Graco helps Komatsu increase productivity of paint booth
A revamped paint management system decreased overspray, reduced paint waste, accelerated cleaning of spray guns, and improved the quality of finish.
These are busy days at the Komatsu Italia Manufacturing
plant in Este, in the province of Padua. Demand for Komatsu machines – such as
excavators, backhoe loaders and skid steer loaders – has increased
significantly, pushing production at Este up from 5,000 to 7,000 machines per
year. It’s a welcome boost to the company after a slump during the pandemic.
Revamping the coating line
To meet higher production rates, it was necessary to optimize elements of the three production lines at Este. In addition, attention was focused on the coating line. Advice was sought from Comaind, the distributor of Graco paint mixing and application equipment that had already designed and installed KIM’s previous system. Together with the KIM team, Comaind conducted an in-depth study to reveal possible bottlenecks, downtimes, and paint wastage.
“Consumption of both paint product quantities used and overspray generated was analyzed,” recalls Davide Galvani, Head of Verona Unit at Comaind. “It was found that the high variety and geometrical complexity of the parts being treated was resulting in the use of a wide range of different load bars. This was leading to significant overspray.”
It was also found that coating distension could be improved, making it more uniform and increasing its degree of gloss while maintaining the same thickness and quality standards. Everything was pointing to the need to replace the dosing system to improve the top coat application phase. Moreover, the switch from acrylic to epoxy products meant that an upgraded pump was needed for primer application.
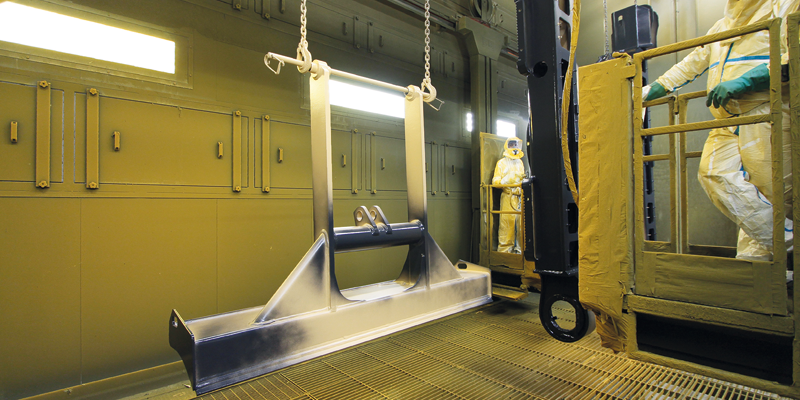
Testing Graco automatic proportioners
“We made some recommendations to KIM, who agreed on the installation of demo equipment to carry out tests,” adds Galvani. “Two Graco ProMix PD2K automatic proportioners were brought in. Thanks to their innovative mixing technology, these machines allow the coating product to be mixed close to the electrostatic gun, which reduces downtime and material waste.”
The new, unique positive pumping technology also guarantees more stable and precise pressure and flow control by moving a fixed volume of material at a constant flow and speed.
Based on the initial results, the green light was given to Comaind to install a new Graco ProMix PD dosing platform in Este.
Equipped with recirculating bypass colour change valves, the ProMix PD2K unit is set up for dosing three colours. Two of these – black grey and natural yellow – are constant, while the third is a wild-card shade. The operator inside the paint booth can select the appropriate colour(s) at the instant the machine is fed with a catalyst from the paint management unit. Pressure regulators stabilize the mixing operation.
“The PD2K dosing platform also allows colour changes to be made in the gun’s pumping part and remote mixing block,” explains Galvani. “All tints remain in the recirculation lines even if not used.” To reduce solvent and paint waste, KIM opted to install two machines, each attached to two Graco ProX XP 85 kW handguns.
Equipped with recirculating bypass colour change valves, the ProMix PD2K unit is set up for dosing three colours. Two of these – black grey and natural yellow – are constant, while the third is a wild-card shade. The operator inside the paint booth can select the appropriate colour(s) at the instant the machine is fed with a catalyst from the paint management unit. Pressure regulators stabilize the mixing operation.
“The PD2K dosing platform also allows colour changes to be made in the gun’s pumping part and remote mixing block,” explains Galvani. “All tints remain in the recirculation lines even if not used.” To reduce solvent and paint waste, KIM opted to install two machines, each attached to two Graco ProX XP 85 kW handguns.
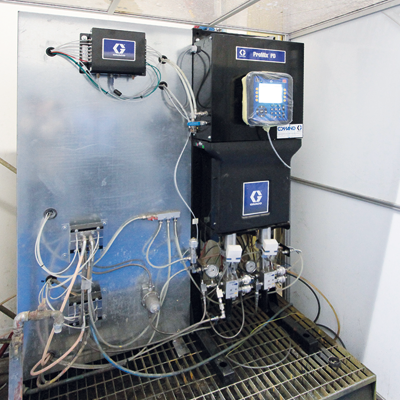
Wide-ranging tangible benefits
The benefits were immediately noticeable and highly significant. ”The new equipment works at lower pressures, so painting occurs in a more targeted way, while still respecting the plant’s takt time,” explains Galvani. “This reduced overspray by 30%, which of course significantly reduced waste and increased profitability.”
Another notable advantage concerns the cleaning of the spray guns. With the previous system, when non-standard requests needed to be handled, gun cleaning would require frequent interventions. These would take a long time and require large quantities of solvent. Now, the reduction in the length of the pipes means that gun cleaning is a much faster process, typically only a few minutes.
“Operators also appreciate the compact and easy-to-use in-booth control interface,” adds Galvani. “It offers a safe way to control programs, pressure values, and colour change operations – all from within the spray booth.”
Automotive-level finishes on excavators
Ultimate top-coat quality also improved. Operators were delighted to find that the new atomization technology with low-pressure air helped them more easily find the optimal application speed. This in turn enabled them to achieve higher quality coating results than those normally expected of construction machines; almost comparable to automotive-level finishes.
Management at Komatsu Italia Manufacturing in Este is also pleased with the new Graco system. It has reduced paint waste, helping the company meet its sustainability objectives. It has reduced solvent usage and emissions, further improving the health and safety of the working environment. And it has improved the aesthetic quality of Komatsu machines. Finally, by replacing the acrylic primer with an epoxy product, the machines now offer increased salt spray resistance.
“KIM has been following us for many years,” confirms Marco Caporello, Key Account Manager, Industrial Division EMEA, Graco, “Our cooperation is based on a mutual exchange. We offer Komatsu the latest innovations, and they open their factory doors for us to test them. Very often, as was the case with the new PD2K dosing system, Komatsu decides to immediately invest in the new technology and integrate it into its coating line.”
More information
Would you like to know how the Graco ProMix PD2K automatic proportioner can bring similar benefits to your paint shop? Check out the product webpages or fill in the form below to discuss your specific requirements or even set up a product demonstration in your plant.

Related Articles
Choosing the right setup: ProMix PD manual technology
Create the perfect working conditions for your operators with Graco’s ProMix PD manual proportioning system for plural-component mixing.
ProMix PD: a closer look at the colour changing process
A brief analysis of the unique colour changing process of Graco's ProMix PD proportioning system for plural-component mixing.
ProMix PD proportioner: a closer look at the flushing process
A brief analysis of the unique flushing process of Graco's ProMix PD proportioning system for plural-component mixing.