Seat upgrades paint shop with Graco electric pumps
Car manufacturer Seat installs Graco’s new electric paint circulation pumps in the paint mixing shop at their plant in Martorell, Spain.
The Seat factory in Martorell, 30 km from Barcelona, is one of the most advanced automotive manufacturing sites in the world. For example, it has more solar panels than another car manufacturing facility anywhere. The site encompasses 15 buildings and covers a total area of nearly 3 million square meters (the equivalent of 400 football fields), of which about 260,000 square meters are given over to green space.
Around 7,000 employees work here. Three shifts throughout the week produce the Seat Ibiza, Leon and Arona, and the Audi A1. Current daily production at the plant is around 2,100 units, which are then sold in 75 countries. The painting process for these models takes place in two workshops. An anti-corrosion surface primer is applied in one hall. In the second hall, robots apply the top coats and varnish.
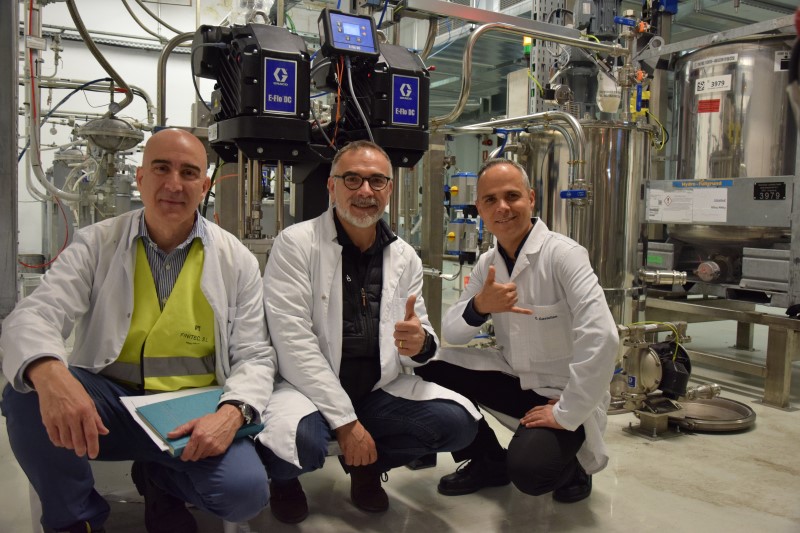
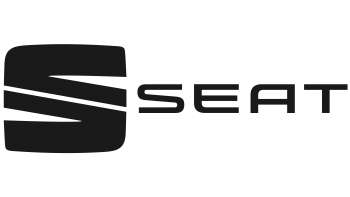
Emissions down; productivity up
Seat is committed to environmental protection and sustainability. Part of this entails reducing emissions of volatile organic compounds (VOCs) during the painting process. Consequently, the workshops are equipped with the most environmentally-friendly technology, and solvent-based primers have been replaced with water-based primers. As part of the transition to a greener paint shop process, it was time to upgrade the paint circulation pumps to more efficient models.
Almost a decade ago, seven Graco E-Flo Plus electric paint circulation pumps were installed in the paint mixing shop. With the switch from a solvent-based primer to a water-based one, it was time to upgrade to the successor model, E-Flo DC 4-Ball. The seven new pumps promise greater efficiency as they require less energy and will also enable improved process monitoring. The E-Flo DC 4-Ball pumps are suitable for all materials – especially metallic paints – and do not damage the paint, which means that the color is consistent.
These electric circulation pumps with brushless DC motors promise five times greater efficiency compared to pneumatic pumps, which will lead to significant energy savings. The reason is that the motor allows more precise control over torque and speed, allowing the pump to respond more quickly to changes in system load.
The E-Flo DC 4-Ball pumps can be set to maintain either a constant flow rate or a constant pressure of up to 17 bar, both of which can be regulated according to set targets through continuous monitoring. Seat uses constant pressure mode as it provides greater control over variations in the painting process. Constant flow mode is more suited to smaller applications with a known flow rate.
Saving energy and reducing maintenance
Another useful feature of the pump is its sleep mode, which enables paint that is not actually needed to circulate at a lower pressure – again, saving energy. When the paint is needed, the pump builds up to its normal operating pressure within a few seconds.
That’s not all. Whereas conventional pumps are usually operated and regulated together, E-Flo DC 4-Ball pumps work independently. The advantage of this feature is that individual pumps can adapt to varying pressure and flow requirements several times a second, reducing pressure fluctuations to a minimum. It also means that production can continue during maintenance work, further reducing downtime. Electric paint pumps are inherently low in maintenance anyway, requiring just one oil change every year.
Finally, the pumps can be controlled and selected using a PLC and are continuously monitored from a monitor next to the pump. The data is collated in the line control center, and passed on to Seat central control, where management have full and continuous control of the painting process.
The E-Flo DC 4-Ball pumps are not the only equipment displaying a Graco logo at Martorell. Seat also employs the Husky 15120 air-operated polypropylene double diaphragm pump as lower pump. This has a stall-free, low-pulse air valve, allowing smooth and rapid changeover of paint. Its single-piece center section is leak-free and is low on maintenance compared to similar diaphragm pumps; only the bellows need changing, every two years. In addition, the Graco Endura-Flo 4D 350 high-pressure diaphragm pump is used to flush the solvent lines.
The use of these Graco pumps is helping Seat meet its strict environmental standards and operate its paint shops as efficiently and productively as possible.
For more information about Graco's industrial finishing and automotive solutions, fill out the contact form below.
Related Articles
John Deere factory in Mannheim installs Graco 2KS paint supply system
To meet stringent quality standards and increase process reliability, the John Deere factory in Mannheim has invested in a new Graco paint supply system.
Large capacity pump strengthens auto assembly line
A large automotive plant eliminated air motor icing and leaky lowers in the paint kitchen to increase productivity.
Sealed-4-Ball lowers withstand harsh materials
One of the world’s most innovative automotive manufacturers updated their pumps to work with their new coating.