Plural-component sprayers deliver high-flow capabilities
High-flow technology
Plural-component sprayers have proven highly effective in pumping, mixing and atomising a wide variety of protective coatings. The ability to mix components within the spraying system, rather than manually mixing components before adding the mixture to the system, has improved quality and reduced labour costs for contractors in numerous industries.
Even more benefits can now be achieved by adding high-flow capabilities to plural-component sprayers. The Graco XP50s-hf and XP70s-hf series of sprayers use the powerful XL10000 air motor, high-powered heaters and heated tanks, enabling contractors to complete jobs even faster and with less wear and tear on equipment.
Labour savings
The original plural-component XP50 and XP70 sprayers, introduced between 2010 and 2012, are designed to handle high-viscosity coatings with an up to 100 percent solids content. For large, high-demand projects requiring large spray tips or multiple guns, the new skid-based XP50s-hf and XP70s-hf enable the same multiple-component spraying, along with high-flow capacities.
Heating and mixing
Two heated tanks help pre-condition the components, maintaining an optimum temperature and viscosity for more efficient application. In addition, higher wattage heaters (5,400 W) provide for faster heat-up times. A lower pressure drop in the system allows the coatings to be sprayed at lower pressures than ever before.
Instead of spending time mixing components and dealing with short pot-life materials, workers can focus on applying the coatings and let the sprayer handle the mixing on an ongoing basis.
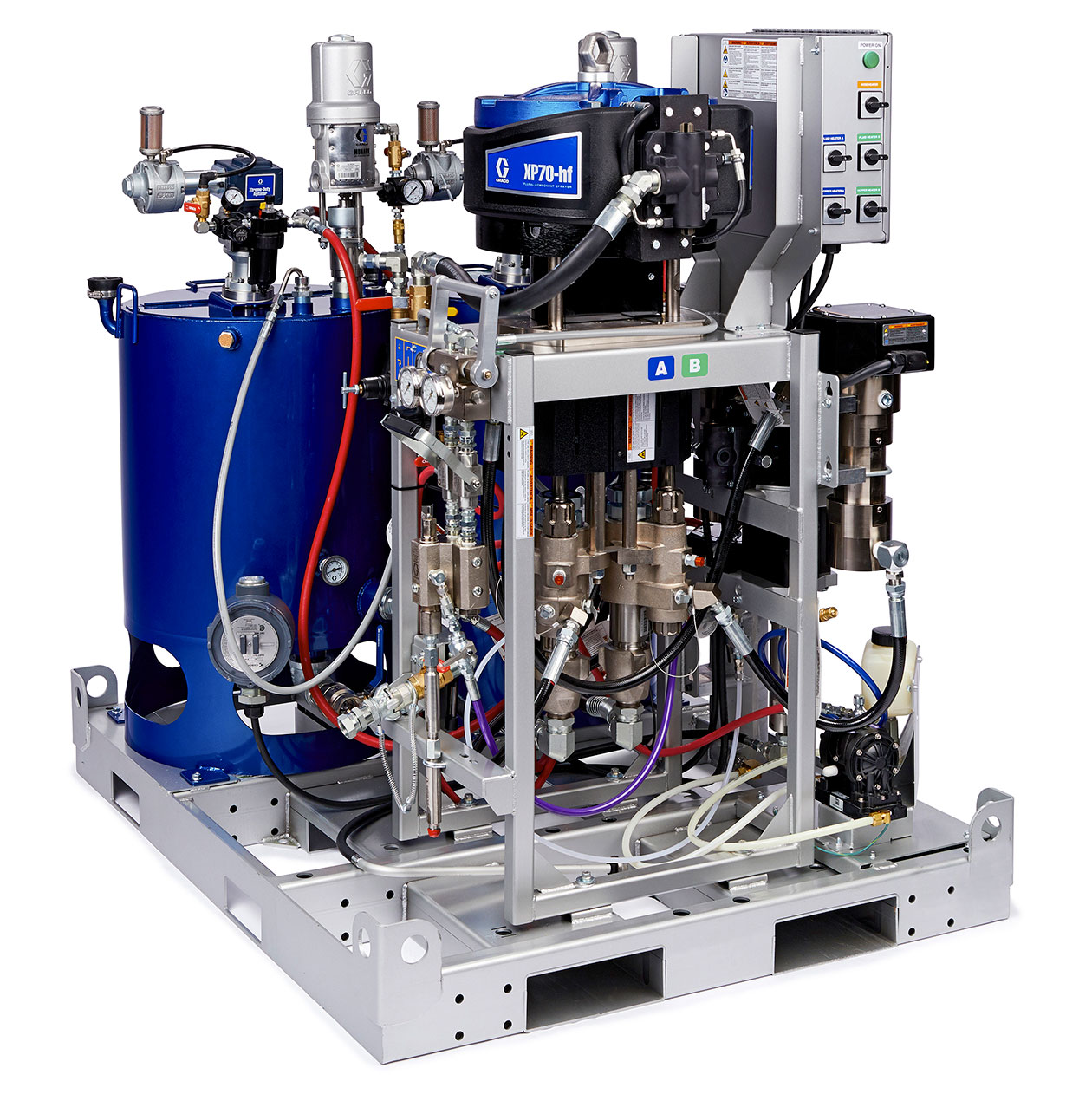
The addition of the XL10000 motor and related engineering upgrades provide for a higher flow capacity and the ability to spray with multiple guns or larger tip sizes. The XP50s-hf can provide a pressure of up to 5,000 psi and deliver 4 gallons per minute, while the XP70s-hf can provide a pressure of up to 7,250 psi and deliver 3 gallons per minute. In short, more work can be completed faster, with higher flow rates and multiple workers.
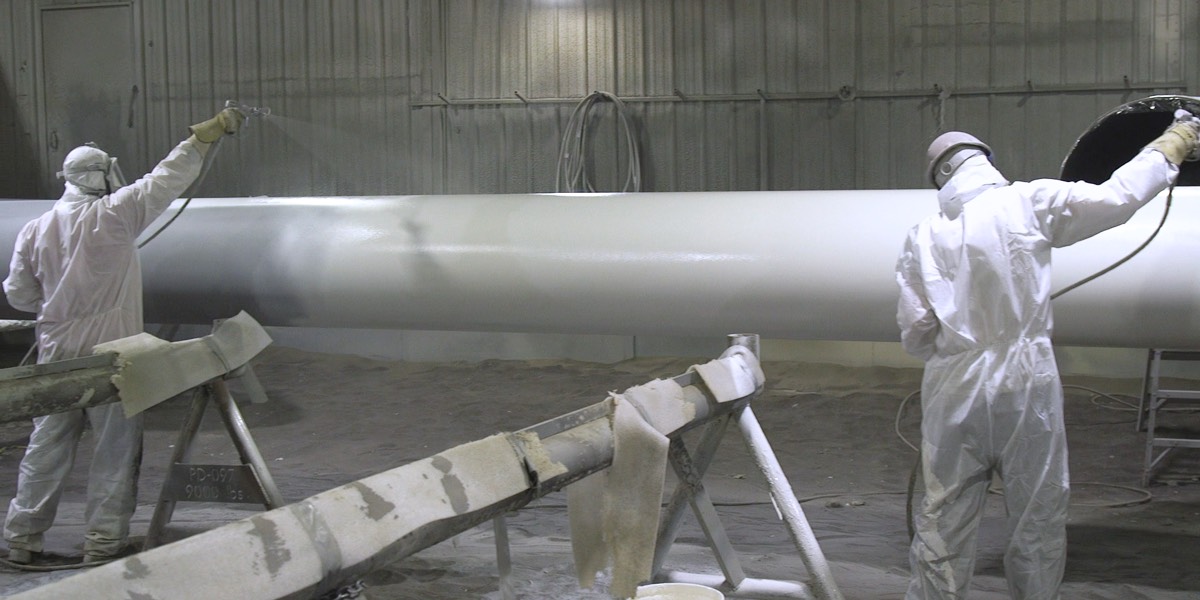
The XPs-hf sprayers enable multiple guns to be operated from the same system.
Reduced maintenance costs
The XPs-hf sprayers can also reduce maintenance costs. Instead of running mixed A and B material that is curing through a single-leg pump design, the A and B materials are handled separately in the system, which increases the life of the pump and reduces the cost of packings, pumps rods, pump cylinders, and parts. Because the material is not chemically reacting in the pumps, wear and tear is reduced and pump life is extended. All parts are stocked and supplied from the Unites States, so if a replacement part is needed, downtime can be minimised for most end users.
Quality benefits
On-demand mixing of components also provides for a more consistent material quality. Instead of relying on manual mixing, which can be prone to mismeasurements and guesswork, mixtures are precisely controlled. The warmed components can be mixed and applied consistently because the material is always fresh as it is sprayed, unlike a mixed batch of material that is reacting and approaching its pot life in a pre-mixed container.
With its higher pressure ratings and the ability to move the mixing point to a remote manifold, the system can handle highly viscous materials through long hose lengths, enabling workers to access hard-to-reach areas while still maintaining consistent flows and pressures. Large projects such as petroleum tanks, piping, and rail cars can be coated swiftly and with a consistent quality, with multiple workers applying precisely controlled mixtures.
Hoppers can contain up to 25 gallons of coating components, reducing the number of times workers have to stop and add components. Mix ratios can be adjusted by swapping out one or two pump lowers to achieve standard ratios ranging from 1:1 to 4:1.
Environmental factors
The XPs-hf systems also offer several environmental benefits. A solvent pump plumbed into the system aids in cleaning up operations at the end of the day and minimises waste. This pump allows the mixed material to be flushed out of the hose at the mix point, downstream of the machine, and the hoppers do not need to be flushed out if the system will be used again the following day or after a break. With manually mixed systems, significant material waste can occur when mixed material is discarded at the end of the day.
Along with the reduced volume of flushed mixture, less clean up solvent is required, reducing the amount of volatile organic compounds (VOCs) introduced into the atmosphere. Reduced solvent requirements also reduce costs for contractors.
Factoring in all the benefits – labour savings, maintenance reduction, quality improvement and environmental factors – the XPs-hf sprayers raise the bar in applying high-quality protective coatings.
About the author
Contact an expert
Related articles
How to Spray Inorganic Zinc Primers
To properly spray inorganic zinc primers, it is as much about how you handle the material as it is about the pump. Here's why.
A closer look at Graco’s XP Plural-Component Sprayers
What’s the difference between the standard airless and the high-flow (hf) airless versions?
The benefits of data collection when spraying fireproofing
The combination of smart electronics and high-performance components results in the high-quality application of high-performance fireproofing products.