Open loop vs. closed loop communication
On industrial finishing lines, technology can range from manual knobs on a closed loop controller to an open loop controller with touchscreen displays. What works best and when? Find out.
When you walk into different finishing lines, controls on equipment can range from manual knobs to touchscreen displays that automatically regulate process controls.
Differences in technology can seem overwhelming, but in reality, they all fall into a basic framework: Closed or open loop communication
Closed loop vs. open loop communication
Some systems with manual air regulators run on open loop communication. This means that there is no feedback, or continuous control.
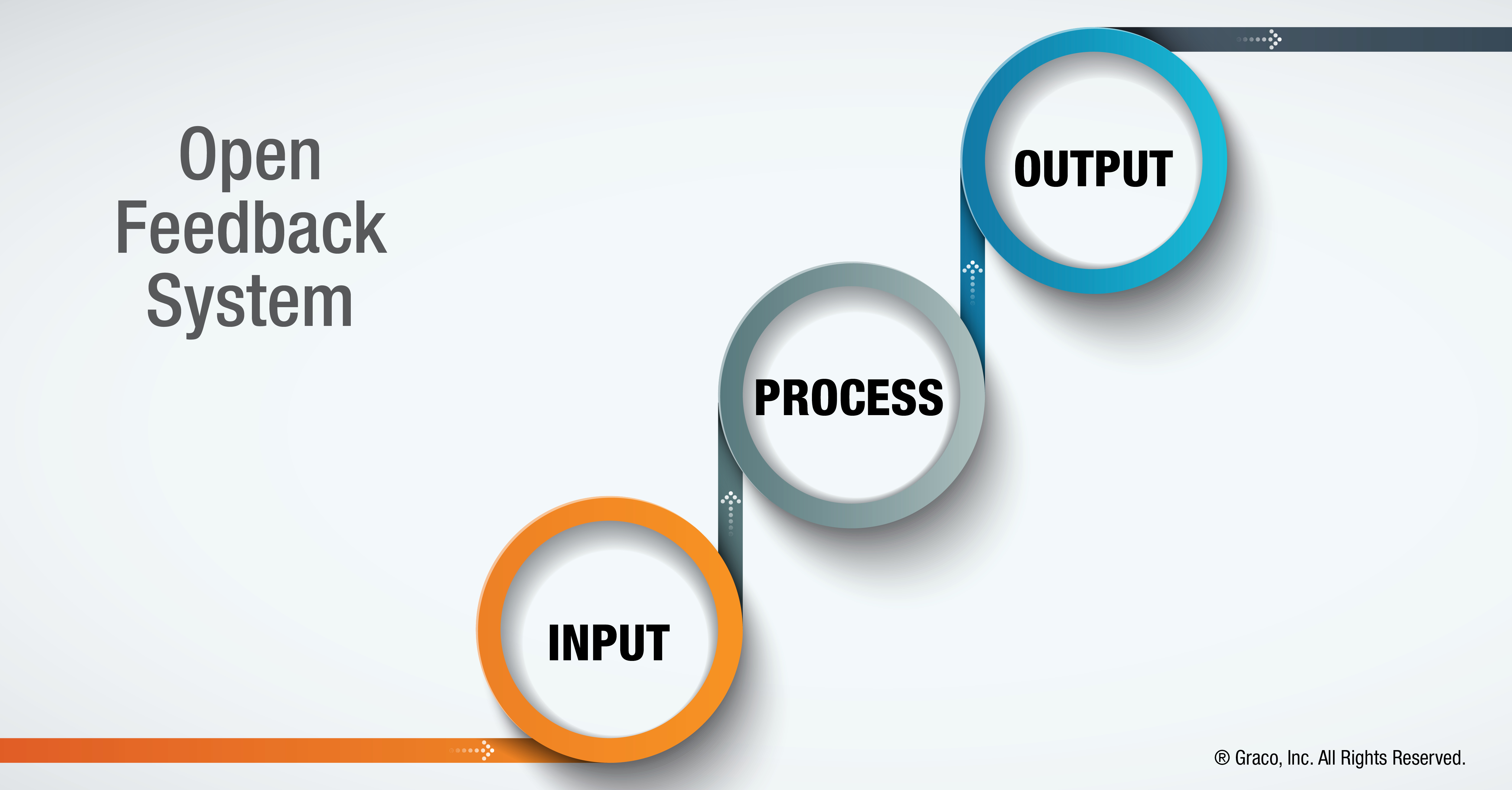
Newer systems have closed loop control. A feedback signal is sent back to the controller to maintain a desired result. The advantage of this is that the system is now self-regulating.
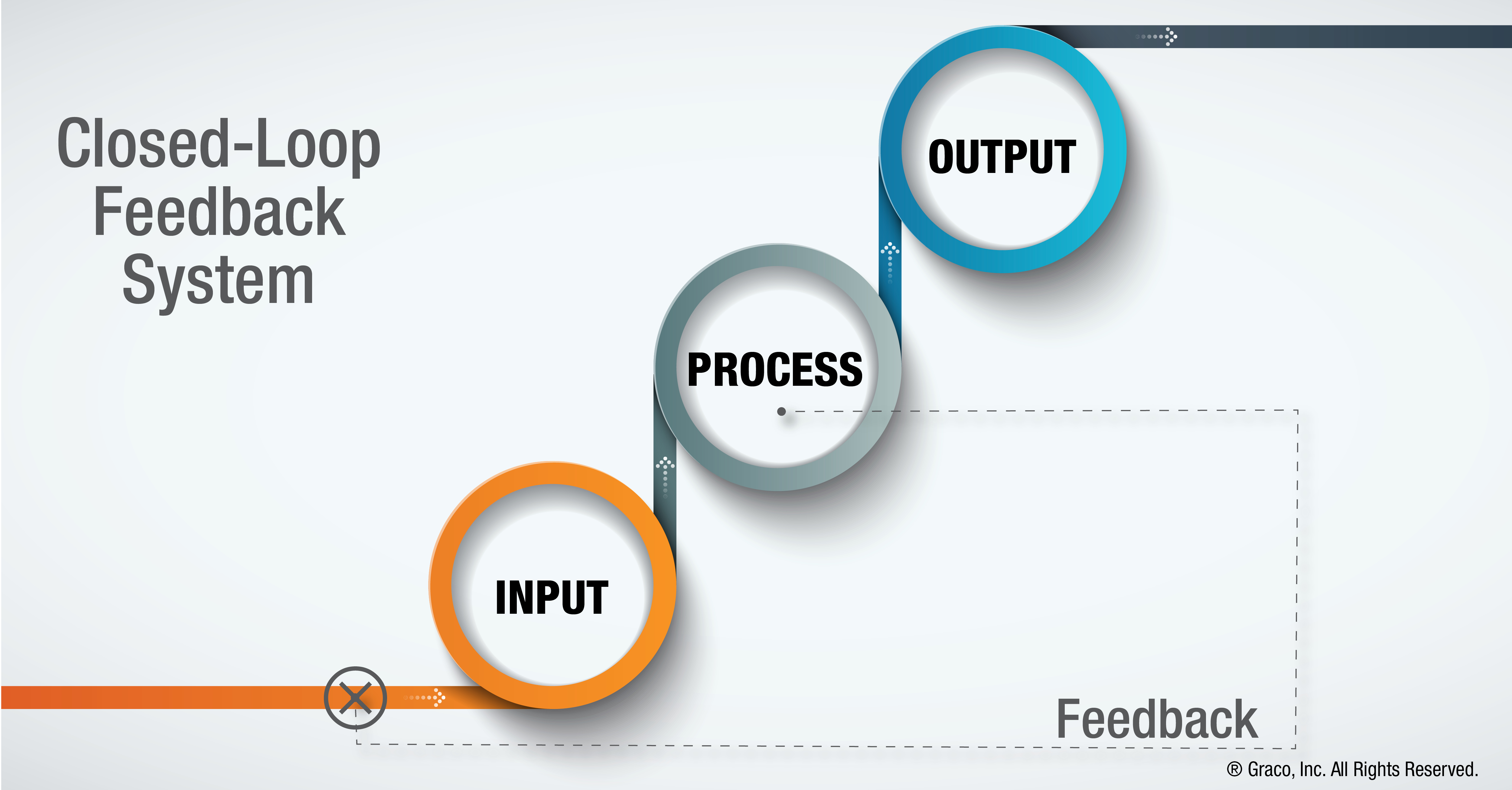
For example, you want to spin a rotary bell atomiser at 50,000 rpm.
- In an open loop communication system, you would adjust the air regulator knob and watch the speed, periodically checking to see if the system was maintaining the rpm.
- In a closed loop communication system, you can set your speed at precisely 50,000 rpm. The system will automatically regulate its turbine air pressure to maintain that speed within a certain margin for error.
With closed loop communication, we can also collect data on system parameters throughout production. This can be very useful in continuous improvement and quality assurance initiatives.
What process control works best and when?
When to use an open loop controller
In some cases, self-regulated equipment is overkill for a manufacturing process. Open loop communication can be more beneficial in these types of production environments.
- When low cost is the highest priority
- Output is not affected by external variables and rarely changes
- No quantitative measurement is possible
- Process disturbance is extremely rare
Example of an open loop system
A truck manufacturer applied a two component material for reducing rust on chassis. To mix this material, they decided to use a Graco ProMix 2KS plural component system with open loop communication.
Keeping costs low was a high priority, while changes in finish quality throughout the day was not as important. In this case, open loop communication was just fine for this manufacturer’s needs.
When to use a closed loop controller
Closed loop communication provides a lot of benefits for manufacturers looking to improve process control. If any of the following are important in your paint line, closed loop controls could provide untapped improvements.
- When there is something to measure (speed, flow control, pressure, temperature, etc.)
- Process has a degree of predictability - a known or approximate response to an input or control
- Output can vary from a desired outcome and is not a “set and forget” process
- Quality is specific and valuable to your process
- Real time data analysis and repeatability is important
- Consistency of products across shifts, days and weeks
Closed loop system example
A high volume commercial vehicle manufacturer needed to maintain a consistent mil thickness. Variations in viscosity and air pressure throughout the day made consistent finish impossible without constant oversight.
Graco’s ProControl 1KE Plus provided closed loop flow control and gun atomising pressure control for their one component materials. This allowed the ability to maintain ideal flow and pressure rates without manual oversight. It also led to less rejected parts, less employee downtime, and a material use reduction of 40 percent.
Added benefits of closed loop communication
With closed loop communication, you can preset system parameters and track data throughout production.
- Setting parameters ahead of time makes transitions smoother and consistency of quality higher.
- Being able to track data throughout production can be very useful in continuous improvement and quality assurance initiatives.