Manufacturer Saves $500,000 with Rotary Bell Atomizers
Replacing Nordson RA20 with ProBell increases paint line speed and decreases solvent use.
Bell applicator technology pays for itself within a year
CUSTOMER: Architectural products finisher
GRACO EQUIPMENT: ProBell Rotary Applicator
CHALLENGE: The engineering manager of a large architectural products finisher too often stepped in paint. Overspray from their 17-year-old Nordson RA20 Rotary Atomizers was making puddles all over the production floor.
The worn out bell atomizers were causing terrible transfer efficiency. To get a satisfactory finish, operators had to run extruded aluminum parts through the production line as many as three times. That, paired with slow color changes, drastically slowed production and caused low employee morale.
To get morale and production back on track, any solution needed to integrate with their current programmable logic controller (PLC) system and be installed without losing any production.
SOLUTION: Aware that his current bells were the source of the problem, the engineering manager began to explore new options.
The company could not find any suitable technology updates in the newer Nordson models. This kept in the Graco ProBell and the Ransburg Aerobell rotary atomizers.
Although the Aerobell performed well, common replacement parts like bell cups and air bearings were much more expensive compared to ProBell counterparts.
On top of affordable parts and good performance, ProBell also offered a unique system logic controller. The company found the easy-to-use computerized control panel allowed for fast color changes and precise parameter settings.
With overall cost of ownership as a major decision maker, the ProBell looked like the clear choice.
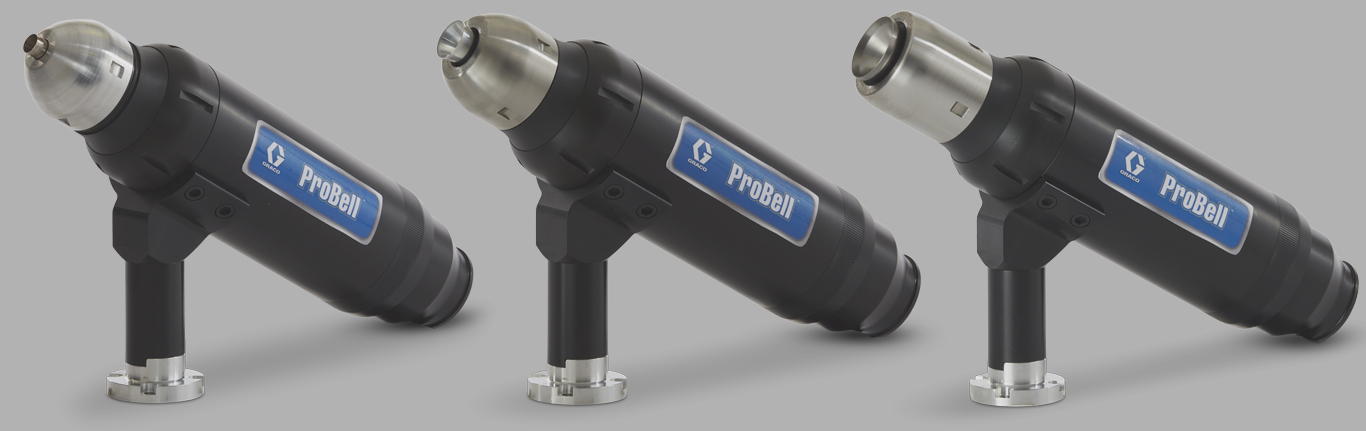
RESULTS: Graco engineers and technicians assisted in the installation and integration of six ProBells with the current PLC system, resulting in no downtime on a tight production schedule.
Immediately, operators were amazed by the finish quality, ease of use, and coverage of hard to reach corners, especially on aluminum extrusions.
Overall, line speed increased, and paint solvent use dropped by 15 to 20 percent. These improvements added up to an annual savings of over $500,000, paying for the new equipment within the first year.
All trademarks and registered trademarks are the property of their respective owners.
Free Webinar
Paint Line Optimization with Rotary Bell Atomization
Explore how the rotary bell atomizer can optimize your paint line, during this 35-minute on-demand webinar.
Contact an Expert
Related Articles
Upgrade Advances Paint Line Production and Innovation
New rotary bell atomizer air caps reduce downtime for cleaning and extend uptime for production.
4 Reasons Why You Need a Rotary Bell Atomizer
Automated finishing equipment increases quality and production, while reducing costs, and safety risks
Finishing Solutions for Aluminum Extrusions & Panels
Paint automation can improve quality and decrease cost.