How to reduce cleaning of your hot melt system
A tank-free system like InvisiPac reduces the cleaning time and expense of your hot melt system
A hot melt system quickly and consistently delivers adhesive at the right temperature and viscosity to enable a packaging line to run smoothly and efficiently. Unfortunately, a hot melt system needs regular cleaning, which leads to production line downtime.
A blocked nozzle is one of the most common problems, leading to production line downtime, long nozzle cleaning times, safety issues, and ultimately reduced productivity and profitability.
The core problem: char in the tank
At the heart of problems around blocked nozzles is char. This is induced by components which are in use for lengthy periods, such as the applicators and hoses. However, most often the source of char formation is the system itself.
Traditionally, hot melt dispensing systems are equipped with tanks in which adhesives are heated to high temperature for hours or days at a time. These long heat soaks lead to adhesive charring; the overheating and burning of adhesives. When adhesive chars, it results in hard clumps that have lost their thermoplastic nature. These clumps stick to the walls or top of the tank.
Char cleaning
Char causes nozzle blocking and line stops, which lead to increased maintenance. The charred material needs to be removed from the tank, so that production doesn’t fall behind. Unfortunately, removing char can take hours. Just scraping it and reheating it can take two hours, leading to decreased productivity and profitability of your hot melt system.
Char removal safety issues
There are also safety issues related to char removal. To get the line up and running as quickly as possible, char is frequently removed by equipment maintenance and system purges when the material is still at a high temperature – thereby increasing the risk of a major burn. This risk is increased if operators or maintenance engineers don’t wear appropriate heat resistant PPE during these maintenance-related jobs. In addition, hot and charring adhesive releases unpleasantly smelling and toxic fumes which can affect an operator’s breathing.
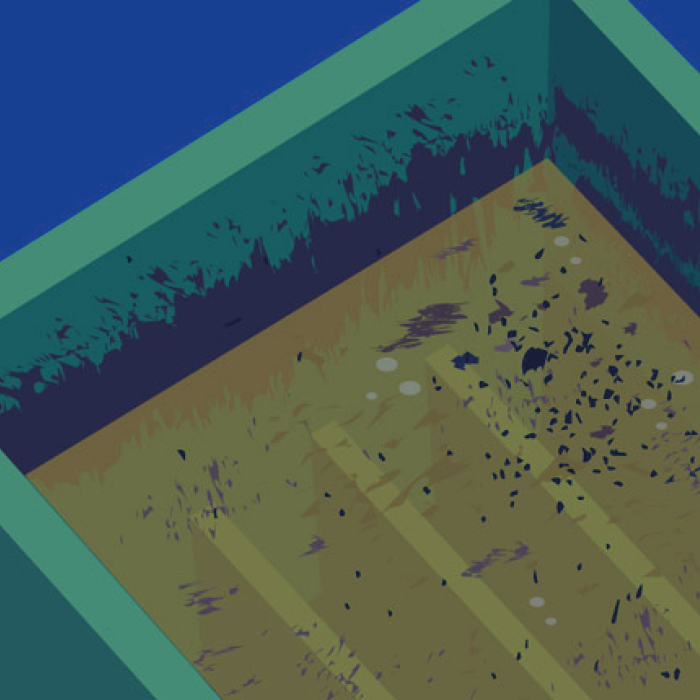
The solution: use a tank-free system!
Simply put, if you don’t have a tank, you don’t get char. This is because a tank-free, melt-on-demand system like Graco’s InvisiPac only heats a small part of the material and only when it’s needed (initially 500 grams but then significantly less due to the First In First Out principle). By not heating more material than needed, the material will never overheat or burn, thereby eliminating charring and nozzle plugging, and reducing maintenance requirements.
A tank-free system like InvisiPac significantly reduces the cleaning time and expense of your hot melt system. And with no large volume of high temperature melted glue accessible to personnel, the health and safety benefits for operators are considerable. Contact our hot melt experts at Graco in the form below for more information.
Related articles
How to reduce the maintenance costs of your packaging line
Discover the benefits of switching from a tank-based system to a tank-free system
Summit Brewing: Packaging line success story
New packaging technology helps Summit Brewing improve their production efficiency.
Why InvisiPac is the reliable option for your packaging line?
An InvisiPac tank-free hot melt glue system with melt-on-demand process avoids charring and nozzle blocking.