QUANTM High Sanitation
QUANTM high sanitation double diaphragm pumps
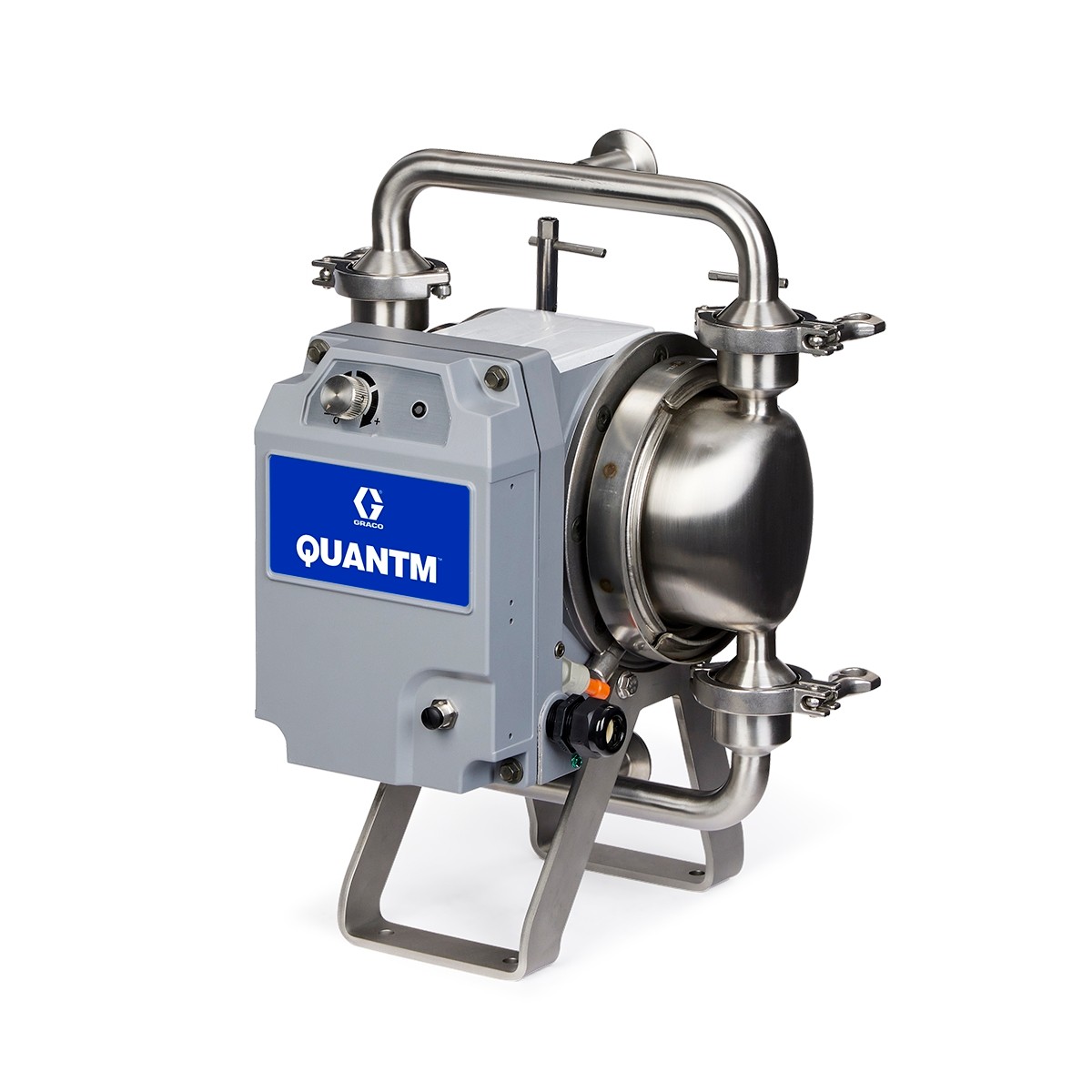
QUANTM High Sanitation
QUANTM high sanitation double diaphragm pumps
Graco’s QUANTM high-sanitation electric operated double diaphragm (EODD) pumps are the ideal solution for high-sanitation, helping facilities cut energy costs, meet sustainability goals, and ensure regulatory compliance. With a return on investment in under a year, QUANTM delivers both cost savings ...
More Info
Features
Product Brochure
Graco’s QUANTM high-sanitation electric operated double diaphragm (EODD) pumps are the ideal solution for high-sanitation, helping facilities cut energy costs, meet sustainability goals, and ensure regulatory compliance. With a return on investment in under a year, QUANTM delivers both cost savings and rebate opportunities.
With flow rates up to 454 lpm (120 gpm) and 7 bar (100 psi), these pumps meet the toughest food, beverage, personal care and pharmaceutical demands. Ideal for upgrading air-operated pumps, they offer self-priming, seal-less design, and smooth flow. The powerful XT motor and drive delivers 8x more torque at low speeds, while the plug-and-play 240V and 380V/480V installation fits AODD footprints – no extra investment is needed.
- Efficiency
- Up to 80% more efficient than AODD, 50% more efficient compared to competitive electric technologies—displacing fossil fuel, hydraulics and air power
- Quick knockdown pumps
- Designed with DIN or Tri-clamp fluid connections, designed for CIP-applications
- Versatility
- A wide operating range and materials compatibility — it handles abrasive substances, solids, and shear-sensitive materials
- Automation
- I/O port for integration with plant PLC enabling remote and hands-free management
- Overmoulded diaphragm plates
- Designed with PTFE on the fluid side and EPDM on the air side
- Does not contain crevices that can harbour bacteria
- Unique stall feature
- The only electric diaphragm pump on the market that stalls under pressure, eliminating the need for pressure sensors and additional controllers and reducing downtime by preventing pump failures caused by clogged lines or closed valves
- Overmoulded diaphragm plates
- Designed with PTFE on the fluid side and EPDM on the air side
- Does not contain crevices that can harbour bacteria
- Bolt-through diaphragm options are also available
- The only electric diaphragm pump on the market that stalls under pressure, eliminating the need for pressure sensors and additional controllers and reducing downtime by preventing pump failures caused by clogged lines or closed valves