Improve Hot Melt System Performance
Explore how to increase the working uptime of your packaging line by improving the efficiency of hot melt adhesive application.
The Drawbacks of Old Technologies
Many traditional and legacy hot melt technologies use a melting process that relies on tanks to heat the adhesive. This "crock pot" approach not only takes a lot of time to heat the material, it also generates adhesive char that plugs hot melt nozzles and causes equipment failure. Tanks truly are natural environment for char.
Also in many old hot melt systems, viscosity changes result in poor adhesive performance and inconsistent dispense.
- If too much glue is dispensed, material – and money -- are wasted.
- If too little is dispensed, pop-opens could lead to scrap or returned product.
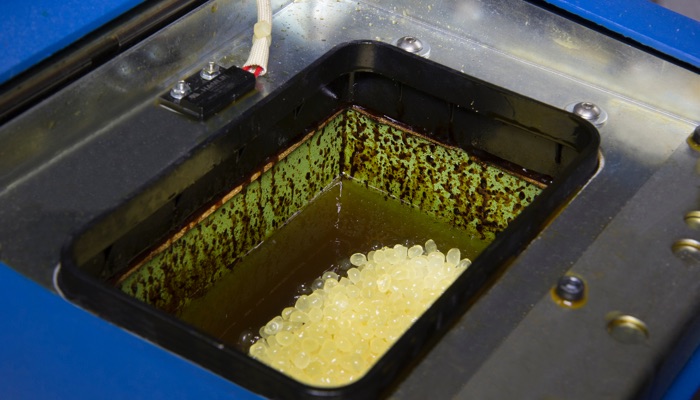
Adhesive char builds up on the sides of the reservoir in this tank-based hot melt system.
Adding new, un-melted pellets shocks the molten glue, changing its viscosity and causing pop-opens.
Tank-Free™ - not Tankless - Hot Melters
Instead of tanks, updated hot melt technologies use specially designed heating chambers. This tank-free approach significantly improves surface to adhesive ratio for fast, efficient melting.
It is not always clear if a hot melt system is truly tank-free, as some suppliers call their equipment "tankless."
- Tankless hot melt technology still has small tank or reservoir, where adhesive is heated to and kept at a certain temperature before it is dispensed. Since the adhesive remains in a tank until it’s needed, char easily forms.
- Tank-Free™ hot melt technology does not have a tank. Instead of keeping adhesive in a reservoir until it is needed, it melts and dispenses the adhesive on-demand. This first-in-first-out design leaves no chance for char to develop.
In this start-up time comparison, the melter on the left is Tank-Free; it has no reservoir. The tankless melter on the right has a small reservoir.
Integrated Vacuum Feeds Limit Viscosity Variations
To keep viscosity changes from causing poor adhesive performance and dispense, some newer hot melt technologies use an integrated vacuum system to feed adhesive to the melter.
- An ultrasonic sensor constantly monitors adhesive in the chamber.
- Adhesive is automatically added, as needed.
Depending on application demands, only about one-quarter cup of molten glue is added at a time. This gradual approach helps eliminate thermal shock and promotes consistent bead weights.
Integrated vacuum feed systems also save labor costs, as they don’t depend on anyone to keep an eye on adhesive. They automatically keep adhesive at optimum levels, while keeping in heat and keeping out dust and debris.
Surface Area to Adhesive Volume Ratio Reveals Performance
Surface area to adhesive volume ratio is important any hot melt technology. The higher this ratio is, the lower the likelihood of charring and the shorter the startup time will be.
By eliminating heated tanks and increasing the melting surface, Tank-Free hot melt technology dramatically improves end of line packaging performance. Adhesive pellets can be melted on demand and then dispensed quickly. This greatly reduces char and material degradation caused by prolonged exposure to heat.
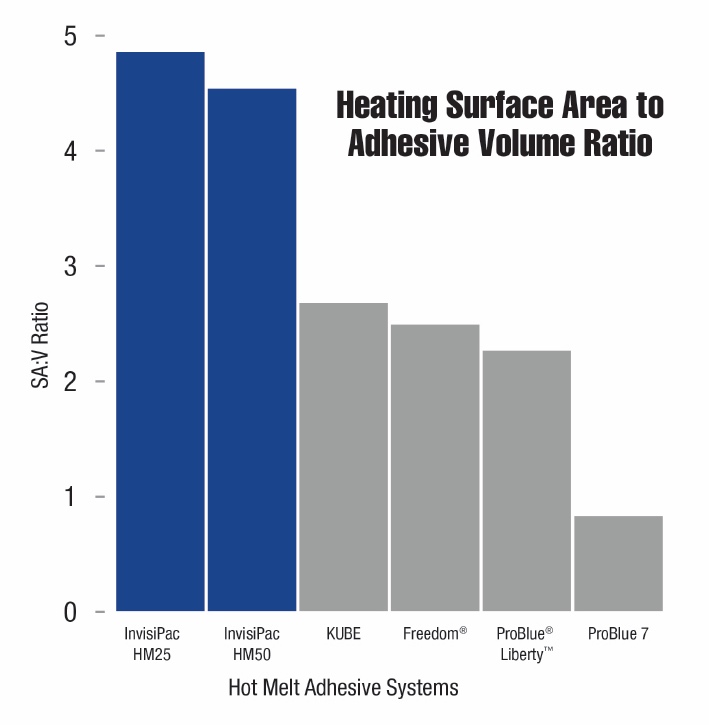
This graph compares the heating surface area to adhesive volume ratio of hot melt systems commonly used for end of line packaging. The two Tank-Free™, InvisiPac® systems have the highest ratio.
The Benefits of Vacuum-based, Tank-Free Technology
When you combine an integrated vacuum feed with Tank-Free™ heating in one hot melt system, you get the right amount of adhesive at the right time.
Traditional heated tanks store anywhere from 4 to 50 liters of molten glue, while Tank-Free designs heat less than two liters at a time. This brings the adhesive to temperature in less than 10 minutes. Such a quick startup time means more uptime – and profitability.
With a minimal melted volume, hot adhesive spends less time at temperature and is quickly replenished with a fresh supply. This drastically reduces char formation within the hot melt system.
Reducing char also reduces material waste and nozzle plugs, leading to less overall system maintenance and less production line downtime.
Related Articles
Fruit Packager Seals Cardboard Boxes with 64% Less Glue
The hot melt delivery system for a large fruit packaging house was causing major problems. The packaging manager explains how InvisiPac reduced costs and liability issues.
Refresco Achieves 45% Hot Melt Adhesive Savings
An operations manager and engineering manager for the world's largest independent bottler of beverages share how they reduced hot melt adhesive use by 45%. Since their factory yearly packages 1 million liters of soft drinks and juices, that is a lot of money.
Reduce Energy Consumption by 36 Percent
How much energy can be saved when dispensing hot melt adhesive with the InvisiPac HM10? An adhesive solutions company put Graco’s hot melt delivery system to the test for cardboard packaging.