John Deere factory in Mannheim installs Graco 2KS paint supply system
To meet stringent quality standards and increase process reliability, the John Deere factory in Mannheim has invested in a new Graco paint supply system.
The familiar and striking colour combination of dark green with yellow wheel rims makes John Deere’s agricultural machinery easily recognizable at a distance. But they are not the only colours used. These vehicles can also be painted in orange – favoured by cities and towns – or in special colours like yellow and white to meet specific customer requirements.
The John Deere factory in Mannheim, Germany turns out over 20 different models in numerous versions and configurations at a rate of 200 machines per day.
After zinc phosphate treatment, the drives, frames and small parts are given a prime layer of epoxy-based cathodic electrodeposition (CED) coating, after which the top coat is applied. A 2K PUR high solids coating is used, applied on a production line both by robots and manually.
Highest quality standards
The surface quality requirements for the machines are now nearly as high as in the automotive industry. To meet these high standards even more comprehensively, in late 2016 the John Deere factory in Mannheim decided to invest in a new paint system. Their goals were to boost process reliability and reduce maintenance. Their current Graco equipment had been in constant use since 2005, and although the Graco machines had performed excellently, they were beginning to show signs of wear and tear.
John Deere managers, along with paint suppliers Gross & Perthun, took advantage of last year’s PaintExpo to get quotations for more modern systems. In the end they gave the nod for the conversion to L&S Oberflächentechnik, a system provider for surface and application technology, material provision and automation.
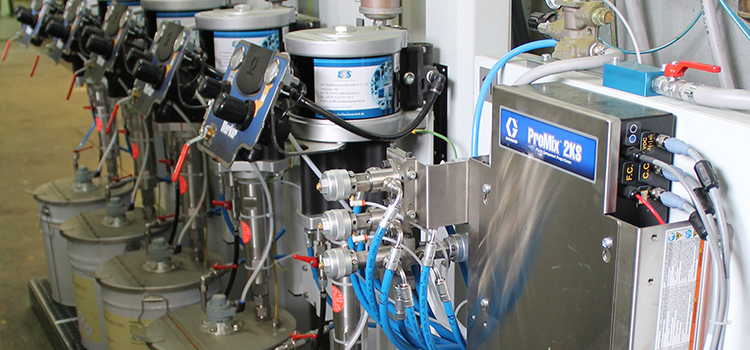
Number of systems reduced from 16 to 12
Incorporating tinting in the new supply system allowed the number of units to be reduced from 16 to 12. Where previously only one stock coating and one hardener could be processed, it is now possible to run up to 30 stock coatings. This makes it easier to apply the paint, the mixing is better and the coating is cleaner.
The systems also support remote queries and can therefore be accessed from a PC, so they can be managed directly by L&S in eastern Westphalia or by paint manufacturer Gross & Perthun in Mannheim. This system integration also clears the way for Industry 4.0 in paint shops. In addition, it is now possible to measure paint quantities and application times, which boosts cost-effectiveness and quality and enables targeted training of new employees.
Installation over three weeks
During the one-week company break at the Mannheim factory in October 2016 and in the two weeks afterwards, L&S installed 12 new Graco 2KS systems. The 2KS mixing and dispensing system is suitable for manual and automatic applications and can process up to 30 stock coatings and four hardeners. It works with both high and low pressure and allows sequential and dynamic dispensing. It also has a programmable rinsing sequence and extended reporting functionality to save and manage all of the system’s process and operating parameters. This makes it easier, for example, to record costs and ensure compliance with quality requirements for each individual component. The Graco 2KS provides maximum accuracy for the mixing ratio and feedback on critical process variables, and it has built-in system safety.
In addition to the 12 stationary units installed in the factory, a mobile Graco ProMix II model enables John Deere to cope with any unexpected outage. This unit is designed exclusively for manual applications, can process up to three tints, and is equipped with USB reporting capability. It means that in the event of an outage, normal operations can be resumed in the shortest possible time, without interrupting the production flow any longer than necessary.
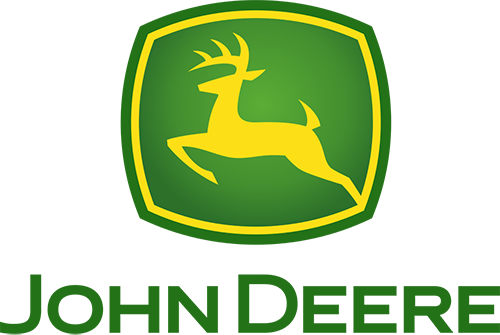
Maintenance intervals significantly extended
The benefits of the new technology are readily apparent: while the old system needed maintenance on at least a monthly basis, this has now dropped to once every three months. The mixing chamber is no longer necessary because the new devices have a completely different injection and rinsing concept, leading to enormous savings on materials. Bad mixes are now impossible, eliminating the need for rework. The volume of costly compressed air has also been reduced considerably.
The Merkur pumps in the central paint supply system, also made by Graco, have also been updated. There are five pump stations on the solo cabin and three pump stations on the mobile 2K system. The gun rinsing stations were also updated, and new gun rinsing stations were integrated for the application equipment to ensure monitored, error-free and safe rinsing. In future, L&S Oberflächentechnik will take over technical service in Mannheim.
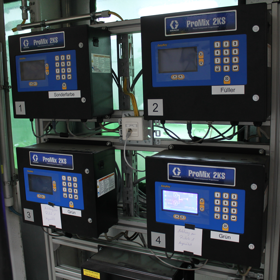
More information
For more details on Graco’s 2KS systems and Merkur pumps, fill out the contact form below.
Related Articles
Seat upgrades paint shop with Graco electric pumps
Car manufacturer Seat installs Graco’s new electric paint circulation pumps in the paint mixing shop at their plant in Martorell, Spain.
The smart way to mix paint
Graco ProMix PD2K paint mixing machines play a key role in the digitalization of painting lines at Pieffeci Turin
Optimally coating gearboxes for self-propelled machines
Graco’s ProMix Easy, ProMix 2KS proportioners, G40 and AirPro spray guns are proving their value at Bonfiglioli’s gearbox manufacturing plant in Forli, Italy