Kawasaki Updates their Finishing Line with ProMix Proportioners
Kawasaki wants the world to know that if you're riding one of its motorcycles, ATVs, personal watercrafts or utility vehicles you're riding "The Leading Edge of Power/Performance/Exhilaration."
While accurately describing its consumer recreational products, the phrase could just as easily describe Kawasaki Motors Manufacturing Corp., U.S.A's "Leading Edge" manufacturing facility in Lincoln, Nebraska, where these products are built. The facility features the best of Japanese and American manufacturing techniques; as well as state-of-the-art production equipment that is chosen for its ability to optimise productivity, maintain quality and reduce waste.
Upgrading equipment after 17 years of service
Recently, faced with the high cost of rebuilding a mechanical paint proportioner on a paint line in the Lincoln facility, Kawasaki decided instead to replace the old piece of equipment with a high-tech electronic proportioning system. "For over 17 years we've been using Graco Variable Ratio Hydra-Cats on our paint lines," said Matt Thomas, Senior Engineer. "They've served us well but after years of continual use, they're wearing out. Replacing major components is expensive so when we compared the cost of repairing the old mechanical proportioner to purchasing a new proportioner, we discovered the difference was insignificant. It was an easy decision."
Because the old Graco proportioners held up so well for such a long time, Kawasaki chose to replace the old workhorse with one of Graco's new generation of proportioners — the ProMix. ProMix is an affordable, easy-to-use electronic proportioner designed for single colour, two-component spray finishing applications. The air-operated proportioner is capable of handling most coatings, as well as a wide range of ratios with flow rates as low as 20 cc/min.
Installation
The ProMix was installed on the finishing line where painters spray the fibreglass decks of the Company's Jet Ski® personal watercraft. After being loaded onto an overhead conveyor, the decks receive a prime coat, topcoat and clear coat. All three coatings are two-component coatings that require metering and mixing.
The ProMix is used to proportion the topcoat, a 40% solids red urethane. At this time, the old mechanical proportioners are still used to meter and mix the primer and clear coat. In addition to the three coatings, the decks are puttied, sanded, buffed, polished and inspected numerous times as they progress along the line.
The ProMix was installed right in the spray booth because it features intrinsically safe controls, allowing easy integration into hazardous environments. "The system is just steps away from the painter," says Thomas, "providing him with easy access to the system's controls." In addition to easy access to the controls, the short distance the mixed material travels from the ProMix to the spray gun has reduced the amount of mixed material Kawasaki wastes during flushing, as well as the amount of solvent required to purge the fast curing paint from the fluid hose. The proportioner also features a new fluid manifold that further reduces the amount of solvent required to flush the system by an additional 20%.
"There isn't much the painter has to worry about," says Thomas. "All he has to do to start up the system is simply turn a dial, push a button and he's ready to spray. When he triggers the gun he knows he's getting the mix ratio we programmed into the unit."
Ratio accuracy assured
The ProMix automatically maintains its mix ratio within 1%. If an off-ratio occurs the system will stop production and sound an alarm, preventing any off-ratio material from being sprayed on the part. Codes on the controller will direct the operator to the cause of the problem. The controller monitors pump and motor operation, as well as metering accuracy. "Once we enter the specified ratio into the ProMix, we don't have to worry about the quality of material we're spraying — it's the same every time," he says.
This wasn't the case with the old mechanical proportioners. "Ratio accuracy was a problem we always worried about," says Paint Line Supervisor Randy Tamerius. "They were so worn they would begin to creep off-ratio. It could result in a finish that was tacky and took longer to cure. We had to constantly check the ratios." Changing or adjusting the ratio on the old proportioner was another chore. It could take up to an hour. On the other hand, changing the ratios on the new ProMix system is easy. It simply requires the operator to enter the new recipe into the controller. When the correct ratio is displayed on the controller screen, the system is reprogrammed.
"It's simple," says Thomas. According to Thomas, they discovered just how easy it was to reprogram the system when the ProMix was moved from the Jet Ski finishing line to a line where ATV parts are painted. "We were going to have to replace the mechanical proportioner that was metering and mixing a clear coat on that line. We wanted to put the ProMix in there to see if it could handle the material as easily as it did the topcoat on the Jet Ski line."
They installed the ProMix and reprogrammed it without suspending production. "We did it ourselves without any difficulty," says Thomas. In fact, the team on the ATV line liked the ProMix so much that they didn't want to return it to the Jet Ski line. Kawasaki ended up purchasing a second unit to permanently install on the Jet Ski line. In addition to proportioning the plural-component material and alerting the crew to off-ratio occurrence, the ProMix also measures and records the total amount of the mixed material used, as well as the usage of each separate component. It also monitors pot life and sounds an alarm if the mixed material in the line is close to curing.
"This system is just so much easier to use," says Thomas. "It's easy to set up, easy to operate, and the display is easy to understand. We recently purchased a third ProMix and expect to replace the remaining mechanical proportioners with ProMix units as the old proportioners become too costly to repair. Since we put the first ProMix in, we haven't had a single problem," he adds.
More information
For more information about Graco ProMix proportioners, fill in the form below.
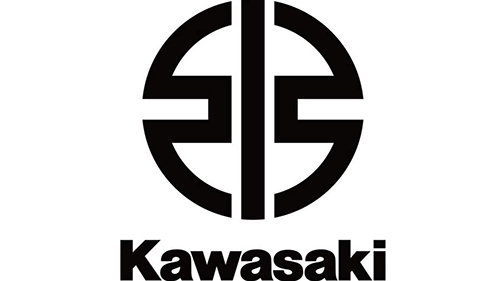
Related Articles
The smart way to mix paint
Graco ProMix PD2K paint mixing machines play a key role in the digitalization of painting lines at Pieffeci Turin
John Deere factory in Mannheim installs Graco 2KS paint supply system
To meet stringent quality standards and increase process reliability, the John Deere factory in Mannheim has invested in a new Graco paint supply system.
5 significant advantages of robot painting
The advantages of automated painting: reduce costs and waste and improve flexibility and quality.