Aiming for optimal product development and technical support
Colorplas is a significant force in the GRP industry, manufacturing a wide range of gel coats & also supplies resin, reinforcement and ancillary products since 1991.
They initially specialized in polyester colour paste dispersions and are now recognized as pioneers in service and consistency of products. “We started out in the pigment dispersion market and originally we used to supply just that one product in different shades. Then our customers began to ask us why we don’t manufacture gel coat,” says Joe Parkinson, Sales and Marketing Director at Colorplas. “So, we looked into that, developed our own gel coats and now, over the 27 year span, we have a full variety of gel coats from ISO Modified to NPG, Spray, Brush and Topcoat viscosities”.
Their customers operate in a wide variety of industries ranging from the commercial vehicle sector, such as automotive and bus and coach manufacturers, to the leisure industry, tank manufacturing sector (sceptic and water holding tanks) and building industry (building dormers and canapés) to name but a few.
Looking for industry-leading equipment
Colorplas had some demands concerning the gel coat application equipment for their UK-based test and development facility. First of all, the company wanted to use the same or similar application equipment as their customers to emulate their production conditions when testing new products. Because they constantly develop new products such as Low Styrene Gelcoat and continuous new pigment colour shades, Colorplas asks for market-leading equipment and solutions to gain the widest possible market coverage and application relevance.
The company already had a close relationship with Graco distributor Glas-Craft, which provided expert training on equipment, on-going service and support for the test facility. Glas-Craft suggested using Graco’s FRP Gel Coat System 13:1, which delivers a consistent on-ratio mixing with smooth pulse-free deliveries and an increased production uptime. The RS Gel Coat Gun delivers an optimum cover and finish. It is lightweight, ergonomic and designed for tool-less operation with easy maintenance.
“We wanted to develop our Spray gelcoats more, so that’s why we chose Graco’s FRP system”, says Joe Parkinson. “Before we had the FRP, we followed the market, analysing other materials. Whilst now, with FRP we develop within looking at such readings Thixotrophic Index, Flexural Modulus, Tensile Strength and Viscosity to develop and test our own gelcoat. The ease of application the FRP allows speeds up this process and Benchmarking is made much simpler”.
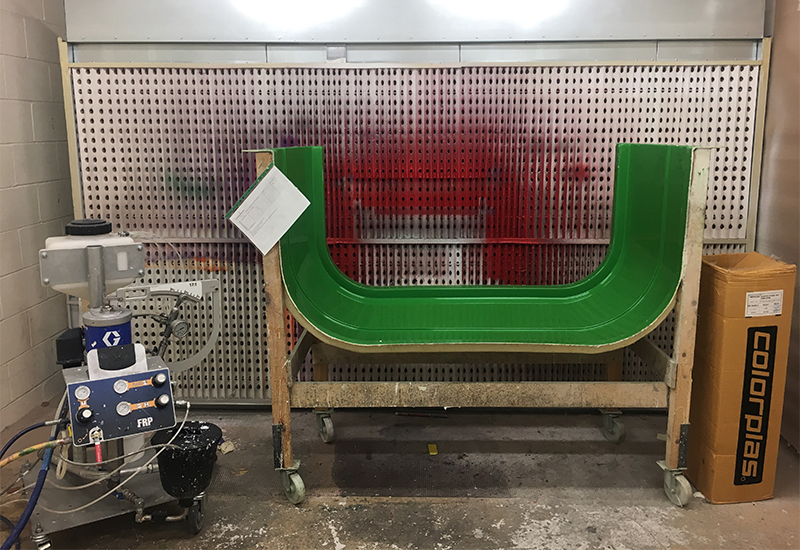
SPRAYER FOR RESEARCH & DEVELOPMENT AND TROUBLESHOOTING
Thanks to the training and a trouble-free start offered by Glas-Craft, the equipment was put to immediate use in combination with various spray Gelcoats to match customers’ requests. “The FRP is easy to use and we perceived the results very well and there’s always good fan atomization. That’s why we went down the route of purchasing it”. The gel coat sprayer is placed in an extraction unit and is fitted with water and moisture traps. It has a stand on wheels so it can be moved around in different locations within the same room. It’s equipped with two RS guns: one internal mix and one external mix gun.
“Once you have a spray machine, such as the FRP, that puts you in your customers’ shoes, you can really understand certain issues and look into ways to overcome them. Thanks to the FRP, we have an idea of what our customers are experiencing every day. And not just on a lab scale. We have a spray booth extraction just as any of our customers would do. So, anything our customers do can be mirrored exactly. We can create a like-for-like atmosphere”. Our Technical Services Department has benefited greatly from the FRP because of this replication and this allows us to solve issues speedily.
On average, Colorplas uses the FRP throughout the week every week. It can be used for a number of things, whether it’s for research and development, testing material to make improvements or troubleshooting when a customer has an issue with a gel coat. For example, if there are reporting issues with a gel coat, Colorplas can test that batch of gel coat, which they have retained back at their facility and report back with a technical audit.
USER-FRIENDLY MACHINE
The company has a stringent care plan in place to negate the unit seizing up. First, they flush grinding resin through it and then they flush it through with acetone. “It’s easy to switch from one material to another once you know how to do it. If you clean down with a good consistent method behind it,you should be fine,” says Joe Parkinson.
With the FRP, the desired spray pattern is very easy to achieve. Graco’s exclusive Air-Assist Containment (AAC) is designed to ensure that the maximum amount of material ends up where it’s wanted: on the object you are spraying. AAC creates a spray pattern in which the droplets travel to the mould at very low pressure. “To achieve atomization of the spray gel coat it’s important to have the right pressure, the right tip, and to consider three temperatures: product temperature, ambient temperature and mold temperature. As long as those three are okay, you’re half way there to get the right spray pattern and therefore a good moulding”, explains Joe Parkinson.
“The FRP has all the gages and measures able to be changed. It’s a very user friendly and easy-to-approach machine. I would say for the expert sprayer or applicator it’s easy to use”.
KEY ROLE IN DEVELOPMENT
Colorplas is now able to produce validated set-up combinations and limitations for customer reference. “Colorplas’ approach on spray gel coats has definitely been aided by the FRP. We knew that we had to research and develop in the area of spray gel and top coats and the FRP was fundamental in our approach in the market”, Parkinson concludes. The Graco equipment will play a key role in the development of new materials, particularly lower styrene products, to meet the changing regulations for lower styrene emissions over the coming years.
MORE INFORMATION
For more information about FRP systems, fill in the form below.
