Painting agricultural vehicle engines
Graco equipment is playing a key role in a new automatic engine coating line at MANTA Group’s plant in Italy.
MANTA Group, based in Foggia, Italy, has been focusing on the assembly and coating of aerospace and automotive components for over 30 years. In 2021, the company was entrusted with the painting of agricultural machine engines. To accomplish this task, MANTA identified a pool of suppliers to build a fully digital, Industry 4.0 compliant, automated, flexible and fast painting line.
The objectives for the new coating line were challenging. It would have to enable the painting of more than 700 engine variants in four different colours, with a capacity of 85,000 engines per year. It also had to be fully digitally integrated with the company’s management system to enable close monitoring of each coating stage and the fulfilment of quality requirements.
Gaiotto, Savim and CM Automazione were involved in the plant engineering aspects, and Graco was given responsibility for the paint application. The water-based single-coat paint system to be applied to the engines was validated by an external laboratory (CRF) before the start of production.
Smooth cooperators
The painting plant was built by Savim (Arbizzano, Verona, Italy), equipped with Gaiotto robots, and integrates an XD45/59 step-by-step conveyor designed and provided by CM Automazione (Giussano, Monza e Brianza, Italy). The line accommodates up to 116 handling units with a maximum load capacity of 850 kg each. At full throughput, the line is capable of painting 370 engines per day.
For the paint feed supply, paint application equipment and the colour change system, MANTA relied on Graco and its integrator Comaind (San Giovanni Lupatoto, Verona, Italy), whose collaboration was fundamental in one of the most critical phases of this project.
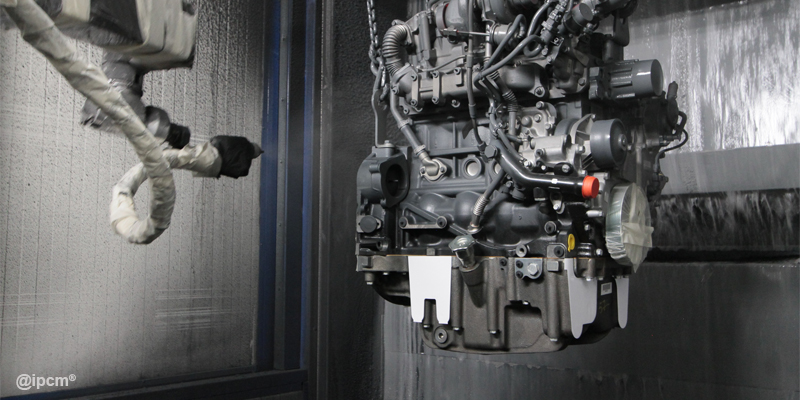
A streamlined process
Each engine passes through a number of preparation stages: masking, chemical pre-treatment with phospho-degreasing, cleaning with demineralized water, and drying in three steps (pre-drying tunnel, robotic blow-off, an oven at 90°C) before the engines pass through a cooling area.
The liquid paint is then applied in two pressurized, temperature- and humidity-controlled water curtain booths, supplied by Savim, each with a Gaiotto articulated robot rotating 180° that paints one side of the engine. The minimum thickness applied is 50 microns. A third manual booth is used for touch-ups. The line ends with a flash-off tunnel and an oven that accommodates 50 engines at 100°C for 90 minutes. The engines then proceed to an in-line quality gate for final approval.
The paint application system
“We designed the paint feeding and application system together with Gaiotto to handle the four colors applied by MANTA,” explains Davide Galvani of Comaind. “The most used one is grey, which accounts for almost 90% of the production. The other three colors are yellow, Perkins grey, and transparent, which take up the remaining 10% of the volumes.”
Coating planning is not done on a batch basis but by individual engines. This meant designing a very quick colour change system of only 30 seconds. The paint management unit is equipped with a 1000 kg container for the grey colour and 200-litre drums for the other tints. The paint is kept agitated by an ATEX-certified electric agitator with expandable vanes and a refill system linked to a 100-litre tank where a Graco Endura-Flo pump circulates the paint at a pressure of 2.5-3 bar. This tank pre-feeds the Graco PD1K plural-component proportioner equipped with four separate pumps, one for each colour, to guarantee maximum colour change speed on board the robot.
In addition, 60-mesh filtration is performed on the recirculated product. The PD1K device also has its own filtration unit at the gun’s outlet. The two coating robots are equipped with two automatic Graco AirPro compliant-technology guns each. One gun handles grey paint, whereas the other is fed by colour change valves positioned about 40-50 cm from the gun, almost on the robot’s wrist; one valve is for flushing the circuit, and the other three are for the tints. The paint management unit also pre-feeds the touch-up booth where a gun is available for each colour that is activated with the correct colour depending on the incoming engine.
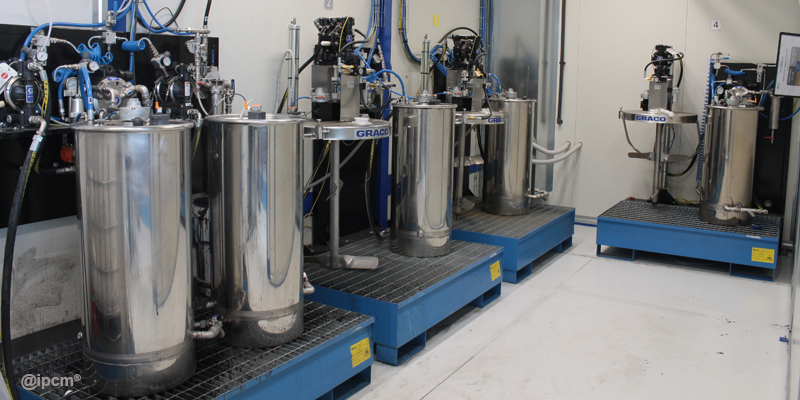
Graco’s PD1K at the heart of the system
“We selected the Graco PD1K plural-component proportioner as it enables the paint flow to be directly controlled at the gun and adjusted according to the movement of the robot during the painting stage,” adds Galvani. “This unit also allows analysis of the technical/production parameters and interfaces with the line’s 4.0 system.”
Thanks to its unique encoder-based piston drive technology and active control valves, the PD1K provides a mixing ratio accuracy within 1%, ensuring smooth and exact dispensing every time. It maintains this exceptional accuracy regardless of head pressure, elevation, material viscosity, temperature or gun triggering.
Moreover, by moving the mixing point closer to the gun, it decreases the flush zone. This translates into less material waste, faster flushing and increased efficiency. Full flushing can be programmed in the unit’s Advanced Display Module, with the option to preset up to five different flushing recipes with individual solvents, time schedules and other factors.
Also of interest to MANTA is the cost-effectiveness of the PD1K, thanks to impeccable flow control, quick color changes, and efficient dispensing. Its unique flushing method reduces solvent use and material waste by up to 80% and the cost of maintenance is significantly lower compared to gear pumps, making it a budget-friendly option for the MANTA painting line.
The device is perfectly suited for manual or automatic applications. It’s capable of operating up to four pumps, dispensing different chemistries, and tracking pot life for up to three spray guns on one single system. Up to 30 colours can be managed in 1K to 4K setups, and it’s possible to combine typically separated materials like epoxy and urethane or waterborne and solvent-borne paint.
Up and running at high-quality
The line started in full production mode at the end of 2022. The start-up phase involved a learning process, especially as water-based paint is much more liquid than its solvent-based equivalent. Initially, some manual retouching was required because the robots’ painting programs were not fully optimized. When these were adjusted, the manual work necessary was progressively reduced.
MANTA – and their customers – are impressed at the high-quality of the paintwork on the engines, thanks partly to the quality and technological content of Graco’s systems.
The bigger picture of this engine painting line
The new painting plant and fully automated engine painting line are the results of experts joining forces. They combine the expertise of Gaiotto, Savim, CM Automazione, Comaind and Graco.
The line consists of different stations. Our paint feeding and application system, being one of them. Let’s have a closer look at the bigger picture, with each number representing a separate station.
- The masking station. To protect sensitive surface areas against water ingress during the pre-treatment
- 3-stage chemical pre-treatment with phosphide greasing, cleaning with demineralised water.
- Pre-drying tunnel. The first step of the drying process.
- Robotic blow-off. To remove any cleaning water remaining inside the holes.
- Oven at 90 °C. The third and final step of the drying process.
- Cooling area.
- Masking phase 2. About 100 masking devices are applied.
The cycle proceeds with the application of the liquid paint in two pressurized, temperature and humidity-controlled water curtain booths. The minimum thickness applied is 50 microns.
A third manual booth is used for touch-ups.
The engine painting line ends with a flash-off tunnel and an oven that accommodates 50 engines at 100 °C for 1 hour and 30 minutes
For more information about Graco’s PD1K system, fill in the form below.
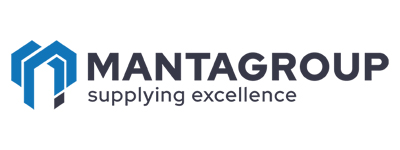
Related Articles
John Deere factory in Mannheim installs Graco 2KS paint supply system
To meet stringent quality standards and increase process reliability, the John Deere factory in Mannheim has invested in a new Graco paint supply system.
Manual processes are a thing of the past: automation for increased productivity
Learn how the Graco AirPro spray guns work well with your automation process.
Optimally coating gearboxes for self-propelled machines
Graco’s ProMix Easy, ProMix 2KS proportioners, G40 and AirPro spray guns are proving their value at Bonfiglioli’s gearbox manufacturing plant in Forli, Italy