Automated paint spray system configurations
Select the best-suited automatic painting machine configuration for your specific application.
Once you have calculated the value of automation on your paint line, the next step is to select the best-suited paint spray system configuration for your specific application. There are five basic industrial paint automation configurations.
Choosing the right automated paint systems configuration is important for the productivity, flexibility and cost-effectiveness of your paint line. Each configuration has its advantages and disadvantages. Understanding them is the first step in determining the best paint automation configuration for your application.
Single station
A single station can be semi-automatic, automatic or robotic, and is primarily used for operations that are difficult to accomplish manually. A single station can be simple and low-cost and offer good uptime, but it only automates a small number of operations and often requires additional material handling and manual labour.
Advantages
- Simple
- Low cost
- High uptime
Disadvantages
- Only automates a small number of operations
- Requires additional manual labour
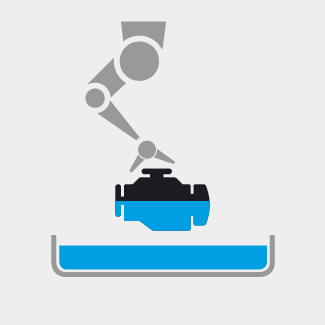
Continuous machines
Continuous machines operate without stopping and perform by moving with the work piece. Continuous machines lend themselves to very high volumes and are mostly dedicated to a particular part. They are durable and quiet, but are fairly complex, which is reflected in their price.
Advantages
- Suited to very high volumes
- Durable
- Quiet
Disadvantages
- Complex
- High cost
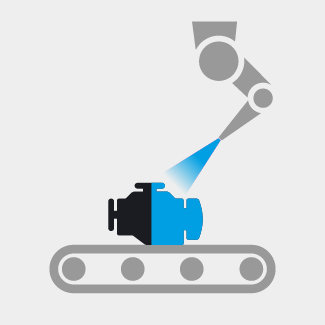
Synchronous machines
Synchronous machines utilise a mechanism by which all work pieces are moved together to sequential workstations. They are often preferred when automating relatively high volumes with little changeover or with large lot sizes. They offer a relatively low cost with high speed and the possibility to increase throughput through multiple tooling. However, production is limited to the slowest operation in the sequence.
Advantages
- Low cost
- High accuracy
- High speed
- Increased throughput due to multiple tooling
Disadvantages
- Production is limited to slowest operation
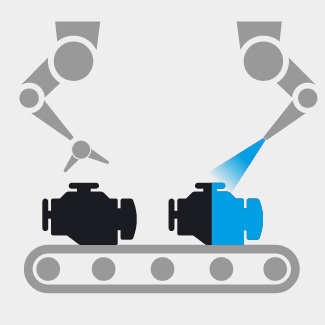
Non-synchronous machines
Non-synchronous machines use individual workstations that operate independently. They are more suited to higher-mix, lower-volume automation projects and the production rate is generally slower than synchronous. However, the throughput can be increased by using multiple parts per pallet combined with multiple tooling. Uptime is usually higher than the synchronous alternative due to the independent workstations and these machines often incorporate programmable changeover in order to accommodate high mix. A key advantage of non-synchronous machines is flexibility; the equipment is modular so stations can be added, removed or rearranged.
Advantages
- Suited to mixed automation projects
- High flexibility due to equipment modularity
- High uptime
Disadvantages
- Low volume
- Low speed and low throughput
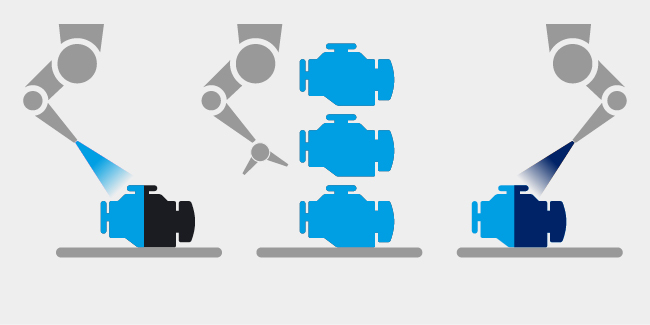
Hybrid industrial automation systems
Hybrid industrial automation systems combine synchronous and non-synchronous machines. With this arrangement, the high speed, throughput and accuracy of a synchronous system can be combined with the flexibility and high uptime of a non-synchronous system. The disadvantages are that this is usually the most expensive solution and it has a large system footprint.
Advantages
- High speed
- High throughput
- High accuracy
- High flexibility
- High uptime
Disadvantages
- Very expensive
- Large system footprint
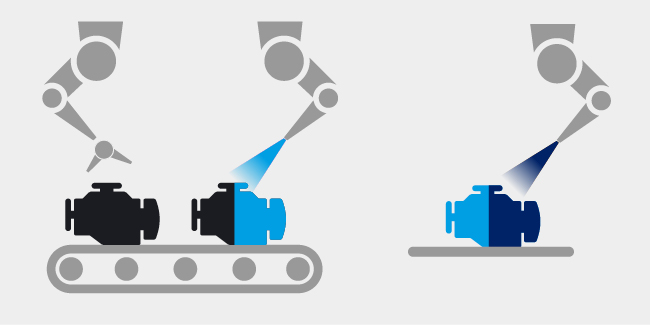
Related Articles
5 significant advantages of robot painting
The advantages of automated painting: reduce costs and waste and improve flexibility and quality.
3 steps to VOC reduction in industrial painting
With three simple steps manufacturers can reduce their VOC emissions and avoid legal penalties.
How to make your paint room Industry 4.0 ready
Make your paint mixing room Industry 4.0 ready by adding advanced control and interconnectivity.