Nissan optimizes paint room operations
Graco’s ProMix PD2K helps Nissan St. Petersburg improve paint quality, increase efficiency, and reduce downtime
On the northern outskirts of St. Petersburg, Russia, in the municipal settlement of Pargolovo, Nissan operates one of its highest quality factories globally. Established in 2009 on an area of 60,000 square meters, 1,500 people work at the plant to produce the Nissan Qashqai, Nissan X-Trail and Nissan Murano. The plant’s production capacity is 100,000 cars per year.
Not surprisingly, top-quality paintwork is a priority. To raise the bar still further, Nissan decided to increase the durability of the paint applied to its cars in St. Petersburg. This involved changing the clear-coat painting line from one-component to two-component (2K). Also called plural component paint, 2K involves a resin and a catalyst that are mixed together in a certain ratio to start a reaction.
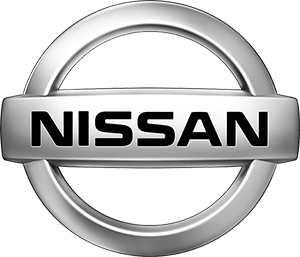
The benefits of 2K
Compared to single-component paint, plural component paint displays improved durability. It has a higher mechanical strength which allows it to withstand abusive conditions better than other paints. It also has better chemical resistance, so can better withstand exposure to a wide range of abrasive chemicals. 2K paint is therefore being increasingly applied by automotive manufacturers.
Plural component paint demonstrates increased flexibility. This means that painted polymeric substrates such as a car bumper are less likely to crack on impact. Another benefit is that less energy is required to cure the paint. Ovens can therefore be run at lower temperatures, which reduces cost. Faster cure times are possible with plural component paints, and curing is much easier to control.
Increasingly important these days, especially with companies keen to enhance their green credentials, are the environmental benefits of plural component paint due to lower VOC’s because there’s no necessity to evaporate solvent. Finally, plural component paints can have a higher solid content, which leads to better surface coverage.
The challenges of 2K
However, 2K isn’t free from its challenges. The 2K mixing process requires constant monitoring. Moreover, to ensure the specified characteristics, the mixture must always be fresh.
In St. Petersburg, another challenge was that two different types of clear coat had to be used on one line. At first sight this might not seem problematic, but remember that the cars are constantly moving along the conveyor line; the right paint must be ready instantaneously when needed. A further potential bottleneck in the process is that although most of the painting is done by robots, the door openings and trunk of each car are painted manually.
Furthermore, management at St. Petersburg was keen to reduce the effect of the production process on the environment. VOC emissions as well as paint waste had to be reduced to the absolute minimum.
Call in the paint-shop experts
To get some help navigating through these often conflicting requirements, Nissan sought the advice of paint-shop specialists from Graco. After visiting the factory and talking with management and engineers, Graco’s specialists went away to work out what was the best equipment and configuration to use for the task at hand. They recommended the Graco ProMix PD2K, the company’s most advanced 2K mixing and spraying technology to date.
Graco’s 2K proportioner ProMix PD2K is based on unique technology of electrically powered and controlled positive displacement dosing pumps. The use of 100% positive displacement technology allows accurate mix ratios (within 1%) and consistent performance. It’s particularly ideal for short pot life materials, as the ProMix PD2K mixes the material close to the gun so the flush zone is significantly smaller. This allows for faster color changes, less material usage, and reduced disposal costs. In fact, up to 80% reduction in flushing waste is possible compared to the most efficient traditional proportioning systems. It also stalls under pressure for consistent, on-ratio results, and is field serviceable in less than 20 minutes, which means there’s no need for costly factory rebuilds like gear pumps.
Complete control with minimal waste
One of the key reasons why Graco recommended PD2K is its inherent modularity. This allows it to be configured – or even customized – directly to meet the specific requirements of the application. In this case, the unit was equipped with four dosing pumps controlled by one control module. This approach made it possible to use two types of clear coat separately and independently from each other.
As to implementation, the control panel of the unit and special flushing boxes are installed in the spray booth, where the spray gun is placed when it is not used by the operator or when it needs flushing. Once the operator at the control panel asks for the material they want, it is ready to spray in less than 15 seconds. This has the significant advantage that the material does not have to be kept ready in a mixed state. As soon as the operator sees that he needs more material, he simply presses a button on the remote control panel and in a matter of seconds he can start painting.
This has an important knock-on effect. As the material is mixed in the immediate vicinity of the spray gun, this reduces the quantity of solvent required to flush the system, thereby reducing environmental emissions. And since the system automatically maintains the preset paint pressure, it is possible to reduce paint waste during the painting process.
Data logging reduces maintenance
The benefits of the PD2K extend long after the paint has dried. During its operation, the Graco system collects and stores a wealth of data on the material used. It links paint usage to specific operators, and monitors all events that occur during the mixing process. It logs and reports operational errors and sends reminders of planned maintenance.
Despite the fact that the proposed configuration is intended for manual operation, Nissan engineers immediately indicated the need to connect the PD2K to the factory PLC to collect and analyze all the data. This was implemented via a pre-selected communication protocol. As a result, plant management can receive complete information about the mixing and painting process from a remote location. They can see in real time all the parameters used by the system, keep records, and timely track and prevent possible errors.
That’s not all. To ensure consistently high mixing quality and trouble-free operation, the Graco PD2K system regularly self-diagnoses for problems, and immediately notifies personnel if any action is necessary. Finally, customizable maintenance notifications improve the efficiency of regular service and avoid unexpected downtime.
All in all, Nissan management is delighted with the significant benefits of higher paint quality, improved operational efficiency, reduced maintenance, and less waste thanks to the implementation of the Graco PD2K at the St. Petersburg factory.
More information
For more information about Graco's automotive solutions and ProMix PD2K, fill in the form below.
Related Articles
The smart way to mix paint
Graco ProMix PD2K paint mixing machines play a key role in the digitalization of painting lines at Pieffeci Turin
Automotive Tier 1 Supplier Accomplishes More with Less Equipment
ProMix PD enables a paint line to do the work of eight robots with only four.