Sealing a swimming pool
A Graco proportioner and Fusion PC spray guns were essential tools to seal a leaking swimming pool in the Polish town of Wisła
The owner of the Start Sports Center on Olimpijska 1 in Wisła, Poland was facing a number of challenges with its swimming pool that needed to be urgently addressed.
The 49 x 13 meter swimming pool is located on the old riverbed of the Vistula. Over the years, rainwater and groundwater have had a negative impact on the reinforced concrete basin of the pool, leading to numerous cracks in its base and sides, which started leaking.
The solution wasn’t as straightforward as simply draining the pool and relining it. The geometry of the pool is complicated. From the shallow end, the pool’s depth gradually increases from 1.2 meters to 1.8 meters, before plunging into a deep 4-meter section with steeply sloping walls. It is this deep part of the swimming pool where most of the cracks were occurring.
Calling in expert help
Local contractor Stanepoxyd visited the site. Stanepoxyd specializes in waterproofing buildings such as wastewater treatment plants, power plants, tanks and bridges. This refers to both keeping water out, as well as keeping it in! More relevant, over the years the company has built up considerable experience in repairing leaking swimming pools of all sizes, from small private pools to large municipal pools.
After carefully examining the pool and the cracks, they proposed to repair the concrete structure and spray a polyurea membrane over the whole of the pool, followed by a polyaspartic top coat. A polyaspartic coating offers specific advantages over epoxy and polyurethane coatings. It is highly flexible, as opposed to epoxies which are stiff and prone to scratches and abrasions during intense use. It also exhibits good UV resistance. Moreover, a single coat of polyaspartic paint accomplishes what traditional epoxy and urethane systems need two coats to do.
The owners were satisfied with Stanepoxyd’s proposal and gave the green light in November 2020. The job had to be completed by April 2021 in time for the new season. Stanepoxyd chose to work with Graco equipment: the Graco Reactor 2 E-XP2 proportioner and the Graco Fusion PC gun.
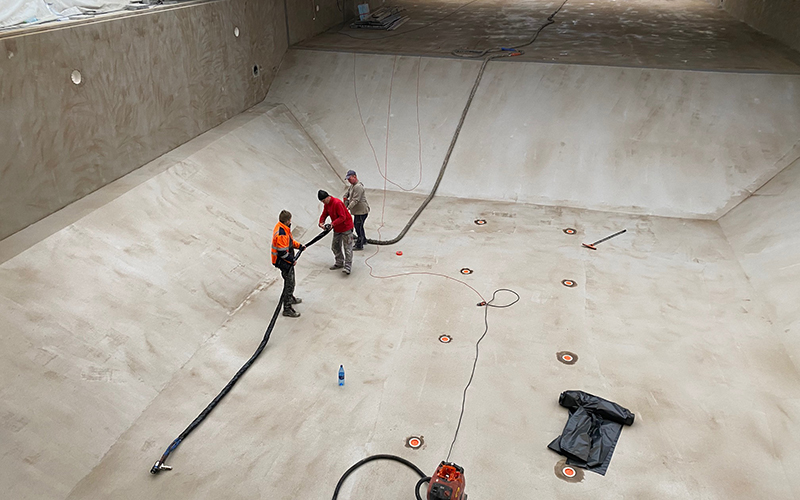
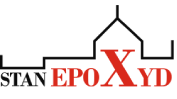
THOROUGH PREPARATION IS VITAL
As with any coating job, success depends on excellent surface preparation. Of the 16 weeks allotted to the project, 13 were taken up with preparing the surface. A team of eight was involved on the job.
The complex geometry of the pool meant that it was a challenging job to recoat. A number of reprofiling treatments were needed, using specialized Polymer Cement Concrete (PCC) mortars. A second subcontractor was called in to perform injection sealing of the structural cracks.
After this procedure was completed, a three-component mortar was prepared. It was designed to protect the polyurea coating against numerous osmotic bubbles caused by negative moisture pressure from the outside. Priming was then performed with a two-component epoxy resin with a sprinkling of quartz sand with a fraction of 0.4-0.8 mm. This was followed by spraying a 2 mm polyurea layer. Finally, the top coat of polyaspartic resin RAL 5012 was applied manually using the traditional method with a roller. Horizontal black markings in accordance with FINA regulations were added as the finishing touch.
REACTOR 2 E-XP2 PROPORTIONER
Stanepoxyd has been using the Graco Reactor 2 E-XP2 for nine years and has always been impressed by its high performance. For this project, it was set up with a 1.7 m3 screw compressor, a 50 kW generator, recirculation and T1 pumps, and a 78-meter length of hose. The machine worked flawlessly to mix and spray the polyurea coating. The unit sprayed without pulsation, resulting in an even distribution of material on the substrate.
The operators were impressed with the machine’s Advanced Display Module (ADM). This interface allows operators to easily track and monitor spray performance and ratio, and enable alarms. It also has the ability to save project information and download data onto a USB drive for further analysis. Having an interface and a reporting tool was found to be invaluable for quality control purposes.
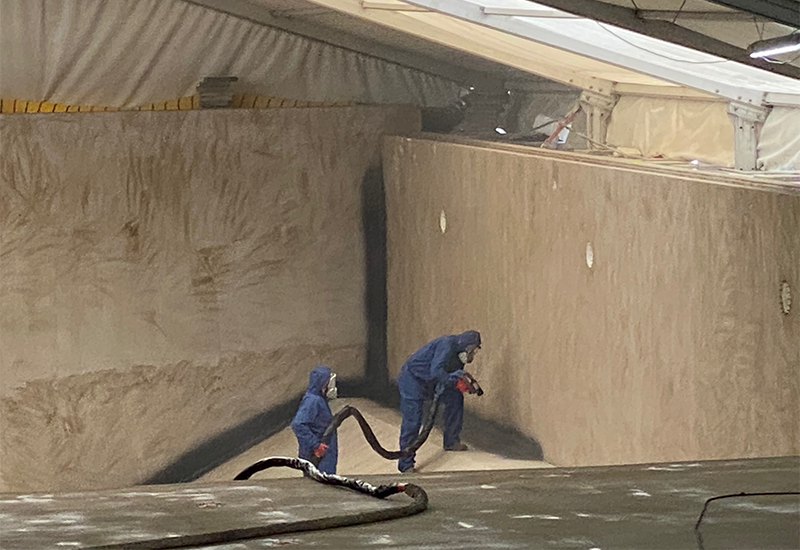
FUSION PC GUN
The main reason for choosing the Graco Fusion PC gun to spray the polyurea coating is its innovative design. The Fusion PC gun features a replacement cartridge head that replaces multiple individual parts with a single component. Simply replacing a cartridge allows for a much faster rebuild, which increases spraying time and minimizes costly downtime. This is a crucial factor when spraying a large area like a swimming pool.
The Stanepoxyd operators who used the gun for two days on this project considered the Fusion PC easy to work with for long periods. It gave a very smooth, uniform application of coating. They were most impressed by the short disassembly and assembly time of the gun, which reduced cleaning and maintenance time to an absolute minimum. This enabled them to complete the project within the specified timeframe.
REDUCED MATERIAL CONSUMPTION
Nearly 2000 kg of polyurea was used, along with 650 kg of polyaspartic material. The polyurea set in seconds, while the polyaspartic material was allowed to set for four hours before the next layer was applied. Spraying the polyurea was conducted with nozzle 2929 for 4.5 sets each of 425 kg. It took just two full days – working from morning until after midnight – to spray the total surface area of approximately 1000 square meters.
SATISFIED OWNER
Thanks to thorough surface preparation and the right selection of materials and equipment, the swimming pool at the Start Sports Center in Wisła was successfully recoated with a polyurea layer and finished off with a layer of light blue aspartic paint. The owner was delighted and was able to re-open the swimming pool in time for the new season.
FURTHER EXPERIENCE WITH FUSION PC
Over the past six months, Stanepoxyd has used the Fusion PC gun on other projects, with total satisfaction as to its performance. To date, they have found that a single cartridge is capable of spraying as many as 23 sets of material. They particularly appreciate the quick-change cartridge. In case of failure, it can be swapped in just five minutes. This saves a considerable amount of time compared to the Graco Fusion AP gun, which takes around an hour to clean, should it fail. A further advantage is that when working with Fusion PC in the field, Stanepoxyd don’t need to take a back-up gun in case of failure; they simply take an extra cartridge.
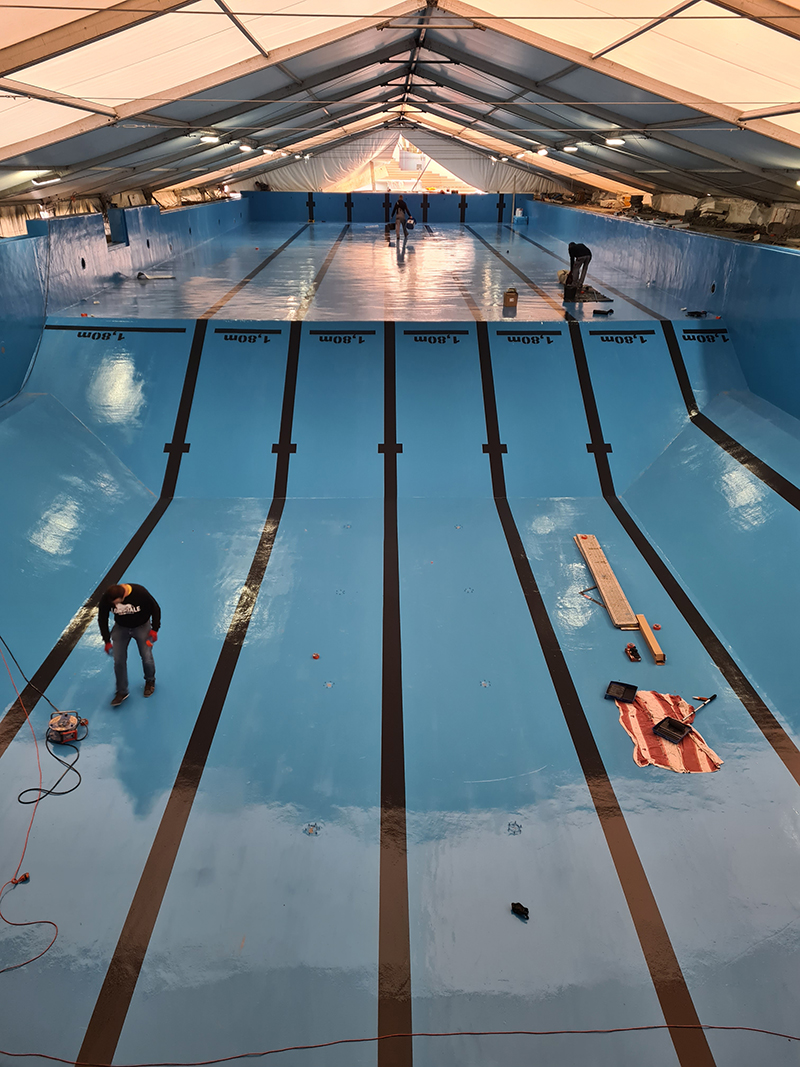
MORE INFORMATION
If you are interested in learning more about the Graco Reactor 2 E-XP2 proportioner or the Graco Fusion PC gun, fill in the contact form below.
Related Articles
How to recoat a swimming pool with Polyurea
Saudi Jomana and AEMCO recently joined forces to recoat a leaking swimming pool, using polyurea and Graco’s Reactor 2 E-XP2.
Spraying swimming pools with gel coat systems
Learn how Franmer worked with Graco on spraying swimming pools with gel coat systems.
Swimming pools in Antalya lined with Graco’s Reactor H-XP2
Find out how swimming pools in Antalya were lined with Graco’s Reactor H-XP2.