interface materials to control excess heat more efficiently, visit UniXact.
Related articles
Thermal Paste vs. Thermal Pads
Thermal Interface Materials: Thermal paste/grease vs. thermal pads
Precision Dispensing for Bonding and Sealing
When a product's functionality depends on a perfect bond or seal, dispensing an imperfect bead could lead to considerable cost implications.
Jet Valve Dispensing – Easy to set up and Maintain
The simplicity of Graco’s patented diaphragm jet, with only two internal moving parts, delivers one of the industry’s lowest running costs per million cycles of the jet.