Precisely monitor your hot melt adhesive dispense
With Graco’s Adhesive Tracking Technology you can easily monitor your hot melt adhesive consumption
Do you know how many grams of adhesive your packaging line is using? Can you track if the same amount of hot melt has been used on all your boxes during a complete production run? No? Bear in mind that if you don’t know how much you are using, you don’t know how much you are wasting.
Such data is not easy to collect with a traditional hot melt system. Only a few hot melt systems currently on the market give you real-time adhesive consumption data. Thankfully, Graco offers one. And it works amazingly simply.
InvisiPac hot melt system indicates abnormal material usage
Thanks to its advanced controls Graco’s InvisiPac automatically warns a user if the material usage goes 20% above or below normal usage. This allows a packaging line manager to easily track and monitor hot melt adhesive consumption. Current material usage is displayed on the screen of the InvisiPac user display, which can be reset at the beginning of each shift. The line manager can therefore keep an eye on the average amount of hot melt consumption per shift. If a sudden change in adhesive consumption is indicated, he knows there may be a problem and can immediately take action to remedy the situation.
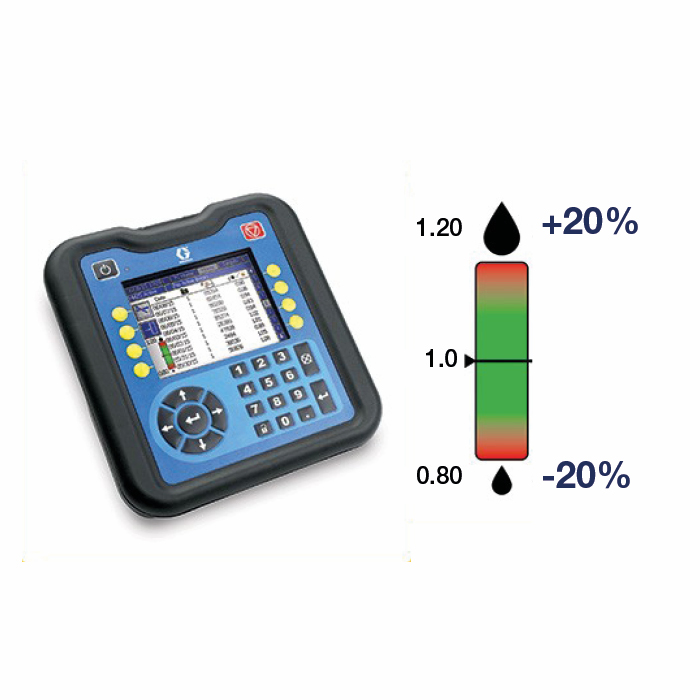
Analyse adhesive consumption and increase your packaging efficiency
But don’t think for a moment that the line manager has to be glued to the display. The system allows him to download and save files to a flash drive for a historical look at adhesive consumption. Data can then be analysed and graphed to get a visual indication of material consumption over time. No matter how he uses Graco’s Adhesive Tracking Technology – which is built into InvisiPac as standard – it’s extremely beneficial because it highlights anomalies in adhesive consumption.
For example, if adhesive usage is going down, it may indicate that someone turned the air pressure down on the machine, which might result in boxes being insufficiently sealed. If adhesive suddenly increases, it could mean an operator saw a box open and decided to turn up the air pressure. This may seem to be the logical action to take, but it may not be the right one as other variables on a packaging line might be involved.
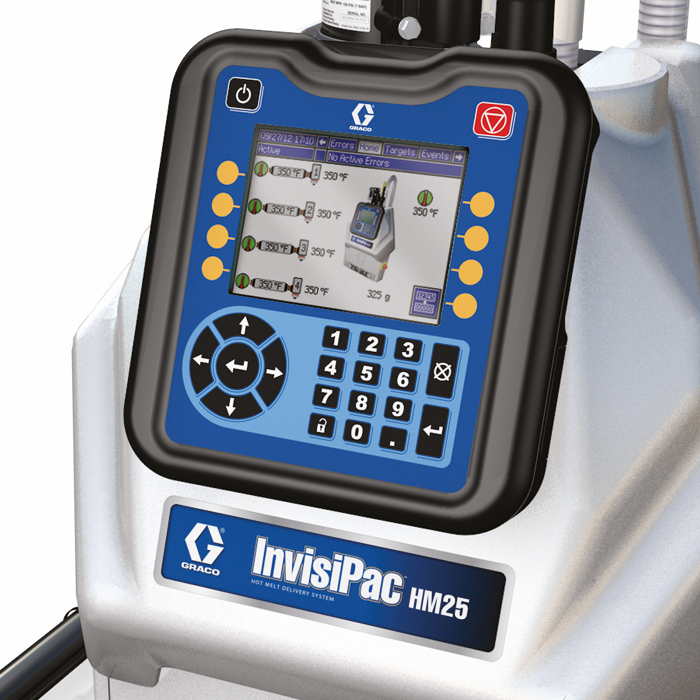
“We’re wasting HOW MUCH adhesive?”
If you don’t know how much you are using, you don’t know how much you are wasting. This certainly applies to hot melt adhesive. If you want to use less adhesive, you work out how many grams of adhesive you are currently using to seal each carton on your packaging line. On the other hand, you might be wondering about the quantitative benefits of Graco’s Adhesive Tracking Technology. After all, saving milligrams of adhesive per carton isn’t really a significant saving. Or is it?
A real case example: £30k (€34K) material cost savings per year
You would be surprised. One company put the technology into place and realized they were consuming 70% more adhesive than necessary, which was equivalent to around £30k (€34K)
worth of adhesive per line per year. This figure is certainly something to bear in mind the next time you look at your packaging line.
Contact Graco’s hot melt experts in the form below for further information on Graco’s Adhesive Tracking Technology or the InvisiPac hot melt system.
Related Articles
Why InvisiPac is the reliable option for your packaging line?
An InvisiPac tank-free hot melt glue system with melt-on-demand process avoids charring and nozzle blocking.
Choosing a hot melt nozzle
The choice of hot melt nozzle impacts the performance of your end-of-line packaging operations.
Monitoring hot melt adhesive dispense
Track adhesive usage and improve efficiencies with remote monitoring of your hot melt adhesive application.