Stricter regulations and improved competitiveness, it is possible!
AJK is a mid-sized Belgian company, specialised in the production and sale of rubbish containers, presses and other, in the disposal and transportation sector used products.
Since the products continuously are exposed to all weather conditions and are used to contain products that can easily damage them, the containers need to have an excellent finishing quality.
Old method
AJK used to apply a one-component material, which was supplied in 20-litre cans. The operators would add 2 litres of solvent and transport the material to their spray booths to paint the products. Since the paint, out of security considerations, was stored in a separate building, this meant a substantial loss in spraying time. Application of the paint (both primer and customer colour) was done in 5 separate spray booths, by means of separate President pumps, with Electrostatic 4500 AA guns. These installations, obviously, worked independently from each other, complicating the achievement of consistent finishing quality. Towards the customer, the standard offering was a one-component finish; two-component and high-gloss options were charged separately.
New method
AJK set itself as a target to not only meet the VOC regulations but also to improve the competitive offering to its customers. To that effect, a central pump room was installed, with 2 Xtreme pumps on 300-litre vats, with agitators and an alarm that indicates when 100-litre is left. To apply the material, 5 ProMix II colour change units were purchased with Electrostatic PRO XS4 guns. The existing 5 President pumps were kept for use with customer-specific colours. The pump room was installed in an easily accessible area in the production hall, for frequent replenishment. The ProMix II fluid panels and the operator controls have been placed in a protective cupboard in the spray cabins so that they will remain clean. In cooperation with the paint manufacturer, it was decided to change to a new, two-component high-gloss paint and a new primer, both using the same catalyst. The paint, which no longer needs to be pre-mixed, is delivered in 10-litre cans.
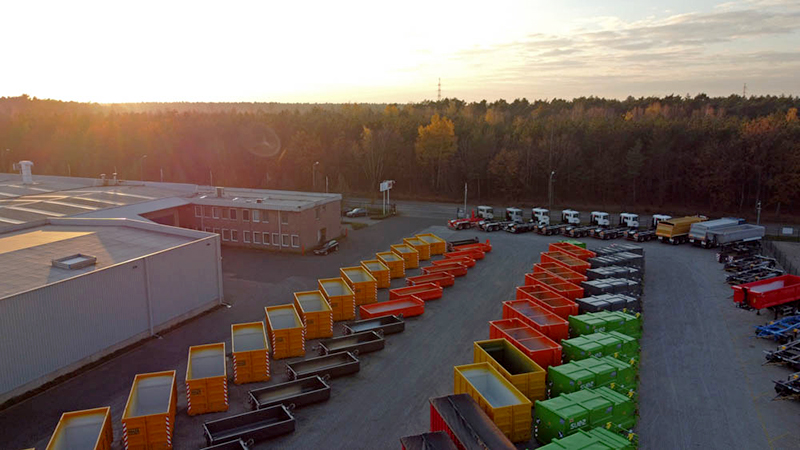
RESULTS IMPROVEMENTS
Results Internal improvements:
- Reduced material: the use of paint has been reduced by 60%;
- Reduced waste disposal costs: because of the reduction in materials used;
- Productivity improvement: thanks to the central paint distribution, an estimated 20% productivity improvement were reached;
- Reduced material on stock: due to the use of the same catalyst and two-component material;
- Improved material coverage in corners: because of the high percentage of solid particles, the electrostatic effect is increased;
- Thicker paint layer: instead of around 70 microns, 110 microns of dry material remains on the products; • Improved output: the products can be processed further quicker thanks to faster drying times.
Results External improvements:
- Customer offer: standard offer now is 2-component finishing, whereas the competition offers one-component;
- Improved resistance: against damage;
- Representative product: the products have a higher gloss, which remains longer.
Director Gunter Janssen says: ”We are very satisfied with the results: both internal procedures and our product offering to our customers have strongly improved. We are ready for the future.”
More information
For more information about ProMix proportioners or electrostatic guns, fill in the form below.
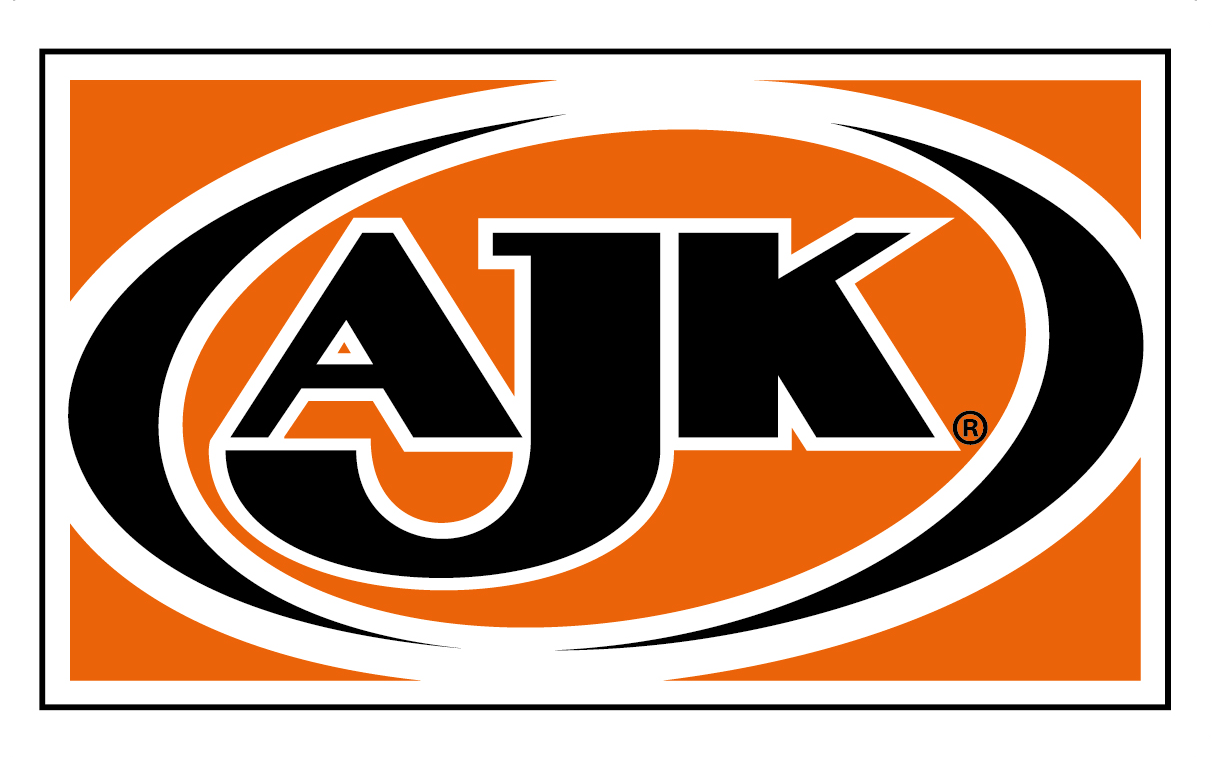
Related Articles
3 steps to VOC reduction in industrial painting
With three simple steps manufacturers can reduce their VOC emissions and avoid legal penalties.
Agrikon paintshop goes electrostatic
Hungarian heavy machinery cabin manufacturer selects Graco electrostatic sprayers to increase efficiency in paintshop
Optimizing spraying results with electrostatic paint sprayer guns
To get the full advantages of electrostatic paint sprayer guns, you must understand how they work and which coatings to apply.