Tips for Improving Transfer Efficiency
Selecting the most efficient spray gun for the intended application is important in optimizing the efficiency of your spray operation.
What’s transfer efficiency? Why are paint spray guns so important?
Transfer efficiency is critical to the spray finishing industry from both a cost and a regulatory standpoint. With high transfer efficiency, manufacturers can save money and reduce VOC (Volatile Organic Compound) emissions.
Although transfer efficiency is a relatively simple concept, TE ratings can lead to considerable confusion (or even deception) if not clearly understood.
The term “transfer efficiency” or “TE” refers to how much paint spray covers a part, compared to how much material sprays past the part and is wasted. This makes choosing the right paint spray gun for the intended application the biggest factor in improving transfer efficiency.
Following these tips can help, too.
Know the Difference Between ASTM and EN Standards
Transfer efficiency (TE) is expressed as a percentage. For example, a 60 percent TE means that 60 percent of the material sprayed actually reached the part. The 40 percent balance was lost to the spray booth or other areas during the spray finishing process.
The two primary tests that measure transfer efficiency – ASTM and EN 13699-1 – come up with very different results. That’s why you need to know what standard applies to a TE percentage, especially when comparing the transfer efficiency of different applicators.
- The ASTM (American Society for Testing and Materials) test simulates a conveyor system. For conventional spraying, ASTM never has transfer efficiency greater than 50 percent.
- The European Standard EN 13699-1 test is performed by spraying a pattern in the middle of a large target. Because of how the test is done, the EN standard shows a higher transfer efficiency percentage for the same paint spray gun than the ASTM standard.
For example, an HVLP (High Volume Low Pressure) paint spray gun tested to the ASTM standard has 25 to 32 percent transfer efficiency. The same HVLP gun tested to the EN standard has 70 to 78 percent transfer efficiency.
Choose the Right Applicator for What You’re Spraying
Selecting the most efficient spray gun for the intended application is important to optimize your production line. Each spray technology – conventional air spray, compliant, HVLP, air assist, electrostatic and rotary atomizer – has its advantages and disadvantages. It all depends on the finishing results needed with the material being sprayed.
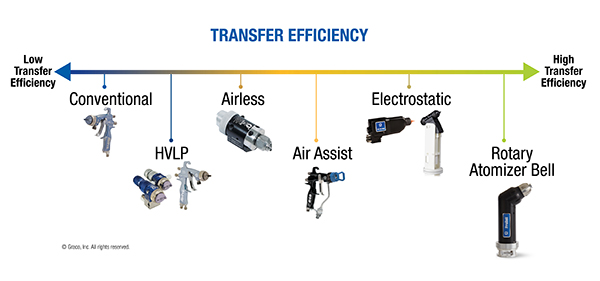
Ensure Proper Spray Gun Setup
To get the full benefit of your spray applicator, ensure you have proper setup.
Proper air pressure and fluid pressure is critical.
- Too much air pressure can cause excessive overspray and reduced transfer efficiency. The key is to use enough air pressure to get a high quality spray pattern, but low enough to optimize transfer efficiency.
- Fluid pressure should be minimized to reduce bounce back of material on the substrate.
Spray pattern height is also important.
- Your spray pattern height needs to match the part you are spraying. Material blow-by from too large of a spray pattern reduces transfer efficiency.
- The spray gun tip size should be sized to the largest spray pattern height for your parts, but not bigger.
You also should purchase a spray gun with a fan pattern adjustment knob. As part size varies, the operator can adjust the spray pattern height down to match the part size.
Train Operators to Use Proper Technique
Operator technique can affect transfer efficiency by 10 to 30 percent. Because of this, operators should be trained on proper spray techniques. Training should include:
- spraying the right distance from the part
- spraying perpendicular to the part
- triggering and de-triggering at the proper time
With a paint robot, the spray technique is consistent each time, and transfer efficiency is optimized.
Get Ready to Spray Less Paint
By increasing transfer efficiency we reduce the amount of paint sprayed. When more paint actually reaches a part, you need to spray out less to get the finish your customers need.
Spraying less paint leads to a reduction in released VOCs. It also lengthens the life of your booth filters.
Applicator ROI Calculator
How much could your paint line save with new spray gun technology? Calculate your return on investment.
Related Articles
Applicator Technology
When choosing the right liquid spray technology, it helps to understand the differences between air spray, air assist, electrostatic and rotary bell applicators.
Take the Paint Efficiency Audit
Take the paint efficiency audit and assess your current equipment and processes.
3 Steps to Reduce VOCs in Paint Lines
To minimize VOCs, manufacturing companies are looking for ways to reduce paint and solvent waste with more efficient equipment and automated processes.