Remote Chemical Management Offers New Flexibility for Wells and Pipelines
Chemical treatment plays a key role in maintaining trouble free operation of pipelines and well heads. Chemicals injected into pipelines and wells help prevent corrosion, freezing, and clogging. Because chemicals represent significant operating expenses, operators are keenly interested in managing these chemicals efficiently. Chemicals need to be procured, stored, and applied strategically to keep the oil or natural gas flow moving effectively and avoid costly downtime.
Traditionally, chemical management has required frequent field visits to monitor chemical tank levels, pump operation, and other conditions. With recent advances in technology, much of this can now be done remotely. Key data can be collected and distributed electronically, allowing operators to monitor and adjust chemical treatment from miles away.
Monitoring Tank Levels and Flows
Chemical levels can be monitored with sensors connected directly at the outlet of the bulk storage tank. A pressure transducer determines the pressure in the tank and converts this to an analog signal, which can then be sent to an electronic controller. The controller correlates the signal to a tank level, which can be relayed electronically via a web-based portal or a supervisory control and data acquisition (SCADA) system, allowing the chemical usage to be tracked remotely in real-time.
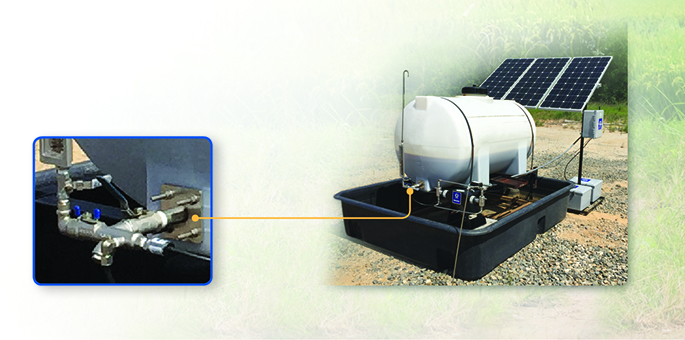
Flow can also be monitored remotely via the web portal. Since the controller knows exactly how much the pump moved based on plunger size, it will know how much was pumped over a 24 hour period. By comparing chemical tank levels and total pump volumes, problems can be readily identified before they become critical. If the values do not correspond within a given threshold, the controller will trigger an alarm and send a message to an operator.
By tracking flows and tank levels, chemical inventories can be monitored precisely, helping ensure supplies are in line with usage. As production goes up or down, analytics can be used to properly manage chemicals.
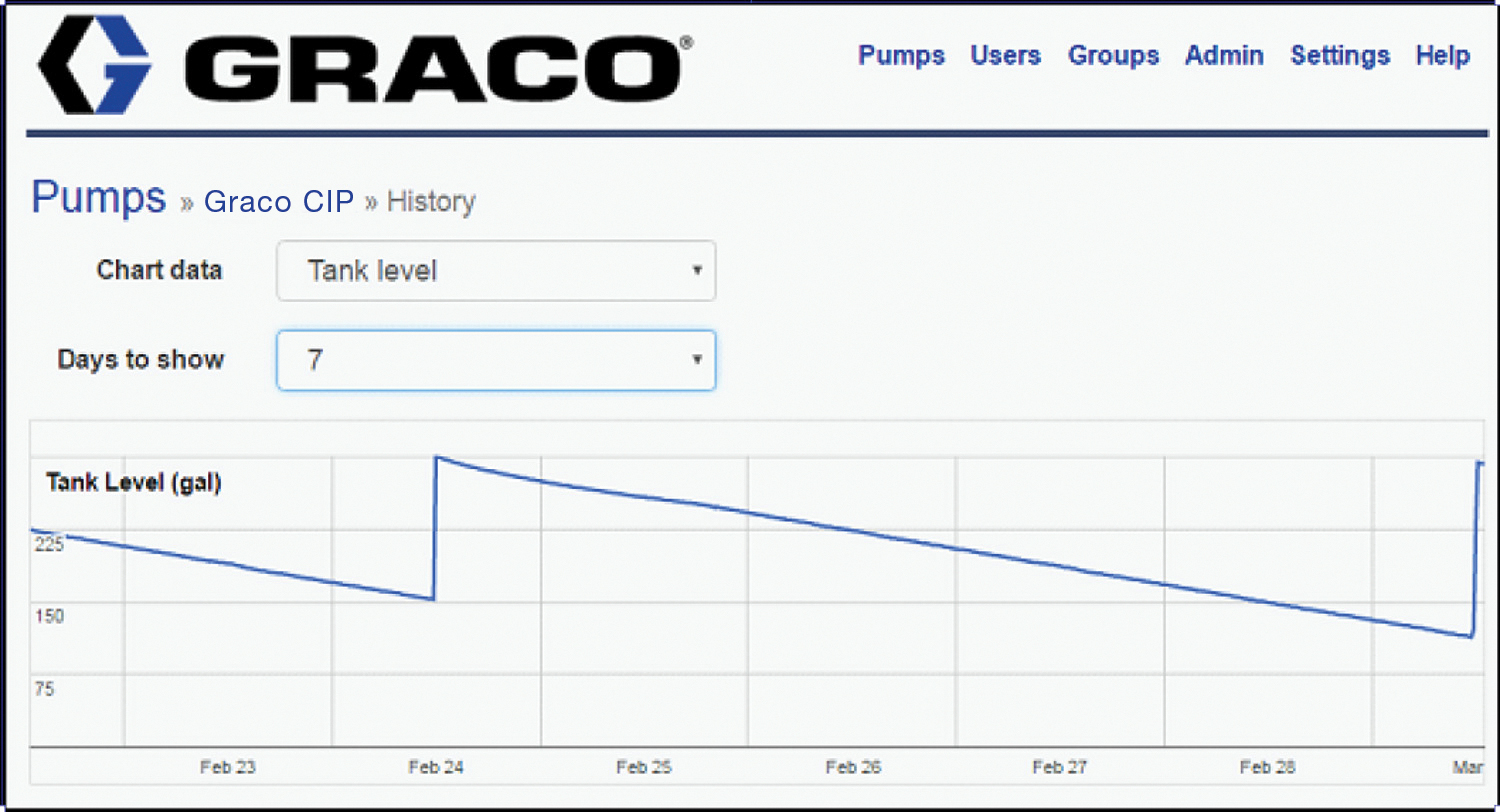
Controlled Pumping
Chemical injection is typically performed by electric or pneumatic pumps that inject the chemicals at certain rates. With pumps connected to the same controller that monitors tank levels and system flows, pumping can also be controlled remotely. Injection rates can be controlled via timed intervals, cycle count, or flow rates. Timed intervals will cycle the pump On and Off as necessary, cycle count will help the controller monitor pump cycles, and flow control will allow for more or less On time to help achieve flow rate targets.
Electric AC and DC operated pumps can provide pressures up to 10,000 psi (689 bar, 68.9 MPa) and flows up to 370 gallons (1400 liters) per day. Proper chemical dosing is critical to successfully reducing corrosion, freezing and plugging. Under-dosing can limit the effectiveness of the chemicals, while over-dosing can lead to waste and excess costs. When sizing pumps, it’s important to know what the volume and pressure output of the pumps should be, as well as the chemical compatibility requirements of the seals.
Controllers serve as the “brains” of chemical management systems, and can be selected based on power requirements, levels of automation desired, and other factors. In addition to controllers, pumps, and tanks, other chemical management components could include a solar panel, stand, batteries, and charge controller if solar power is used.
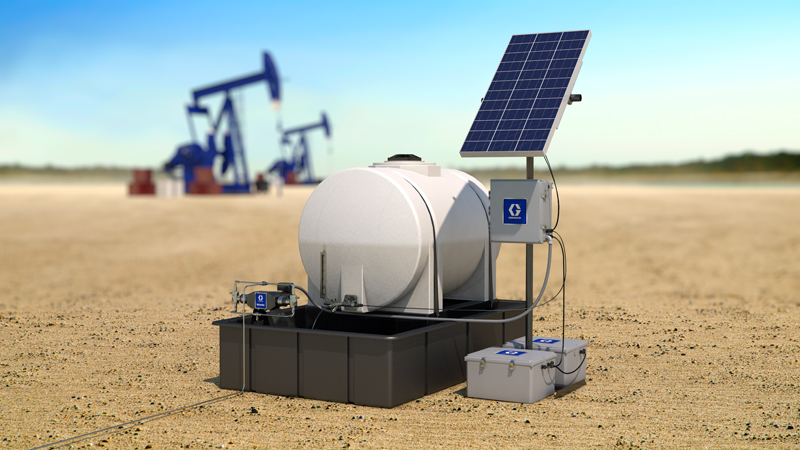
A chemical injection system in use at an oil-field site
Payback on Automation Investment
Automation of chemical management can produce a rapid return on investment. Assuming a modest cost estimate of $250 per field trip to a well site, a $1,500-investment in automation equipment is roughly equivalent to just six field trips. Add to this the value of ongoing monitoring of equipment and pumping conditions, and automation of chemical management becomes a key player in protecting the overall investment of oil and gas facilities.