Reducing environmental concerns with vapour blasting equipment
Lloyds Engineering of Sharjah, Dubai designs and fabricates steel structures, tanks, pipe spools, pressure vessels and process skids for both onshore and offshore facilities.
When blasting was required, outside contractors were used, but neither Lloyds Engineering nor their customers were satisfied at the quality levels obtained. The company, therefore, decided to construct their own blasting room and started looking for a supplier of a more efficient, dust-free blasting solution that could give them higher quality blasting.
Demo and training program with successful results
Graco distributor BITEC was contacted, and BITEC Branch Manager Mohammed Nayaz organized a demonstration at Lloyds Engineering of vapour blasting using EcoQuip EQ 600S. It made a big impression, with its clear benefit of a reduction of environmental concerns through not using sand or water.
BITEC followed up the demo with a training program for all the 125 technical staff at the Sharjah site. EcoQuip EQ 600S is now being used as the standard high-quality vapour blasting equipment by Lloyds Engineering, to the satisfaction of their customers.
Why Vapour Abrasive Blasting?
To prepare a surface for effective corrosion protection, sandblasting is a commonly used technique. However, the major disadvantage of sandblasting is the vast quantity of dust produced. Apart from the health and safety issues of clouds of dust – not only for the operators but people in the immediate vicinity – dust disposal is costly. The cost and disposal of the abrasive also has to be taken into account. Graco has been concerned with these issues for a number of years and has developed a revolutionary alternative to sandblasting: vapour abrasive blasting with EcoQuip™.
EcoQuip provides a performance equivalent to sandblasting but with 92% less dust, thus minimising the need for PPE, tenting and containment, and decreasing environmental impact. In addition, it uses up to 75% less blast media and far less water than wet blasting, and creates little run-off. This means there is no large slurry mess to clean-up and dispose. It’s effective in rain and high humidity, and efficiently removes coatings without damaging the sub-surface. The bottom line is that EcoQuip reduces project costs while increasing the speed, efficiency and productivity of blasting.
More information
For more information about Graco's abrasive blasting solutions, fill out the form below.
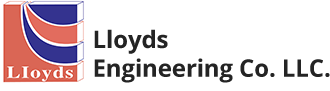